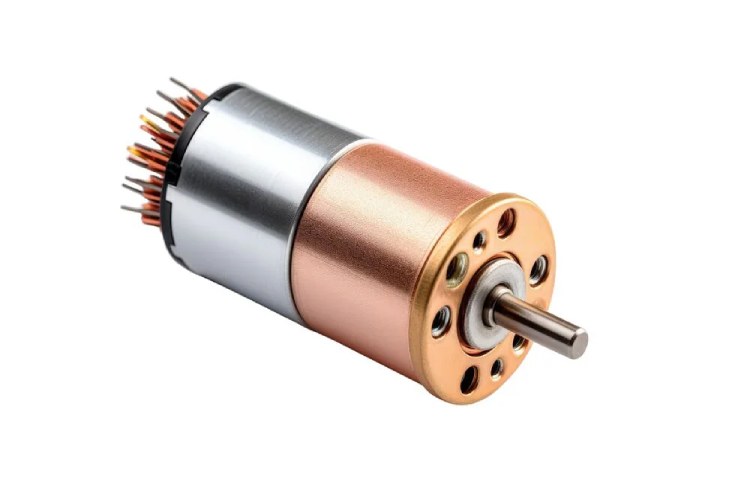
The broad world of DC motors has two basic categories: brushed and brushless. The brushed motor has been around since the 1830s (yes, that long!), and billions of them have been used successfully. However, the brushed motor also has many well-known drawbacks, including brush wear, electrical noise, and controllability issues. Despite these shortcomings, brushed motors have served us well for over 100 years and, for quite some time, were the only DC-powered motor option in many cases.
Several decades ago, the motor situation changed. This was a result of the brushless DC (BLDC) motor, which rose to prominence as electronic commutation was rising in popularity. This popularity was mainly due to two developments: high-energy permanent magnets and low-cost, efficient power-switch devices (MOSFETs and IGBTs) for their coils.
Many larger applications that previously used brushed motors transitioned to brushless designs or variable AC drives (a relative of brushless motors), while smaller motors often shifted to the stepper-motor approach (a close counterpart). Brushed motors appeared to be suitable only for low-cost, low-end, non-critical applications, such as disposable toys, window displays, and similar scenarios where high performance and reliability were not priorities.
Nevertheless, both motor types remain relevant depending on the application, and selecting the right motor size and type can be a challenge. This blog explores the nuanced decision-making process faced when choosing between brushed and brushless DC motors for various applications, considering factors like efficiency, control, and application-specific requirements.
Brushed vs. Brushless Motor Basics
What’s the difference between BLDC and brushed motor arrangements? As seen in the left diagram of Figure 1, the brushed DC motor relies on mechanical commutation to switch the polarity of the magnetic field between the rotor—also known as the armature—and the stator. The stator’s magnetic field is generated by either permanent magnets or electromagnetic coils.
The source current passes through coil windings on the armature. The interaction and constant reversal of the magnetic field between rotor coils and stator induces rotary motion. The commutation action, which reverses the field, is done using physical contacts that are called brushes. These brushes touch contacts on the rotor and bring power to the rotor coils.
The brushed motor can operate directly from the DC rails without any intervening driver or control electronics. This makes it suitable for basic, low-cost, non-critical applications such as simple toys or animated window displays.
In contrast, the brushless motor features an array of electromagnetic coils, called poles, that are fixed around the interior of the housing, with high-strength permanent magnets attached to the rotating shaft (the rotor), as shown in the right diagram of Figure 1. As the poles are energized in sequence by the required control electronics, a process known as electronic commutation (EC), the magnetic field surrounding the rotor rotates and attracts or repels the rotor, which is compelled to follow the field.
Figure 1: A brushed DC motor uses mechanical contacts to implement the commutation and alternating of the magnetic field (left). In contrast, the brushless DC motor design uses electronic commutation and has no wear-prone or EMI-generating moving contacts (right). (Source: Mouser Electronics)
While the current driving the poles can be a square wave, this approach is inefficient and induces vibration, so most designs use a ramping or curved waveform tailored for the desired combination of electrical efficiency and motion precision. Additionally, the controller can fine-tune the energizing waveform for quick yet smooth starts and stops without overshoot, ensuring a sharp response to mechanical load transients. There is a direct and visible relationship between the construction and operation of brushed motors. In fact, brushed motors are so straightforward that they are offered as STEM-focused kits in educational settings (Figure 2).
Figure 2: A classic brushed DC motor serves as a good teaching and demonstration fixture for electricity, magnetism, and motion basics. (Source: HENADZY/stock.adobe.com)
The Designer’s Tendency
Today’s reality is that when a designer needs a small motor with sub-fractional horsepower for a project, the natural instinct is usually to look at the wide range of standard brushless DC (BLDC) motors first and maybe, just maybe, also consider the brushed motor.
This approach makes sense for several reasons. For one, BLDC motors are easy to drive with modern controller ICs or embedded firmware. Moreover, matching the motor with necessary MOSFET drivers between the processor and motor poles is relatively simple. Lastly, they are reliable and generate minimal EMI due to the absence of sliding-contact brushes.
Therefore, in most cases, when a new product needs a DC motor, the designer’s natural inclination is to think brushless in many cases. However, that would be short-sighted. The reality is that brushed motors are still very viable and have their place in sophisticated designs as well.
Remaining Open-minded
When selecting a DC motor, engineers typically prefer the BDLC motor for most new designs because it has such an attractive combination of benefits and few drawbacks compared to the brushed motor. Designers can choose among many different ratings for voltage, current, torque, and more, while they can also select the needed hardware drivers and control algorithms—in software or embedded in firmware. In addition to basic motor-selection guides, vendors offer application software packages with graphical user interfaces (GUIs), making it easy to set the desired performance attributes such as speed, acceleration/deceleration profiles, and responsiveness.
In contrast, the brushed motor is more difficult to control with precision, and algorithms can only do so much and to a more limited extent. To improve performance, some brushed motor system designs add a rotary-position feedback sensor, such as optical, Hall effect, capacitive, or magnetic. However, this approach adds to the design cost, has mechanical-mounting issues, and increases control complexity. In fairness, while many BLDC installations do not need such a feedback sensor, it is also added in some cases to allow tight closed-loop feedback and more consistent performance.
Still, brushed motors are used for various designs ranging from legacy applications to sophisticated systems, such as automotive functions with well-defined velocity and torque requirements. Many vendors offer driver ICs for BLDC motors and variants suitable for brushed motors. Some vendors even provide automotive-specific, AEC-Q100-qualified brushed motor drivers for that demanding application, which is evidence of their continued viability.
Conclusion
Despite conventional engineering wisdom, brushless is always better for serious applications. In contrast, brushed may be suitable for less critical ones, but the choice between the brushed and brushless DC motor is not necessarily simple. A conscientious engineer will rank project priorities and their relative weight and give a fair look at the various alternatives before deciding which is best in a specific situation.