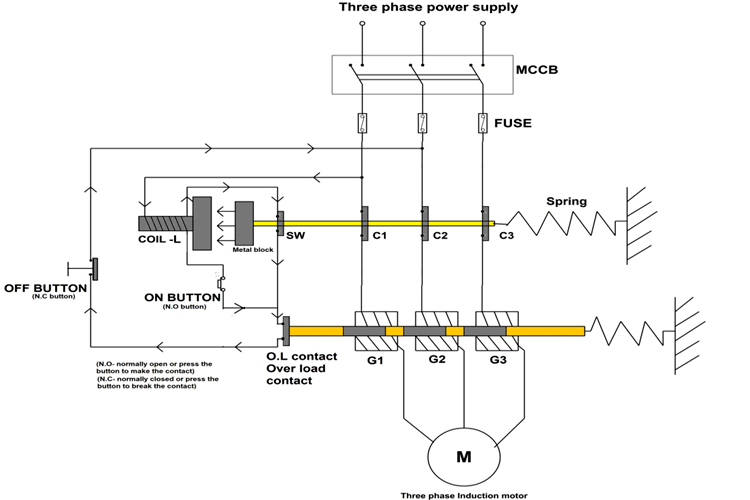
Direct Online Starter or DOL is a simple electromechanical system designed for switching and protection of Induction motors.
We all know that motors consume electric power horribly and this high power consumption is the result of current drawn by the winding of the motor. So higher the current drawn by the motor, the higher will be the power consumed by it and higher will be the heat generated. This heat will usually be dissipated into the environment through radiation or by direct contact conduction. But in some cases where there is no proper ventilation or the environment is hot, then the armature winding may burn because of excessive heat.
So the motor winding current needs to be monitored closely to avoid high current flow for long periods of time. So, to avoid the flow of high currents for long periods of time, motors are usually provided with protection systems of various types.
Usually, these protection systems are required for three-phase industrial motors that drive high power loads. And the Direct Online Starter is a mechanism that provides overload protection for three-phase squirrel cage induction motors.
The main functions provided by Direct Online Starter to Three-phase induction motor are:
- Over-current protection or Short circuit protection.
- Overload protection.
- Isolated motor switching setup.
Over-current protection or Short circuit protection: DOL starter consists of MCCB (circuit breaker) and fuse setup to disconnect the motor from the supply in case of a short circuit.
Overload protection: DOL starter consists of an electro-mechanical setup which will disconnect the motor from the power supply if the motor is overloaded or the motor draws current more than the rated value.
Isolated motor switching setup: Since high power motors are dangerous, the DOL starters are designed in a way that allows the customer to turn ON and OFF the motor indirectly.
The three features mentioned above are important for low and medium power induction motors used in industries. So DOL starters are popular and extensively used.
Direct Online Starter Working
For avoiding confusion, we will disassemble the original DOL starter and discuss about each of its sections.
The internal structure of Direct Online Starter Circuit we are discussing below is only for understanding the working principle, the original design of the starter may be different.
MCCB (Molded Case Circuit Breaker) and FUSE section:
The above figure shows the circuit connections between MCCB, fuses, and motor. The basic function of this section of the DOL starter is to protect the motor from faults and short circuits.
The MCCB here will be selected to match the motor ratings and in case of any fault in connections or motor windings, this MCCB will trip immediately disconnecting the entire system from the main power line. MCCB is usually the first protection layer for the entire system as shown above. These are also installed in our homes for safety.
The fuses in the circuit are present here to protect the motor and other devices from a short circuit. These fuses will blow up immediately in case of any short circuit and disconnect the motor from the power line. Also, the fuse rating must be chosen accurately to avoid irregular blow-ups during operation. This can happen in the case of massive inrush current during motor start up, so choosing appropriately rated fuses is important. Learn more about various types of protection circuits here.
Electromagnetic Contactor Section:
In the above figure, the internal structure of the contactor setup is shown which is present in 3 phase direct online starter and it is connected to an induction motor.
Here the three-phase power is connected to the motor through three normally open metal contacts namely ‘C1’, ‘C2’ and ‘C3’. So under rest conditions, no current flows in the circuit and the motor stays OFF. Also at this time, the ‘ON BUTTON’ will be open and no current flow through the coil.
Now, if we press the ‘ON BUTTON’, then the coil here will get magnetized because of the current flow as shown below.
Since the coil generates a magnetic field here, the metal block suspended with a spring will get attracted to the coil and moves towards it. Now that the metal block is moving, the entire contactor setup will also move along with it as shown in the figure.
As a result of this movement, the metal contacts C1, C2, and C3 will short the open terminals present between the power line and the stator terminals thus turning ON the motor. In more simple terms, after the button is pressed monetarily, the motor will get power from the source because of the movement of the three-phase contactor. Also, with the movement of the three-phase contactor, the spring will be stretched and it will be exerting a force on the metal block to place it back on its initial position.
After momentarily pressing the ON button and releasing it, the current in the coil, which should be zero, will still be flowing because there will be another path for the current to flow after the three-phase contactor moves to the final position. You can see in the figure a closed circuit formed for the current to flow through the ‘SW’ metal contact.
So after a single push of ‘ON BUTTON’ the three-phase contactor will self lock itself with the help of ‘SW’ metal contact and keeps the connection between three-phase power and the motor.
Now, to stop the motor, we will have to add another button to the above circuit as below.
Here the ‘OFF BUTTON’ will act as a short circuit in rest position and so there will be no change to the operation of the circuit we discussed above. But once the ‘OFF BUTTON’ is pressed, the circuit loop formed between the power line and coil will be broken, which results in current flowing through the coil to become zero. Now that current through the coil is zero, the coil will start demagnetizing itself and once the coil loses its magnetization completely the three-phase contactor moves back to its initial position because of the force exerted by the stretched spring. Obviously, now that the three-phase contactor moved back to rest, the supply voltage to the motor will be broken, resulting in the stop of rotor movements.
Even after the stop button is released, the three-phase contactor will stay in rest until the start button is pressed again to magnetize the coil. Hence we can conclude that using this setup, we can turn ON the motor forever by pressing one button and stop the motor forever by pressing the other button.
Overload Protection Section:
The key part of the overload protection section is the three coils G1, G2, and G3 as shown in the figure. These three coils carry the same current as armature winding as they are in series with the three-phase induction motor. So, whenever the motor draws the power from the power line, these three windings get magnetized. And whenever they get magnetized, the metal rings fixated on the shaft will be attracted by the coils. Normally, this will not be an issue but it will become prominent once the motor is overloaded.
So for understanding the function of this section, let us consider that the motor was turned ON sometime ago and is overloaded. Now with the motor is heavily loaded, the armature winding will draw heavy currents from the power source and thereby magnetizing G1, G2, and G3 coils heavily indirectly. In the presence of this heavy magnetic field, the metal rings will overcome the spring opposition to align themselves with their respective coils. And once the metal rings shift to the final position the ‘OL contact’ will also shift with them to break the loop of ‘COIL-L’.
So the end result of heavily loading motor is breakage of the current loop formed between the power line and ‘COIL-L’. We can see here that this basically functions the same as pushing the stop button we mentioned above. The end results in both cases are forever turn OFF of the motor.
Hence overloading the motor will lead to disconnection of power line and motor turn OFF.
Direct Online Starter Control Circuit
Up until now, we have studied the three sections each providing a special function. And we need to join these sections together to form a DOL starter.
Here you can see the final internal structure of the Direct Online Starter.
In the final conclusion:
- MCCB-FUSE section provides short circuit and fault protection for the motor.
- Three-phase contactor setup will provide simple and safe bi-stable switching of the motor.
- O.L contactor setup will protect the motor from overload burn out.
Advantages of Direct Online Starter
- Most economical and cheapest starter: Of all the starters present for three-phase induction motor, DOL starter is the most cheapest and economical one.
- Easy to operate: The starter has only two buttons for ON and OFF and a knob for setting the overload safety making it easy to operate.
- Easy maintenance: Since the internal structure of the starter is simple the engineers can easily find faults and rectify them.
- Since there is no startup protection the motor fixed with DOL starter provides 100% starting torque.
- The dimensions of DOL are small making it compact and reliable.
Disadvantages of Direct Online Starter
- Since there is no startup protection, the DOL starter does not limit the starting current.
- Unnecessary high starting torque during motor startup.
- Only suitable for low end and medium power motors.
- Since there is no startup protection the power line on which motor is connected will experience voltage dips during motor startup. This fluctuation in voltage may harm other electrical equipment feeding on the same supply.
- The motor is subjected to thermal Stress which affects the life of the motor.
- The mechanical stress on the motor is increased because of unnecessary high starting torque during motor start-up.
Dear Sir,
can we have a wireless operated switch schematic (either using Triac or Relays) to operate the 3-phase direct online switch ?
Thank you very much in anticipation