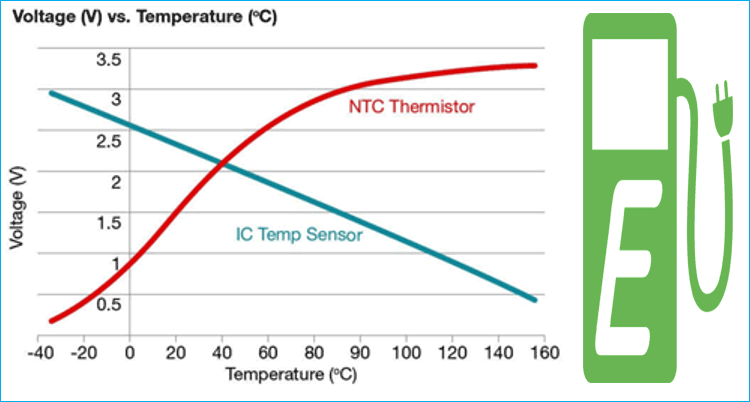
Automotive manufacturers all over the world are focused on vehicle electrification. There is a need for cars to charge more quickly and have a more extended range on a single charge. This implies, electrical and electronics circuit within the vehicle should be able to handle extremely high power and manage losses effectively. There is a need for robust thermal-management solutions to ensure that safety-critical applications remain operational.
In addition to heat produced by vehicle by itself, just think of all the thermal tolerance that your car and its electronics must have in order to handle wide ambient temperature ranges. For example, in India coldest regions face temperature much below 0°C during winter and it could be exceeding 45°C during summer for some other regions.
Each subsystem within an Electric Vehicle (EV) requires temperature monitoring. On board charger, DC/DC converter and Inverter/motor control require safe and efficient control to protect the power switch (MOSFET/IGBT/SiC). Battery management systems (BMS) also require fine resolution of temperature measurement on cell level. The one component that must be accurate at extreme temperatures in order to protect the system is no doubt the temperature sensor. Accurate temperature information allows the processor to temperature-compensate the system so that the electronic modules can optimize their performance and maximize their reliability no matter the driving conditions. This includes temperature sensing of power switches, power magnetic components, heat sinks, PCB, etc. Temperature data also helps to run cooling system in a controlled manner.
Negative temperature coefficient (NTC) and PTC (positive temperature coefficient) thermistors are among the most common devices used to monitor temperatures. The NTC is a passive resistor, and the resistance of an NTC varies with temperature. More specifically, as the ambient temperature around an NTC increases, the resistance of the NTC decreases. Engineers will place the NTC into a voltage divider with the output signal of the voltage divider read into the analog-to-digital converter (ADC) channel of a microcontroller (MCU).
However, there are a few NTC characteristics that can make it difficult to use in an automotive environment. As previously mentioned, the resistance of an NTC varies inversely with temperature, but the relationship is nonlinear. Figure below shows an example of a typical NTC-based voltage divider.
When you consider the heat generated from various subsystems within EV and climates that exist in different regions of the world, it becomes clear that a vehicle’s semiconductor components will be exposed to a wide range of temperatures (-40°C to 150°C). Over a wide temperature range, the nonlinear behavior of the NTC will make it difficult to reduce errors as you translate a voltage reading to an actual temperature measurement. The error introduced from an NTC’s nonlinear curve lowers the accuracy of any NTC-based temperature reading.
An analog output IC temperature sensor will have a more linear response when compared to NTCs as shown in the figure above. And MCU can easily translate the voltage into temperature data with more accuracy and speed. Finally, analog temperature sensor ICs often have superior temperature sensitivity at high temperatures compared to NTCs. IC temperature sensors share a market category with other sensing technologies like thermistors, resistance temperature detectors (RTD) and thermocouples, but ICs have some important benefits when good accuracy is required over wide temperatures like the AEC-Q100 Grade 0 range (-40°C to 150°C). First, the accuracy limits of an IC temperature sensor are given in degrees Celsius in the data sheet across the full operating range; conversely, a typical negative temperature coefficient (NTC) thermistor may only specify the resistance accuracy in percent at a single temperature point. You would then need to carefully calculate the total system accuracy for the full temperature range when using a thermistor. In fact, be careful to check the operating conditions specifying any sensor’s accuracy.
When selecting an IC, keep in mind that there are several types – with various merits for different automotive applications.
- Analog output: Devices like the LMT87-Q1 (available in AEC-Q100 Grade 0) are simple, three-pin solutions that offer multiple gain options to match best with your selected analog-to-digital converter (ADC), which lets you determine the overall resolution. You also get the benefit of low operating power consumption that is comparatively consistent over the temperature range vs. a thermistor. This means you don’t have to trade off power for noise performance.
- Digital output: To further simplify your thermal management implementation, TI offers digital temperature sensors that will directly communicate temperature over interfaces like I²C or Serial Peripheral Interface (SPI). For example, TMP102-Q1 will monitor temperature with an accuracy of ±3.0°C from -40°C to +125°C and directly communicate the temperature over I²C to the MCU. This completely removes the need for any sort of look up table or calculation based on a polynomial function. Also, LMT01-Q1 device is a high-accuracy, 2-pin temperature sensor with an easy-to-use pulse count current loop interface, which makes it suitable for onboard and off board applications in automotive.
- Temperature switch: Many of TI’s automotive-qualified switches provide simple, reliable over-temperature warnings, for example TMP302-Q1. But having the analog temperature value gives your system an early indicator that you can use to scale back to limited operation before getting to a critical temperature. EV subsystems can also benefits from the programmable thresholds, ultra-wide operating temperature range and high reliability from in-circuit operational verification of the LM57-Q1 due to the harsh operating environment (both ICs are available in AEC-Q100 Grade 0). For complete portfolio of IC based temperature sensor parts, you can visit : http://www.ti.com/sensors/temperature-sensors/products.html
In most of the EV subsystems, MCU is isolated from power switches and other components of which temperature is being sensed. Data coming from a digital output temperature sensor can be easily isolated using simple digital isolators like ISO77xx-Q1 family of devices from TI. Based on number of isolated digital communication lines required and the isolation a suitable part can be selected from here: http://www.ti.com/isolation/digital-isolators/products.html.
Below is block diagram of TIDA-00752 reference design which provides digital pulse output over an isolation barrier.
In summary, NTC thermistors are often used to monitor temperature, but their nonlinear temperature response can prove problematic for automotive solutions. TI’s analog and digital temperature sensor solutions enable you to both accurately and easily monitor the temperature of many automotive systems.
About the Author
Mr. Mahendra Patel started his career in semiconductor industry with Texas Instruments 6 years ago. As a field engineer, he supports multiple customer and application in automotive sector. He enjoys working on designs related to Electric vehicles and automotive lighting.