The Future of Semiconductor Design: Trends Shaping the Next Decade
Pankaj Panjwani, CEO and Founder of KeenSemi, brings over 25 years of experience in semiconductor design, leading successful projects across domains like Physical Design, Machine Learning, Functional Verification and SoC/ASIC design. In 2016, he founded Keenheads to provide high-value semiconductor design services specializing in areas such as FPGA, embedded design and Design for Test. Recently, he shared his vision for the future of the industry in the article "The Future of Semiconductor Design: Trends Shaping the Next Decade". Below, we dive into his insights which outline the key trends set to define the semiconductor landscape in the coming years.
Semiconductors, the backbone of modern technology, are on the cusp of transformative growth. As industries worldwide integrate emerging technologies like AI, IoT, and quantum computing, the semiconductor landscape is set to evolve dramatically. There are several trends shaping semiconductor design over the next decade, with an emphasis on India’s burgeoning role.
Generative AI and the Demand for Advanced Semiconductors
Generative AI is poised to redefine semiconductor design and functionality. The global demand for AI-enabled chips is expected to grow exponentially, driven by B2B and B2C applications. By 2030, the compute demand for generative AI alone could surge by 25 times, with substantial growth in industries such as healthcare, automotive, and customer engagement systems. This demand underscores the need for advanced chips capable of handling vast computational loads while optimizing energy efficiency.
Artificial General Intelligence (AGI) and the Next Compute Frontier
While Generative AI has already transformed semiconductor demand, the emergence of Artificial General Intelligence (AGI) introduces an entirely new frontier. Unlike narrow AI, AGI aspires to perform tasks across multiple domains with human-like adaptability and reasoning.
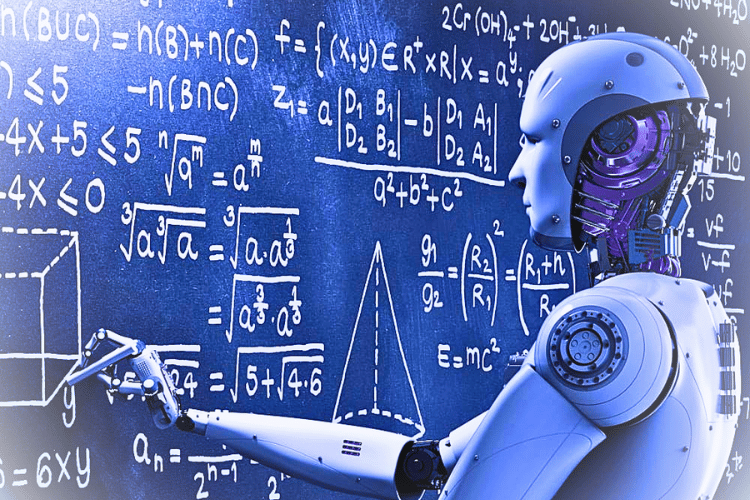
The realization of AGI will require unprecedented computational power, emphasizing ultra-advanced semiconductors capable of dynamic learning, real-time data processing, and massive parallel computations. AGI’s compute demands are expected to surpass those of generative AI, with specialized chips needing exponential improvements in processing speed and energy efficiency. This trend will drive innovation in chip architecture, including neuromorphic designs and quantum elements, enabling AGI’s multifunctional capabilities.
India’s Strategic Focus on Semiconductor Ecosystem Development
India, recognizing the strategic importance of semiconductors, has initiated robust policy measures to bolster its position in the global semiconductor market.
Key Initiatives Include:
- Semiconductor Manufacturing Incentive Schemes: Programs like the Semiconductor and Display Fab Ecosystem and Design Linked Incentive Scheme aim to attract domestic and international players.
- India Semiconductor Mission (ISM): This long-term initiative focuses on creating a sustainable semiconductor manufacturing ecosystem, supported by government subsidies and strategic partnerships.
- Cluster-Based Development: States like Gujarat are investing in semiconductor parks to enhance collaboration and resource efficiency.

With a projected 20% CAGR, India’s semiconductor market, valued at $27 billion in 2022, highlights its potential as a global semiconductor hub.
Chip Design Innovations: AI, IoT, and 5G
The convergence of AI, IoT, and 5G is driving innovation in chip design. AI accelerators, edge computing chips, and 5G-enabled processors are pivotal to the next wave of technological advancements. For instance, companies are developing semiconductors optimized for low latency and high bandwidth to support autonomous vehicles and smart city infrastructures.
Global Collaboration and Talent Development
India’s emphasis on fostering global partnerships has bolstered its semiconductor aspirations. Collaborations with countries like the US and Japan aim to secure supply chains, enhance R&D capabilities, and develop a skilled workforce. These partnerships are critical for India to bridge gaps in manufacturing and resource constraints.
Sustainability in Semiconductor Manufacturing
As the semiconductor industry scales, environmental concerns are becoming a priority. The focus is shifting towards sustainable practices, such as reducing energy consumption during manufacturing and developing recyclable materials for chip components. Indian startups are particularly active in this area, integrating green technologies into their designs.
Challenges and Opportunities
Despite Its Promising Trajectory, India Faces Several Challenges:
- Manufacturing Infrastructure: While India excels in chip design, a lack of advanced fabrication facilities limits its competitiveness.
- Capital Intensity: Semiconductor manufacturing requires substantial investment, which can deter smaller players.
- Supply Chain Dependencies: Heavy reliance on imports for raw materials and components remains a vulnerability.
Addressing these challenges through policy support, foreign investment, and innovation will be key to unlocking India’s full potential.
The Global Perspective
Globally, the semiconductor industry is expected to reach $1 trillion by 2030, driven by advancements in AI, quantum computing, and the proliferation of IoT devices. India’s contributions to this growth are increasingly recognized, especially as it aligns with global efforts to decentralize semiconductor supply chains.
India At The Helm Shaping The Future Of Semiconductor Innovation
The semiconductor industry stands at the intersection of technology and strategy, shaping the future of innovation. India’s proactive policies, coupled with its robust talent pool and strategic collaborations, position it as a critical player in the global semiconductor landscape. As challenges are addressed and opportunities harnessed, the next decade promises a transformative era for semiconductor design, with India playing a pivotal role.
Expert Q&A: Insights from Pankaj Panjwani in Discussion with Circuit Digest Team
Q. How is the rise of Generative AI and Artificial General Intelligence (AGI) increasing the demand for semiconductors in India, and how well is India prepared to take advantage of this growing demand?
Generative AI and AGI are transforming industries across the globe, driving an insatiable demand for high-performance semiconductors capable of handling massive computational loads while optimizing energy efficiency. In India, this demand is reflected in applications ranging from smart cities and healthcare to automotive technologies and customer engagement platforms.
India's preparation to meet this demand stems from its growing emphasis on semiconductor design expertise. The country has long been a global leader in chip design, and with the increasing adoption of AI in business and consumer technologies, Indian semiconductor firms are aligning their capabilities to develop AI-specific chips. For example, companies are creating edge computing solutions and AI accelerators to cater to domestic and global markets.
However, when it comes to manufacturing, India still faces significant challenges, including the absence of large-scale fabs and a reliance on imports for key raw materials. To address this gap, the government has launched strategic initiatives like the Semiconductor and Display Fab Ecosystem and the Design Linked Incentive Scheme. While these initiatives are promising, their effectiveness will depend on long-term execution, investments in research and development, and fostering partnerships with global semiconductor players.
Q. How do you believe India’s strategic initiatives like the India Semiconductor Mission and various manufacturing incentive schemes are helping position the country as a key player in the global semiconductor market?
India’s strategic initiatives are laying the groundwork for its emergence as a significant player in the global semiconductor market. The India Semiconductor Mission (ISM) is a standout effort, focusing on creating a sustainable ecosystem for semiconductor manufacturing and design. By offering government subsidies, incentives, and facilitating partnerships with global leaders, ISM is addressing critical gaps in manufacturing infrastructure.
Additionally, manufacturing incentive schemes like the Production Linked Incentive (PLI) Scheme and the Design Linked Incentive (DLI) Scheme have created a favorable environment for investment in semiconductor design and production. These programs aim to attract domestic and international players by reducing costs and encouraging innovation.
Cluster-based development in states like Gujarat, where semiconductor parks are being developed, promotes collaboration, resource efficiency, and knowledge sharing. Such measures, coupled with India’s reputation for a robust IT and software sector, strengthen its position in the global semiconductor supply chain. However, sustained investment in advanced fabrication facilities and reducing reliance on imported raw materials remain critical for achieving self-reliance.
Q. What do you think about India’s skilled workforce in the semiconductor sector? Are they ready to contribute to the country’s semiconductor evolution, or is there a need for more skill development to meet the challenges ahead?
India’s workforce has long been recognized for its expertise in engineering and IT, particularly in semiconductor design. With a substantial pool of engineers and researchers trained in chip design, verification, and embedded systems, India is well-equipped to drive innovation in this area. Organizations and academic institutions like the Indian Institutes of Technology (IITs) are producing top-tier talent that contributes to global semiconductor R&D efforts.
However, the evolving nature of semiconductor technology, especially with the advent of generative AI, AGI, and quantum computing, demands a workforce skilled in cutting-edge fields like AI chip architecture, neuromorphic computing, and photonics. To bridge this gap, there is a pressing need for enhanced skill development programs that focus on specialized training in semiconductor manufacturing, fabrication technologies, and advanced chip design.
Government and industry partnerships, such as training initiatives under the ISM and collaborations with global semiconductor leaders, are critical for equipping India’s workforce with the necessary expertise. With strategic skill development, India’s talent pool has the potential to drive its semiconductor aspirations and contribute to the global industry.