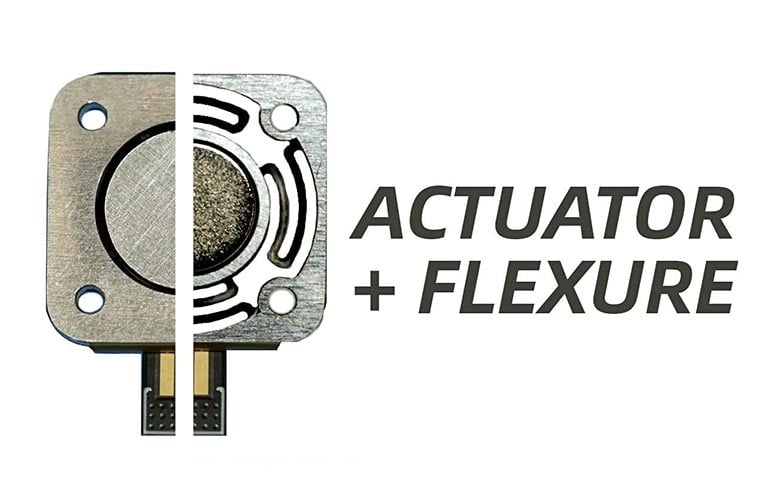
In a groundbreaking project, a creator named Carl bugeja has ingeniously combined flexure bearing mechanisms with magnetic PCB (Printed Circuit board) actuators, pushing the boundaries of miniaturization and exploring novel applications. The project was sparked by the development of a magnet-based actuator enclosed within a 3D printed housing and a PCB coil, which demonstrated both promise and limitations. The initial actuator's height constraint led him to experiment with flexure geometries, aiming to reduce thickness while maintaining functionality.
The project's core involved meticulously designing and testing various flexure geometries using Fusion 360, resulting in a comprehensive array of 40 different prototypes. These prototypes showcased diverse flexure configurations, including 14-arm spirals, 8-arm circular designs, springy variations, and 4-arm zigzag springs. His extensive exploration allowed him to fine-tune parameters such as width, thickness, and material composition, utilizing standard two-layer flexible PCBs as the foundation.
Throughout the testing phase, challenges and successes emerged. Some flexure designs proved too fragile to assemble, while others exhibited excessive stiffness, rendering them unsuitable for the intended coil actuation.
However, the 4-arm zigzag spring flexure displayed promising performance, showcasing the most effective balance between flexibility and stability. The selection of non-copper flexures with an aluminum frame was deemed optimal due to its weight and mounting capabilities.
An integral aspect of the project was redesigning the actuator for practical applications. Using Altium Designer, the creator protected the fragile flexure mechanism within a circuit board housing. While the force actuator concept faced limitations in lifting capacity, the actuator demonstrated potential for creating buzzers, speakers, and haptic feedback devices. Additionally, integrating capacitive touch technology further extended its versatility, although thermal efficiency emerged as a concern.
Further experimentation led to concepts like laser galvanometer-like movement using multiple coils and pop-up displays inspired by 3D printing techniques. Challenges were met as stability issues and magnet placement complexities emerged, indicating the need for further refinement. He contemplated potential applications ranging from innovative displays to tactile interfaces, acknowledging the challenges and possibilities inherent in these uncharted territories.
In conclusion, this pioneering project seamlessly integrated flexure bearing mechanisms with magnetic PCB actuators, propelling the field of miniaturized technology forward. The project's meticulous construction and testing of flexure geometries underscore the delicate balance between fragility and functionality. Despite facing obstacles, the project's results illuminate a promising path for diverse applications, from haptic feedback solutions to potentially groundbreaking display technologies. As the project creators continue to refine their designs, the technological community eagerly awaits the realization of their innovative ideas.