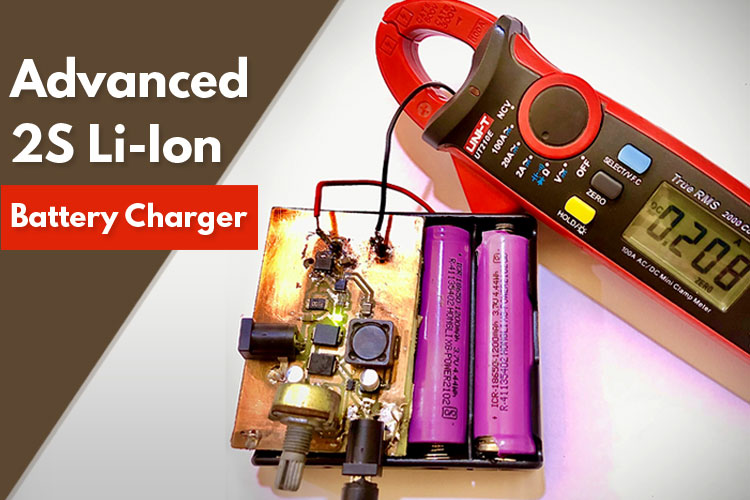
In this project, we are going to make a 2S charger module using the MCP73844 module from the microchip. The charger is capable of taking voltage between 2-12Volts and charge Li-ion and Li-Po batteries in a 2S configuration. The aim of this project is to develop a charging circuit that can be used as a subsystem in any consumer-grade project. The charger module can be connected with either a standard mobile adapter or power bank and it can also be powered with a 12 Volt charger. I will also tell you how we can use the same circuit to charge a single Li-ion or Li-Po cell by modifying a single component. In this project, I will design and fabricate the whole circuit in house, everything from circuit designing, PCB fabrication, and soldering SMD component is done in-house. We will also see how we can change the charging rate, heat dissipation, and other parameters in order to make the circuitry suitable for different use cases. We have previously made different battery chargers for different cell chemistries or having different features, if you are interested in that or to learn more about batteries, check the articles by clicking the links.
Battery Charger Circuit Overview
As mentioned above, the circuit can take any voltage between 2V to 12V, hence we are mainly focusing on a 5V input which is given by all the phone’s chargers, power bank, and even the computer’s USB port. The circuit is divided into 2 parts. When using a 5V input, the first step is to boost the voltage from 5V so that our charger IC can use it. We are boosting this voltage to 12 Volts. The boosted voltage is then fed into the charge controller circuit which then gives a controlled output to charge the battery.
MCP73844 Linear Charge Management Controller
The main heart of the system is the charger management controller IC. I have used the Microchip MCP73844 for this project. This IC belongs to the family of microchip’s linear management controller line MCP 7384x which has been specially designed to be used for low cost and space-limited applications. These highly advance ICs feature constant voltage (CV) and constant current (CC) charging techniques and unlike most low-cost products have features such as cell preconditioning, auto charge termination, charge indication, safety timer, and even optional cell temperature monitoring. The IC we have used comes in an 8-pin MSOP package and if you want the optional cell temperature feature, you can select either the MCP73841 or MCP73842. The application circuit of the MCP73843/MCP73844 modules is given below.
Figure 1 Li-Ion Battery charger circuit
The functional block diagram of our IC was taken from the datasheet is given below:
In the above functional block diagram, the 2 pins namely THREF and THERM are only available in the MCP73841/ MCP73842 which are used for monitoring the temperature of the battery, these ICs come in a 10 pin MSOP package unlike the 8-pin MSOP package of the IC we have used. Apart from these 2 pins the connection and functioning of all the 4 ICs are alike. The pin description of the ICs is given below:
Component Selection
The charger is highly customizable and we can select different charging rates, efficiency, etc. by choosing different passive components. The charging circuit we have designed is for a maximum of 2A/hour charging rate for 2S battery configuration. The maximum power would be given by integrating maximum output voltage (Vout_max) with max output current (Iout_max). Thus, the power will be 16.8 Watts. The connection for our IC is given below.
Here, The R3 resistor is acting as a shunt resistor. The output current is based on the value of this shunt resistor formula for which the value is given by Rshunt = VFSC / IFSC
Here, Rshunt is the value of shunt resistor
VFSC = fast charge voltage
IFSC = fast charge current
From the above equation, we can clearly say that the fast charge current is inversely proportional to the shunt resistance, and by changing the value of R3 we can achieve the desired output.
NOTE:
The resistor’s value will change the heat generation and power loss at this point which can be calculated by the formula P=R*(I*I)
PowerDissipation = 100mW ´ 1A^2 = 100mW
Thus, you have to take that into consideration while deciding the fast charge rate.
The MOSFET we have used is a P-channel MOSFET S19433BDY you can substitute this one with a Fairchild™ NDS8434 or IRF7404.
Battery Management Input Pin (VDD)
The VDD is the input supply that also prevents the draining of the battery when VDD supply is not present, it enters the power-down mode below a certain voltage threshold thus improving the life of the battery.
We have used a Schottky diode to prevent reverse current from flowing to the booster circuit.
Thermal Consideration
While selecting the components, you either have to limit the charging current or have to increase the copper pad size and include multiple vias to effectively dissipate heat for better and longer-lasting operations. There are design tradeoffs you’ll have to make while selecting the components.
Absolute Maximum Ratings
VDD -- 13.5V
All inputs and outputs w.r.t. -- -0.3 to (VDD+0.3)V
Current at DRV Pin -- ±4 mA
Current at STAT1 Pin -- ±30 mA
Maximum Junction Temperature, TJ -- 150°C
Storage temperature -- -65°C to +150°C
Parameters of our charger:
Parameters |
Rating |
Input Supply voltage (VDD) |
2V-12V |
Output Supply voltage (Vout) |
8.4V |
Max charging current (ISS_max) |
2A |
Charging start and stop threshold |
8.45-8.90V |
To make 1S charger:
If you want to design a charger for 1S battery or a single Li-Ion/Li-Po cell, you can substitute the MCP73844 with either MCP73841 or MCP73842. The MCP73841 will have the exact same circuit while the MCP73842 will just have an additional connection for temperature measurement. The remaining circuit will remain the same.
Booster Circuit using MT3608
As stated above, the operating voltage of our IC is between 8.7 V to 12 V, thus, in order to make this system compatible with a 5 V input, we need to design a booster circuit. Considering that this charger can be used in a consumer-grade product, the IC we have used is MT3608 which comes in a 6-pin SOT23 package, it features thermal overload protection, under-voltage protection, and current limiting while having high efficiency. The basic application circuit and efficiency curve is given below.
Technical Data of MT3608:
The pin diagram and function of each pin of the IC is given below-
Absolute Maximum Rating for MT3608
IN, EN voltages -- -0.3V to 26V
Operating Temperature -- -40°C to +85°C
FB Voltages -- -0.3V to 6V
Junction Temperature -- 160°C
SW Voltage -- -0.3V to 30V
Storage Temperature Range -- -65°C to 150°C
Peak SW Sink and Source Current -- 4A
The MT3608 IC is capable of taking input voltages as low as 2V. For our application, we have a fixed 5V input and the output we require should be lower than 12V, thus we will design the circuit according to our requirement. The schematics is shown below:
How to set the output voltage
The internal reference of our IC is 0.6V. The output voltage can be controlled by changing the values of resistor RV1 and R2 which is given by the formula-
If you want, you can use replace the pot with a fixed resistor of 50K ohm which will give you a constant output of 9.6V which will be suitable for our application.
Inductor values should lie between 4.7uH to 22uH. For higher efficiency of the booster circuit, the inductors must have a lower core loss at 1.2mHz frequency(working frequency of out MT3608) and low values of DCR. Both the input and output capacitors should be 22uC and ceramic capacitors with lower ESR values should be preffered. While selecting the diode the breakdown voltage value of the diode should be greater than the output voltage, hence a Schottky diode is a good choice for this application. Furthermore, the current rating of the diode should meet the root mean square of output current multiplied by peak current, which can be written as
For our case, we will use a Schottky diode with a current rating of 2Amps.
Some important consideration while placing the components in the PCB
- The input and output capacitors should be placed close to the IC.
- The main current traces should be kept short and wide (at least 20 mil)
- A common ground plane will help in reducing the noise and work as a heatsink too.
The components required for designing this circuit are:
Capacitors
- 2 x 22uF
- 2 x 10uF
- 1 x 0.1uF
Diode
- 2 x Schottky diode
- 1x LED
ICs
- 1 x MCP73844
- 1 x MT3608
Inductor
- 1 x 20uH
Resistors
- 1 x pot
- 1 x 3.3
- 1 x 100 mOhm
- 1 x 1k
MOSFET
- S19443BDA
Designing and Fabricating the Module
After selecting all the components, I drew a schematic using KiCad’s schematic editor Eschemia. The schematic is given below. As explained above the circuit is divided into 2 parts, a voltage booster circuit, and a charger circuit.
After completing the schematic, I exported the file to KiCad’s PCB editor. Keeping all the designing constraints in mind. I placed all the components and did a copper pour for common ground as shown in the figure below.
After checking the PCB connection, I took a printout of the PCB and using an iron box imprinted the prints on the copper clad. The imprint on the copper-clad was fine, thence I dipped the PCB in a ferric chloride solution and got the traces on the copper solution as desired.
Note: when using SMD components, always remember to take the mirror image of your PCB prints, because when you transfer the print from paper to the clad you will get mirrored print.
After checking the connectivity of the traces, I soldered all the components on the board and after it all that was left was testing the setup. You can download the Gerber file from the given link.
Testing the Circuit with 5V Input
For testing the circuit, I connected 2 li-ion cells with a nominal voltage of 3.7 V and 1200mAh capacity. Both the cells when connected in series were charged to 7.55V. I connected the setup and the charging light started glowing. For power, I used Apple’s 10W charger and connected it with a USB to DC barrel jack cable. The battery was connected for around 50 minutes before getting completely charged and the LED indicator turned off automatically indicating that the charge was complete.
When we measured the current flowing to the battery pack it maxed to about 1A and most of the time it was around 100mA-500mA. At maximum power, the battery was charged at around 9W of power.
Testing with 12V Input
When we powered the charger module with a 12Volt charger, the output voltage was around 8-10V but the current delivered was as high as 2.2Amp, which is more than 16W of power. Using this setup, the battery might heat up a bit during the fast charge phase, but that should not be a problem and should not degrade the life of the battery.
Final Verdict
This is a very simple yet effective circuit that can be used in a consumer-grade product. The size of the whole system can be effectively decreased, but because we were trying to fabricate it in-house, we did not place the components very close to each other. The charging module has very high efficiency and has many features such as preconditioning of battery which is not available in cheaper options, this feature replenishes the over-discharge battery in a controlled manner thus improving the life of your battery. This highly customizable design can really improve the overall efficiency and health of your battery pack.