In the electronics value chain, the packaging is a very early stage. The semiconductor foundries can either outsource packaging or do it in-house. In the last two years, the international semiconductor packaging industry has been impacted tremendously because of the strict lockdowns in various countries. Due to this scenario, the production of the chipset has been slumped. In fact, the massive disruptions of the supply chain ecosystem also severely affected the growth and demand of the semiconductor packaging sector. Experts have clearly added that slowly consumer electronics demand will be augmented and that will lead to escalating demand for semiconductor packaging. Numerous international firms are carrying out innovative strategies to deploy cutting-edge technologies in the packaging production process.
The high-end semiconductor devices, wafers, PCBs, ICs, LED chips, and electronic components are mostly imported from China and hence, the closure of manufacturing units in the region has augmented the costs of semiconductor components by more than 2-3 percent. This has led to a supply slump. Nonetheless, OME’s slow manufacturing and the decrease in demand of consumer electronics and smartphones have marginally impacted the semiconductor packaging industry. The delay in planned ventures and the decrease in capital outlays in several end-use industries have crashed the international economy. Also, during that time, semiconductor firms monitored the volumes of product demand and the production schedules have been altered to fulfill the urgent needs by deploying AI-backed technologies.
Why Advanced Semiconductor Packaging Gaining Prominence and The Growth
The growth and resurgence of artificial intelligence (AI) and the Internet of Things (IoT) and the sudden spike in demand for top-notch electronics spearheaded the cutting-edge application segment across the automotive and consumer electronics sector. Over the years, the packaging technology of semiconductors has been matured to reduce the costs involved and perk up the entire efficiency of Integrated circuits (ICs). Therefore, in the market, the vendors are surrounded by a huge challenge to offer efficient solutions in terms of the performance of the packaging, size, and on-time delivery aspects. Semiconductor packaging technology also plays a pivotal role in the defense and aerospace sector.
Sagar Sharma, Chief of Staff, India Semiconductor Mission (ISM) said, “When we speak about semiconductor design and manufacturing, packaging plays a very important role. The cost, power, performance, and normal functionality of all chips on a macro level are dependent on it. Basically, the container is the package where the semiconductor die is kept. After the COVID-19 scenario, many global semiconductor foundries are increasing their packaging units, which are now done by OSATs or vendors. The die is protected by the package, helps in dissolving the heat, and connects the chip to the board. Currently, the packages appear in various materials, which could be standard or custom and they can be furnished with active or passive cooling.”
As per a report by Future and Markets Insights, the semiconductor packaging market internationally reached a growth of CAGR 4.9 percent. In 2015, the overall market valuation of this industry reached US$ 19.1 billion, whereas by the end of 2021, the sector reached a growth of US$ 25.4 billion. Media reports further added that by 2030, the global market of this industry is speculated to reach $60.44 billion compared to $27.10 billion in 2020 which is increasing at a CAGR of 9.10 percent from 2021 to 2030. When speaking of the Asia-Pacific region, the market is expected to augment at a CAGR of 6.8 percent by grabbing a revenue of $19,078.5 million by 2028. The North American semiconductor packaging market generated $7,778.5 million in 2020 and is projected to register a revenue of $13,747.0 million by 2028.
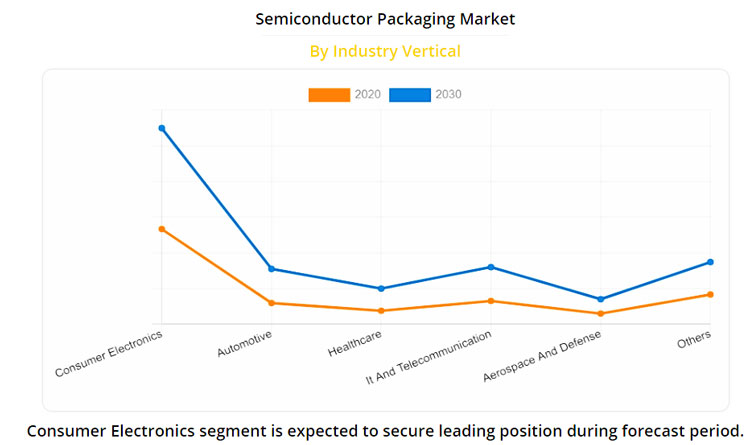
The global firms operating in this space are massively investing in key strategies such as alliances, expansions, and mergers and acquisitions to increase their worldwide share and presence. Also, new products are being unleashed by these firms to enhance their product range. For example, Intel back in 2022 associated with the University College London (UCL) to unveil a new touchless computer that can be controlled and operated by waving the hands, face, full body, and head. Texas Instruments on the other hand unveiled a new camera and sensor for the mist, rain, and snow for the radar of the vehicle during rough weather.
The Current Technical Challenges of The Global Semiconductor Packaging Industry
The semiconductor packaging industry is not new and has been there for more than fifty years, says experts. Slowly, new transistors and architectures started coming in the market and there are innovative ways of increasing the performance with the same transistors or a better one. This is where the major technology was centered and it was inside the chip. The process became a bit intricate because more complex electrical functionality was centered around the central processor. There were necessities of top-notch transistors and different voltage domains. And if the performance needs to escalate in a cost-effective way, all of that functionality cannot be kept into what is going to be a relatively big chip in a cutting-edge node and in that case, the wafers are going to be very costly.
The major problem is that most of the semiconductor companies do not have skilled designers to design a custom SoC for the entire marketplace. In order to have a full operation product, the IP blocks are required to be re-aggregated at the package level, if a chip is disaggregated. Now, this is where the package is being pushed to do an end number of things. Fine lines are needed to retain things integrated. The power and the thermal waste heat requires managing. If a device is power-hungry, more power needs to be delivered. This is where the packages are endowed with additional demands.
One of the major impediments is power utilization and dissipation. It’s hitting the packaging sector due to the integration at the package level. A huge amount of wasted heat is generated by Silicon, which is not thermally methodical. This is because the heat needs to be dumped somewhere else. Experts highlighted that a good participation is required between the package edge and the die. The most important thing from a technological perspective, additional voltage regulations and conversions are required in the package. Through this way, higher voltages can be fetched into the package and then weed them out into lower voltages.
Shanmugavadivel S, Founder at IcOnT Technology & Co-Founder of Tohands, said "Packing is more important as it determines the usability of the silicon wafers. Packaging is core thing that ensures the life time of the semiconductor, Heat withstanding and protect the wafers from environmental hazards. Now a days chip sizes are reduced very much, which is eventually due latest packaging process. First point i would say is infrastructure provided for fab is not enough. It requires a lot of capitals to establish the fab, in which the government is trying to subsidize that too. Second part is the availability of academic institutions which are more into semiconductors. Though India has few but not like Taiwan ,US or other countries established."
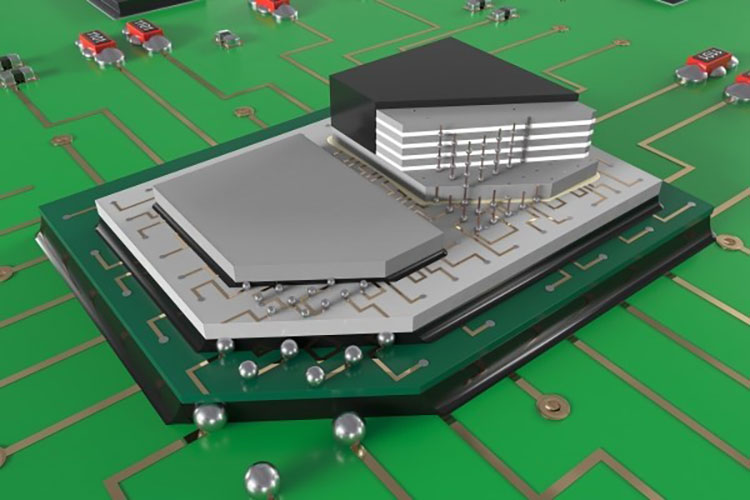
Where India Currently Stands in Semiconductor Packaging
Of late, a media report added that the semiconductor packaging industry in India is expected to craft a revenue opportunity of around US$ 1.7 billion during 2022-23. The All India Association of Industries (AIAI) stated that the nation has augmented its investment in defense and military by proclaiming a budget around US$ 67.4 billion during the union budget 2020-21. The investment has been increased to 10 percent when compared to the past few years. The increasing demand of semiconductors in this sector will escalate growth of the packaging industry in the country in the coming years.
Amid the government of India’s strong push to spearhead the growth and supply of semiconductors, packaging wafers will turn out to be the first node, which is going to be localized in the electronic component’s supply chain. In an interaction with the Economic Times, IIT-Madras director Kamakoti V and HCL founder Ajai Chowdhry mentioned that the packaging services like putting the wafers in casing and its shipment will be the most important thing that will start off. Now, when the investments are taken into consideration, the semiconductor packaging industry will make India an imperative part in the worldwide supply chain of semiconductors, used from luxury cars to phones.
Highlighting the importance of semiconductor packaging industry in India, Amitesh Kumar Sinha, Joint Secretary at Ministry of Electronics & Information Technology (MeitY) told CircuitDigest exclusively, “The growth in electronics manufacturing in India is happening immensely because back in 2014-15, the valuation was just 29 billion, and now, we have a target of 300 billion in the coming four years. In fact, the economy of semiconductors in the country is also growing around 110 million. So, you can imagine what kind of growth is happening. By 2030, the semiconductor industry is also poised to become a trillion dollar economy; around 450-500 billion economies exist in this industry. This is the right time for design and make products in India backed by incentive opportunities. Product design is the most important thing and the journey starts from there. In the semiconductor program, we have attributed 30 percent incentives for designing in India. Around 50 percent of the cost will be borne by the government from designing to testing and production of final products.”
To boost the growth further, homegrown electronics firm Sahasra Group has set up a memory chip assembly, test and packaging unit in the Bhiwadi region of Rajasthan with a capital outlay of Rs 150 crore, which in coming three years will increase to Rs 300 Crore. The plant is set to begin its operation from February 2023. Whereas, another home-grown firm Ruttonsha invested Rs 200 crore, which is under the compound semiconductor category. In Phase 1, the company aims to produce silicon wafers, phase 2 is about fabricating power electronic devices, and the unit is expected to commence its operation by March 2023.
In December 2021, the government announced a staggering Production Linked Incentive (PLI) scheme of roughly $10 billion dollar, which will offer an incentive of upto 30 percent on the capital expenditure for OSAT/ATMP. It is expected by the government that there would be 15 approvals for semiconductor packaging and compound semiconductors. And as per a report of the ET, Tata Electronics' Outsourced Semiconductor Assembly and Test (OSAT) is in discussions with several international OSAT vendors and semiconductor firms to invest into advanced packaging of semiconductors.
Speaking of the grave concerns in this industry, Dr. Sandip Chatterjee, Director & Scientist at MeitY told CircuitDigest exclusively, “The semiconductor industry has transformed tremendously over the past few years and it requires a very high-tech workforce. Advanced materials should be the main thrust area. We require more skilled manpower, research in a very matured way and there should be more IPs. From the ministry side, we are creating an ecosystem along with the industry where we are trying to create more deep tech startups. We also have a couple of centers of excellence in India on semiconductors.”
“What we are trying to do is solve the pain-points of research and final development of the products. Investment will come, but unless we are working on the technology side we cannot grow our market. In the last four decades, the government of India has invested heavily on R&D especially on IIMs and IITs. We have even created nano-centers in IITs. But findings reveal that in the last two decades the institutes were not focused and the industry was also not capable of absorbing the high-end niche research areas. In the last 5-6 years, industry has started taking interest. Earlier, IITs were taking initiatives of upto tier-III cities, which is now extended beyond that.” added Chatterjee.