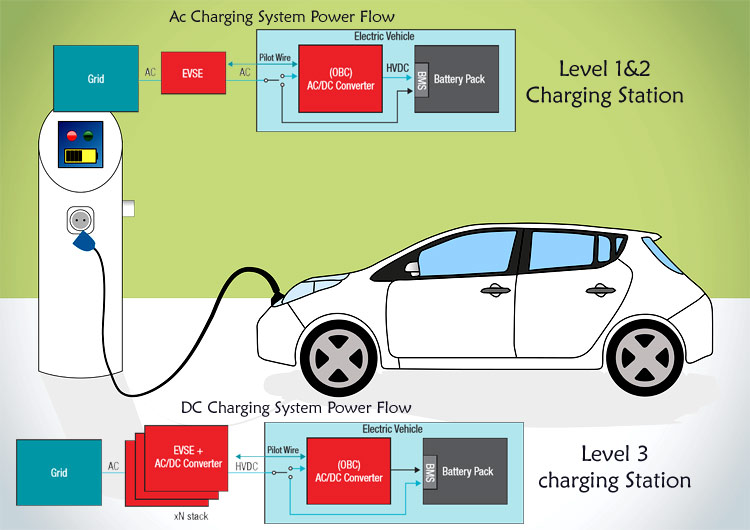
As the world is gearing up to unleash an EV revolution, it is still true that the rate of adaption is slow. Electric Vehicles (EVs) despite being a greener, smoother and cheaper mode of transport does not seem to be practical yet. The reason is two words, Cost and Ecosystem. Currently EV’s are priced substantially at par with Gasoline cars making it a less significant choice for buyers, the advancement in battery technology and government schemes are expected to bring down the cost of EV in Future.
The second part would be, there is no proper ecosystem for the buyers to use an Electric Vehicle without much hassle. With “Ecosystem” I am referring to the charging stations to charge your EV when you run out of battery juice. Imagine using a gasoline vehicle when you have no gas stations in your town and the only place you can refill is you home, adding to that you will need a minimum of 6-8 hours to charge a typical EV. Many companies like Tesla, EVgo, charge point etc have already acknowledged this problem by setting up charging stations around the country. With countries like Netherland, who promised to give up petrol engine by 2035 it is sure that the roads of future will be replaced with EVs over internal combustion engines and a lot of EV charging stations would pop up around us.
But, how does a EV charging stations work? Can a single charging station charge all types of Electric Vehicles? What are the types of Electric Vehicle charger? What protocols are followed for EV chargers? In this article we will discuss the answer for all these questions and also understand what constitutes an Electric Vehicle Charging Station and the subsystems behind it. Before going further you should read about the batteries used in Electric vehicle and how Battery management system works inside Electrics Vehicle.
Electric Vehicle Supply Equipment (EVSE)
The equipments that constitute an Electric Vehicle Charging Station are collectively called as Electric Vehicle Supply Equipment (EVSE). The term is more popular, and it refers nothing but to the charging stations. Some people also refer it as ECS which stands for Electric charging station.
An EVSE is designed and engineered to charge a battery pack by using the grid for Power Delivery; these battery packs might be present in an Electric Vehicle (EV) or in a Plug-in Electric Vehicle (PEV). The power, connector and protocol for these EVSE will vary based on it design which we will discuss in this article.
On-Board Chargers and Charging Stations
Before we step into charging stations it is important to understand what is present inside the EV and to which part the charger will be connected to. Most EVs today come with an On-Board charger (OBC) and the manufacturer also provides a Charger along with the vehicle. These chargers along with the on-board charger can be used by the customer to charge his EV from his house power outlet as soon as he/she gets it home. But these chargers are very basic and do not come with any advanced features and hence would normally take around 8 hours to charge a typical EV.
Types of EV Charging Stations (EVSE)
Charging Stations can be broadly classified into two types, AC charging Station and DC charging Station.
An AC charging Station as the name implies provides AC power form the grid to the EV which is then converted to DC using the On-board charger to charge the vehicle. These chargers are also called the Level 1 and Level 2 Chargers which is used in residential and commercial places. The advantage of an AC charging station is that the on-board charger will regulate the voltage and current as required for the EV hence it is not mandatory for the charging station to communicate to the EV. The disadvantage is its low output power which increase the charging time. A typical AC charging system is show in the below picture. As we can see the AC from grid is supplied directly to OBC through EVSE, the OBC then converts it to DC and chargers the battery through the BMS. The Pilot wire is used to sense the type of charger connected to the EV and set the required input current for the OBC. We will discuss more on this later.
A DC charging Station gets AC power form the grid and converts it to DC voltage and uses it charge the Battery pack directly by by-passing the On-board Charger (OBS). These chargers normally output high voltage of upto 600V and current upto 400A which enables the EV to be charged in less than 30 minutes as compared with 8-16 hours on AC charger. These are also called Level 3 chargers and commonly known as DC Fast Chargers (DCFC) or Super chargers. The advantage of this type of charger is its fast charging time while the disadvantage is its complex engineering where it needs to communicate with EV to charge it efficiently and safely. A typical DC charging system is shown below, as you can see the EVSE provides DC directly to Battery pack bypassing the OBS. The EVSE is arranged in stacks to provide high current a single stack will not be able to provide high current due to power switch limitations.
Normally the Level 1 chargers are meant for residential use, these are the chargers that are provided by the manufacturers along with the EV which can be used to charge the EV through standard house power outlets. So they work on Single phase AC supply and can output anywhere between 12A to 16A and takes about 17 hours to charge an EV of 24kWH. A Level 1 charger has not much role in charging stations.
The Level 2 charger is provided as an update for level 1 charger it can either be installed in house, on special request provided the house has split phase power supply or can be used in public/commercial charging stations as well. These chargers can provide upto 80A output current due to its high input voltage and can charge an EV in 8 hours. The Level 3 charger or Super chargers are meant for public charging stations alone. They require poly phase AC input from the grid and consume more than 240 kW which almost 10 times more than a typical Air conditioning unit in our home. So these chargers require special permission from the grid to operate.
The Level 2 and Level 3 chargers are considered to be more efficient than the Level 1 charger since the AC/DC and DC/DC conversion takes place in the EVSE itself. Because of the huge size and complexity of a Level 2 and Level 3 chargers they cannot be built inside a EV as it would increase the weight and reduce the efficiency of the EV.
Charging Station Type | Charger Level | AC Supply Voltage and Current | Charger Power | Time to charge a 24kWH battery Pack |
AC charging Station | Level 1 - Residential | Single Phase – 120/230V and ~12 to 16A | ~1.44 kW to ~1.92kW | ~ 17 Hours |
AC charging Station | Level 2 - Commercial | Split Phase – 208/240V and ~15 to 80A | ~3.1 kW to ~19.2 kW | ~ 8 Hours |
DC charging Station | Level 3 – Supercharger | Single Phase – 300/600V and ~400A | ~120 kW to ~240 kW | ~ 30 minutes |
Types of EV Charging Connectors
Just like the Europeans operate at 220V 50Hz and the Americans operate at 110V 60Hz the EVs also have different types of charging connectors based on the country it is manufactured form. This has lead to confusion among ESVE manufacturers as they cannot be made universal easily for all EVs. The main classifications of Connectors for AC chargers and DC chargers is given below.
AC Charging Sockets for Electric Vehicle:
Among the three the most common type of AC charging socket is the JSAE1772 socket with is popular in North America. As you can see the Plug /connector have multiple connections the three broad pins are for Phase, Neutral and Ground while the two small pins are used for communication between the Charger and the EV (Pilot Interface), we will discuss more about this later. The Mennekes or VDE-AR-E is used in Europe for three phase AC charging system and hence can output high power upto 44kW. The Le-Grand is also a similar socket with safety shutter to prevent debris from entering the charging socket. According to technical standards only the HSAE 1772 and the VDE-AR-E sockets are suggested to be used in all AC chargers of future.
DC Charging Sockets for Electrical Vehicle:
On the DC charger Side we have the CHAdeMO charger socket which is the most popular type of socket. It was introduced by Japan and soon adapted by France and Korea. Today most EVs like the Nissan Leaf, Kia etc have these types of sockets. The socket has two broad pins for the DC power rails and communication pins for CAN protocol. As we know Level 3 DC chargers do not use the on-board charger and hence have to provide the required voltage and current for the battery pack of the EV by itself. This is done by establishing a communication link (Pilot link) though Control Area Network (CAN) protocol with the BMS of the battery pack. The BMS then instructs the Charger to begin the charging process, monitors it and then requests the charger to stop charging.
The Tesla cars have their own type of chargers called the super chargers and hence have their own type of connectors as shown above. But they do sell an adapter which can convert their port to be charged with CHAdeMO or CSS chargers. The CDD charger is another popular charger socket which combines both AC and DC types of chargers. As you can see in the image he charger is split into two segments to support both DC and AC. It can support CAN and Power Line Communication (PLC) and is widely used in European Cars like Audi, BMW, Ford, GM, Porsche etc. It can support upto 400kW DC output and 43kW AC output.
EVSE AC Charging Station - Level 1 and Level 2 Chargers
The Level 1 and Level 2 Charging station simply has to supply AC power to the on-board charger in an Electric Vehicle which would then take care of the charging process; this might look on a first look. But they bear the responsibility of proving right amount of Power from the Grid as required by the EV battery Pack by communicating to it through Pilot wire. The subsystems present in a typical AC charging station represented in TI Training document is shown below.
The Level 1 chargers have a maximum output current of 16A because of the limitations of household power sockets, while the Level 2 chargers can provide upto 80A when operated in Three Phase supply. Both the Level 1 and Level 2 AC chargers normally use the SAEJ1772 standard plug connectors.
As you can see the AC Power Line (L1 and L2) are connected to the J1772 connector though a Relay. This relay will be closed to begin the charging process and opened when charging is completed. The Pilot Signal communication is used to detect battery status and the host processing system decides how much power should be supplied to the on-board charger. We will discuss more on this later.
The Power supply unit consist of an AC/DC converter which take in the AC power form grid and converters it to DC 15V using a switching circuit. This 15V is then provided to the Regulator which consists of a DC/DC converter which uses three different Buck Regulators to regulate 12V, 5V and 3.3V which is used to power the sensors, displays and controllers in the Charger Unit. The Measurement System consists of V/I Sense circuits which is used to measure the AC current and AC voltage. In the above block diagram a Current transformer (CT) is used to measure the input current but shunt or Flux method can also be used. The voltage is measured on either side of the relay to know if the relay is current open or closed. Since the measurement subsystem deals with AC voltage and current it is digitally isolated from the Host Processing Subsystem.
The Host Processing Subsystem consists of the main Microcontroller which receives the information from pilot communication and based on the information it triggers the Relay using Relay driver circuits. It also monitors the current and voltage using the values provided by measurement subsystem and takes corrective actions whenever required. This controller will also have a display unit, EEPROM and RTC to provide useful information like charging time, current status etc to the user.
Pilot Wire Communication in EVSE (AC charger)
In AC chargers the charging rate, that is the required input current, is actually decided by the EV itself. Not All EV’s require the same amount of input charging current and hence the AC Charger should communicate with the EV to know the required input current and perform a handshake before the charging could actually begin, this communication is called the Pilot wire communication.
Normally the AC chargers use the J1772 cable which has two points on the charger other than power lines. These two signal lines help the charger to communicate with the EV through +/-12V PWM signals. By default the signal pins on the EVSE output +12V, this when connected to an EV will get reduced to 9V because of a load resistor present in the Electric Vehicle, this signals the EVSE that the connector has been plugged into a EV. After this the EVSE will send a PWM signal of magnitude 12V and a duty cycle value corresponding to the maximum current it could deliver. If the EV is okay with that value of current then it performs a handshake by changing the load resistance and dropping the PWM voltage to 6V after which the charging begins.
The above graph illustrates the communication happening between the EV and the EVSE. As you can see initially when EVSE is not plugged in the EVSE output 12V, as soon as it gets plugged in it drops to 9V and the PWM signal is started. Here in this case, the duty cycle of the PWM signal is 50% meaning the available input current is 30A (Maximum capacity 60A). If the EVs on-board charger could work with this current then the EV signals a handshake by changing the load resistance and the PWM signal now drops to 6V. The charging begins at this point and will continue as long as the PWM signal oscillates between 6V and -12V. The EV will change its load resistance again when the charging process is complete to signal the charger to shut down.
EVSE DC Charging Station - Level 3 Chargers
The level three charging stations are more complex than the Level 1 and Level 2 since the DC/DC conversion for the battery pack has to be done by the EVSE itself. Since a DC EVSE bypasses the on-board charger it should know all vital parameters of the battery pack to charge it safely hence a CAN or PLC (Power Line Communication) should be established between a EVSE and the BMS of the EV. A Level 3 charger normally uses the CHAdeMO charger socket but other connectors like the J1772 Combined charging connector, Tesla connector are also being adapted by different manufacturers, these chargers can deliver upto 200A directly to your battery pack to charge the EV in less than 30 minutes. A typical simplified DC charging station Subsystem block diagram is shown below.
The system here is over simplified by removing the systems that we discussed earlier in the AC charging system. The Level 3 charger always works on a three phase AC supply, so the AC/DC converter has to take in the 3 Phase supply and convert it to 40V or higher DC. This DC voltage will then be stepped up to higher level (350 -700 V) as required by the battery pack. The Output Voltage and Current will be decided by the BMS of the EV which will then be communicated to the EVSE through CAN/PLC communication. Most of these level 3 chargers will be placed in charging stations for public access and hence a Human Machine Interface (HMI) arrangement gets mandatory. Some EVSE will also have wireless features like NFC, Bluetooth and Online payment gateway features etc to facilitate easy public usage.
The technology challenge lies with the AC/DC converter and DC/DC converter subsystems of the module. Since the charger draws in high current form the grid a proper Power Factor Correction system is required. Also the Converters are dealing with very high current and the power electronic switches inside them like MOSFET and IGBT cannot handle as a single unit. Hence normally the converter units are split into small units which are then combined in parallel to provide high current.
Advancements in EVSE
Few people arguably put forward that EVs are not completely green if they are powered by Electricity generated from non-renewable power stations like Coal, Nuclear etc. Good thing is that Solar Powered EVSEs are slowly getting popular. Due to the size, efficiency and weight of solar panel it is not possible to have EV’s directly run by solar power. But EVSE on the other hand can draw power from the Solar panel instead of grid. The downside though is huge initial cost and poor efficiency, since the power from solar has to be stored in batteries and then have to be transferred to EVs again. Also the efficiency of solar panel is very low (44.5% is the highest till date) and its technology still has to be developed to make it a affordable upgrade.
Another noticeable advancement is the Vehicle to Grid (V2G) system. Wherein the Battery Pack in a EV could act a Power source for household equipments. Today’s EVs come with a huge battery pack upto 100kWh or more making it an easy portable power house. So with the right inverter the power from these battery packs can be supplied to the grid during peak demand hours. Then these EVs can be driven to Solar powered stations to get them charged again, building a completely green eco system.
Setting up an Electric Vehicle Charging Station in India
With EVs getting quickly popular in India, we can already notice many EVSE set-ups popping up in major cities of India. With regulations still being standardized for India the following are the common problems with setting up an EVSE in India.
1. Low Charge Rate for Indian EVs: The EVs in India are still not ready for Level 3 or Super chargers as their battery packs do not support fast charging. How fast a battery could charge depends on its C rating, Indian EVs still have very low C rating that even a Level 2 charger is not required for most EVs. This will create less demand for public EVSE
2. Electricity Re-Sale Problem: According to norms you are not allowed for direct Re-Sale of electricity. Only the DISCOM is allowed to sell electricity. However with pressure from ISGF the Charging stations might be considered as an expectation for this in the future.
3. Weak Distribution Transformers: Most of the Distribution Transformers (DT) in India is already overloaded. An EVSE will consume high power from the grid making it a heavy problem. Hence the complete DT in that area has to be replaced with higher rating ones. This will be a major problem as new EVSE starts popping up in the city. You can read this whitepaper from ISGF to know more details about setting up an EV charging station in India.
Hi there! Today the onboard chargers looks to have good charging festures.
If i still need a onboard charger to do AC-DC conversion. Why the evse portable will be useful?