Join Rudy Ramos for a weekly look at all things interesting, new, and noteworthy for design engineers.
What are e-bikes, and what is their main purpose? E-bikes—electric bicycles equipped with electric motors to assist riders with propulsion—represent a fusion of technology with the traditional biking experience. Their assisted pedaling power makes cycling easier, more accessible, and downright fun. Pedal assistance can be particularly beneficial in covering longer distances, tackling hilly terrain, and arriving at destinations without excessive physical exertion or sweating, making e-bikes a practical option for commuting and urban travel.
E-bikes also offer an environmentally friendly alternative to cars for short to medium-distance travel, helping to reduce traffic congestion and lower carbon emissions. In fact, e-cargo bikes (i.e., e-bikes equipped with baskets for transporting goods) are perceived as an advantageous solution for urban last-mile logistics. Using e-cargo bikes is ideal for low volumes of goods and short distances in urban areas where access to conventional cars may be prohibited.[1]
Lastly, even with motor assistance, e-bikes still provide a form of exercise, as pedaling is typically required to engage the motor, especially on pedal-assist models.
This week, we take a quick look at different types of e-bikes, their regulations, and some of the embedded tech powering them.
Types of E-Bikes and Regulations
While there are various types of e-bikes, they generally fall into two main categories:
- Pedal-assist e-bikes amplify the rider's pedaling effort. They typically have a motor that activates only when the rider is pedaling, boosting to their natural pedal power. The amount of assistance can usually be adjusted, allowing the rider to choose how much help they receive from the motor.
- Throttle-based e-bikes have a throttle that can engage the motor without the need for pedaling, similar to how a motorcycle or scooter operates. This allows the rider to move forward using just the motor’s power.
With e-bikes making their way into parks alongside traditional bicycles, the U.S. National Park Service (NPS) has established regulations governing the use of electric bicycles within the National Park System. The NPS defines an e-bike as “a two- or three-wheeled cycle with fully operable pedals and an electric motor of less than 750 watts that provides propulsion assistance.” An updated memorandum includes additional requirements that an e-bike may not exceed 100 pounds or reach 20mph when powered solely by the motor, prompting many states to create their own regulations for e-bikes using a three-class system limiting the maximum assisted speed of e-bikes.[2]
- Class I: e-bike equipped with a motor that provides assistance only when the rider is pedaling and that ceases to provide assistance when the bicycle reaches 20mph
- Class II: e-bike equipped with a motor that may be used exclusively to propel the bicycle and that is not capable of providing assistance when the bicycle reaches 20mph
- Class III: e-bike equipped with a motor that provides assistance only when the rider is pedaling and that ceases to provide assistance when the bicycle reaches 28mph
The Tech Driving E-Bikes
The average range of an e-bike—the distance it can travel on a single charge—varies widely depending on many factors. However, most e-bikes can typically cover 40 to 80 kilometers (25 to 50 miles) on a single charge. This range can be influenced by factors such as battery capacity, motor efficiency, riding conditions, rider input, bike load, e-bike settings, and the overall condition of the e-bike, including the age of the battery.
E-bikes with larger batteries can store more energy, providing a longer range. Similarly, the efficiency of the electric motor plays a critical role in how effectively it uses battery power. Hills, headwinds, and rough terrain, in addition to the bike’s carrying load, all play a role in how much the motor needs to work. Also, the more a rider pedals and the less they rely on the motor, the longer the battery will last. Many e-bikes have different modes, such as eco, normal, and high power, impacting how much the motor assists. Over time, the battery’s condition can cause them to lose capacity, leading to decreased range.
In recent years, there have been several notable developments in e-bike technology, including lighter-weight designs with foldable features (Figure 1), higher capacity batteries with smart connectivity, upgraded safety features, and automatic gearing systems.
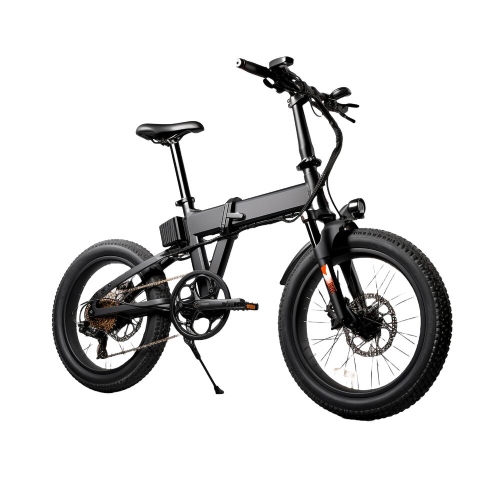
Modern e-bikes often feature smart systems that integrate digital technologies with physical components, enhancing user experience with advancements such as over-air updates, connectivity with apps like Bosch's e-Bike Flow App, and tracking personal cycling goals directly through the bike's system.
E-bike safety technology has also seen enhancements, including new anti-lock braking systems that are smaller and lighter, thus reducing accidents significantly. Additionally, there are innovations like digital anti-theft features, alarm systems, and tracking capabilities for enhanced security.
Additionally, the adoption of automatic gearing systems like that of the Enviolo® Harmony™, which has a number of advantages over traditional gearing systems,[3] has greatly simplified the riding experience and reduced the overall maintenance needs of e-bikes while also contributing to user-friendly e-bike designs.
All these technological developments reflect riders’ evolving demands and preferences, offering more efficient, versatile, and accessible options for a broader range of consumers. The e-bike industry continues to innovate, focusing on sustainability, user-friendliness, and technological integration.
The Newest Products for Your Newest Designs
This week’s New Tech Tuesday showcases gate drivers from Texas Instruments and Infineon Technologies. Both gate drivers are ideal for half-bridge brushless direct current (BLDC) motor drives and have built-in bootstrap diodes for the high-side capacitor.
The Texas Instruments DRV8300 and DRV8300-Q1 are components designed for three-phase BLDC motor control, commonly used in applications like e-bikes. These devices are essentially gate drivers that facilitate the motor’s control and operation by driving the gate terminals of the MOSFETs in the motor's electronic speed controller.
The DRV8300-Q1, specifically, is an automotive-grade version that offers robustness and higher reliability. It supports up to 100V operation, making it suitable for higher voltage applications. This series is known for its advanced protection features, ensuring enhanced system robustness, which is crucial in e-bike applications where safety and reliability are paramount. Additionally, these devices are designed to minimize noise issues and improve efficiency in motor operation.
Their use in e-bike applications is especially beneficial due to their efficiency in controlling the motor, contributing to the overall performance and reliability of the e-bike. This makes e-bikes equipped with such technology more efficient, safer, and potentially more powerful, enhancing the riding experience.
Next, the Infineon Technologies MOTIX™ 160V Gate Drivers are an advanced solution for motor control, particularly suitable for e-bike applications. These drivers are designed for half-bridge BLDC motor drives, a common configuration in e-bikes and other mobility applications. One of their key features is the ability to support a 100 percent duty cycle operation through a trickle charge pump, ensuring consistent and reliable motor performance. The gate drivers also boast protection features such as undervoltage lockout (UVLO) and overcurrent protection, which are crucial for the safety and durability of e-bike systems.
Furthermore, the MOTIX series emphasizes optimized efficiency and reduced electromagnetic interference (EMI), which are essential for maintaining the performance of e-bikes in diverse operating environments. The built-in bootstrap functionality of these drivers facilitates their use in high-power applications, making them ideal for more demanding e-bike designs that require robust power-handling capabilities.
Overall, the Infineon MOTIX 160V Gate Drivers provide e-bike and other e-mobility applications with enhanced control, efficiency, and safety features, contributing to their improved performance and reliability.
Tuesday’s Takeaway
E-bikes represent a fusion of traditional biking with advanced technology, providing an assisted pedaling experience that makes cycling more accessible, enjoyable, and practical. They serve as an efficient, environmentally friendly alternative for urban travel and commuting, offering numerous benefits for a diverse range of users. E-bikes have evolved with advancements in technology, leading to enhanced performance, safety, and versatility. These technologies allow e-bikes to achieve better speed control, more extended range, and overall improved riding experience.
Original Source: Mouser
About the Author
Rudy Ramos Rudy is a member of the Technical Content Marketing team at Mouser Electronics, bringing 35+ years of expertise in advanced electromechanical systems, robotics, pneumatics, vacuum systems, high voltage, semiconductor manufacturing, military hardware, and project management. As a technology subject matter expert, Rudy supports global marketing efforts through his extensive product knowledge and by creating and editing technical content for Mouser's website. Rudy has authored technical articles appearing in engineering websites and holds a BS in Technical Management and an MBA with a concentration in Project Management. Prior to Mouser, Rudy worked for National Semiconductor and Texas Instruments.