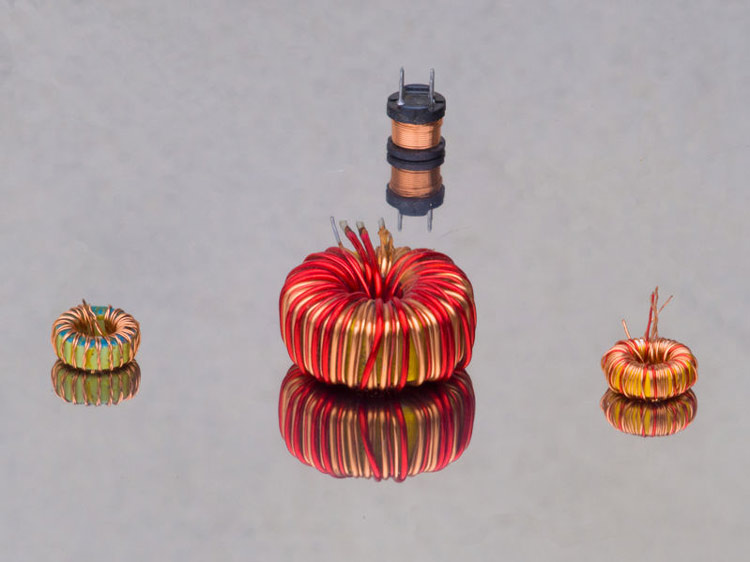
Every hobbyist wanting to dabble in radio has to – at some point – wind a coil or two, be it the antenna coil of an AM radio, a coil on a toroidal core for a bandpass filter in a communications transceiver or a centrally tapped coil for use in a hartley oscillator. Winding coils is not hard but quite time-consuming. There are different methods of making coils, depending on the area of use and inductance needed. Air cores are the most broadband but getting high inductances means using a lot of wire, they are also not the most efficient do to the magnetic field escaping the coil – this escaping magnetic can cause interference by inducting in nearby wires and other coils.
Winding a coil, over a ferromagnetic coil focuses the magnetic field, increasing the inductance. The ratio of inductance after and before a core with the diameter of the coil has been inserted inside it is called relative permeability (denoted μr). Different commonly used materials have different relative permeabilities, ranging from 4000 for electrical steel used in mains transformers, through around 300 for ferrites used in SMPS transformers and around 20 for iron powder cores used at VHF. Each core material should only be used inside of the specified frequency range, outside of which core starts exhibiting high losses. Toroidal, multi-aperture cores, pot, and other enclosed cores enclose the magnetic field inside the core, increasing efficiency and practically reducing interference to zero. To learn more about inductors and its working follow the link.
Air Cored Inductors
Air cored coils are good for low inductance coils, where interference is not of utmost importance. Coils with a small amount of turns and relatively thick wire are wound over a cylindrical object such as a drill bit or can, which is then removed and the coil supports itself, sometimes the coil is coated in resin for higher mechanical stability. Bigger coils with a lot of turns are commonly wound over a non-ferromagnetic former, such as a hollow plastic tube or a ceramic former (for high power RF coils) and then secured to the former with glue. To wind them you first need to calculate the required wire diameter, because it has a lot of influence over total coil length.
The formula for wire diameter is
(√I)*0.6=d, where I is RMS or DC current and d is wire diameter.
If the coils are used at low power levels the wire diameter is of not so high importance, 0.3mm is good for most applications and 0.12mm is good for canned if coils used are in transistor radio receivers. If the coil is used in oscillator service the wire should be stiff, to prevent warping effects as they can change the inductance to some extent and cause frequency instability (driving).
Next, you need to know what diameter the coil needs to have. It is recommended that the coil diameter is 50% to 80% coil length for optimum Q and those are dependant on how much space can the coil take up. If the coil will be self-supporting you can use a bolt or a screw, wind the turns inside the grooves and remove the bolt by unscrewing it while holding the wire of the coil, this makes a very even and reproducible coil.
Below is the Inductance formula for a cylindrical coil
L = µr ( n2 . ᴫ2 . r2 / l ) 0.00000126
L is inductance in henries, μr is relative permeability of the core (1 for air, plastic, ceramic, etc. coils ), n is the number of turns, π is pi, r is the radius of the coil in meters (from the middle of the wiring layer to the middle of the winding) or half of the diameter (from the middle of the wiring layer through the middle to the middle of the wiring layer on the other side), l is the length of the winding in meters, and the long number on the back is the permeability of free space.
Another formula for inductance.
L = ( n2 . d2) / 18d + 40l
This formula is used when winding a one-layer uniform coil with all turns being closely wound with no space between them. The units are the same as with the above formula, except d which is coil diameter in meters.
A very good calculator for coil has been made by Serge Y. Stroobandt, callsign ON4AA here.
How to make an Air-Core Inductor
To wind a regular air-cored coil you need a former, a source of wire, some fine sandpaper or a modeling knife (not shown) and a bit of superglue or double-sided tape to hold the wire in place.
After designing the coil it is time to wind it. If you are making an air-cored coil it is a good idea to use a plastic former to wind it on, since the plastic former is non-ferromagnetic and doesn’t conduct electricity it won’t affect coil performance at low power levels. Next, cut a strip of double-sided tape with the length of the coil and stick it to the former, then drill holes in the former where the coil ends and at taps, take off the cover layer on the tape and start winding, first by passing it through the hole you drilled then winding it, as usual, the wire will be held by the double-sided tape, alternatively, you can glue the begging of the coil to the former after winding a few turns with cyanoacrylate glue, wind the rest of the coil and glue every 1cm (also called super glue, use gloves, it is very hard to remove from skin and causes irritation). For taps, twist a length of the wire together, pass it through the hole in the former and continue as usual. Try to wind the turns close, after winding strip the enamel off using fine sandpaper or a modeling knife and tin the ends with a soldering iron. You can use an LCR meter to measure the inductance or a GDM, to use a GDM as an inductance measuring device see the linked article.
Below pictures explain the process of winding an Air-Core Inductor:
Step 1: Below two pictures show the Former with a bit of tape where the wire will be wound and Holes to hold the wire in place.
Step 2: In the below picture the Protective film has taken off, winding started and the wire for a tap is bend & twisted together.
Step 3: Then put through a hole in the former and out the other side.
Step 4: The finished coil has its wires tinned by submerging them in solder on a piece of PCB laminate.
Step 5: Finally the coil inductance is measured using an LCR meter. You can also use an Arduino to measure the inductance of a coil or can use a Grid Dip Meter (GDM).
Winding Coils on Ferrite Rods
Winding coils on ferrite rods (for example Ferrite Rod Antennas in radio receivers) is similar to winding air-cored coils, but since you can’t drill through a Ferrite rod you have to rely on the double-sided tape or glue to hold the wire tightly. Since the tape doesn’t always stick to the ferrite it is a good idea to first cover the rod with one to three layers of paper masking tape right under where the coil has to go and stick the tape over it. You can use super glue to hold the wire in place instead of double-sided.
To calculate the coil use the inductance formula for a cylindrical coil found above, for μr input the relative permeability found in the datasheet or an online coil calculator. If you designed the coil you can wind it like the air-cored coils, but there is a different method, faster method!
Put the ferrite rod in an electric drill, just like a drill bit and spin it slowly, the rod will rotate on its own, this way you can make high quality and high inductance coils with a lot of turns very quickly! If you have plastic formers for the rod, wind onto them first and then put them onto the coil and glue them in place.
On the left is a factory-made antenna coil in a broadcast receiver, where the coil is wound on a former that is secured to the rod using plastic elements. The wire is held in place with epoxy resin. On the right, there is a small coil on a ferrite rod made with the methods described above.
Toroidal Core Winding
Toroidal coils are quite easy to calculate, but a little bit tricky to the wind. Toroidal cores have a wide variety of applications, such as filter inductors in SMPS, RFI chokes, SMPS power transformers, RF input filters, baluns, current transformers, and others.
Toroidal coil inductance in nanohenries (When the AL inductance index is given in nH/N2) can be calculated by with this formula:
L(nH)=AL(nH/N2)*Turns2
After conversion, we get a formula for the number of turns needed for the required inductance:
Required turns = [L(nH) / AL(nH/N2)]1/2
To wind a toroidal coil you need a toroidal core, a source of wire (deflection coils from old CRT TV’s are a good source of it), some fine sandpaper and a bit of superglue.
To wind a toroid you first need to cut an appropriate length of wire, because you can’t pass a roll of wire through the hole. To calculate the wire needed, multiply the circumference of the cross-section of the ring by the number of turns needed. This is sometimes stated in the datasheet as mlt (mean length per turn). On the this website, there is an online calculator that aids in the design of toroidal coils, just choose your core, plugin the required inductance and it gives the amount of wire and turns needed.
Step 1: First pass one end of the wire through the hole, make sure that around 4cm stick out – this bit is called a pigtail.
Step 2: Wind the pigtail around the core, leave 1cm to 2cm off and secure the rest with superglue.
Step 3: Use the remaining length of wire to wind the rest of the coil, attach the longer end to a nail or a nail for easier winding.
Since the coil is expected to have a low inductance (around 3.6μH) in absence of a professional LCR meter it is better to use a GDM, as common micro-controller-based meters have very low accuracy when metering small inductances. A 680pF capacitor was connected to the coil in parallel, along with a small coupling loop. This circuit dipped at 3.5MHz (right), putting these values into a resonance calculator gives us around 3μH. On the left, the meter is set to a different frequency, outside of the circuit resonance.
Calculated coils can give very different results when made in real life, due to parasitic capacitances and parallel self-resonance caused by them.