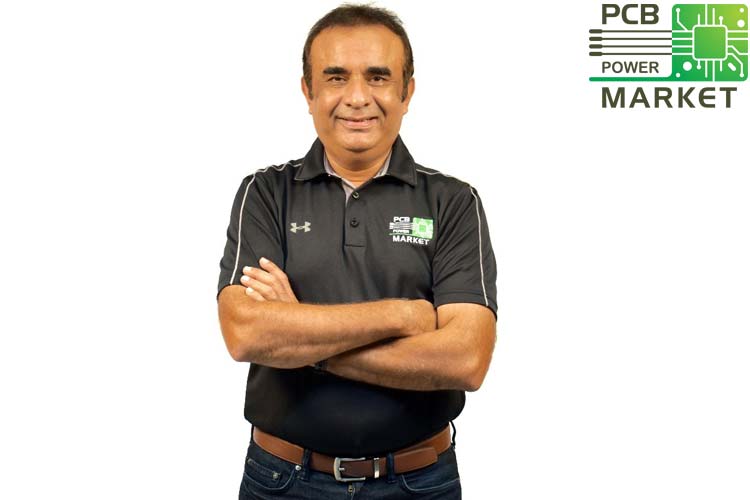
Printed circuit boards are one of the most crucial components in the electronics industry. Customized PCBs acts as an electrical connection and mechanical support for the components, reducing error in construction and speeding up the process. It not only makes electrical connections simple but also plays a crucial role in speeding up the manufacturing of electronic modules. They act as a canvas for an electronics engineer where the process of designing & planning a printed circuit board, also known as PCB Layout is done. Albeit being used in our everyday electronics gadgets, we don’t have much knowledge about PCBs and it’s manufacturing. To learn more about it, Mr. Paresh Vasani, CEO of PCB Power Market India spoke to Circuit Digest about different aspects of PCB production.
Q. Please tell us about your company and the vision with which you started the company?
PCB Power is almost a 25-year-old company, manufacturing Printed Circuit Board in Gandhinagar, Gujarat. Our vision is to become the de facto standard partner for customers in the area of electronics manufacturing, and electronics innovation, where we can provide value to our customers. We have been manufacturing printed circuit boards, double-sided multi-layer, special technology, high-frequency boards, including Rogers and other materials for many years.
When we started the company, the Indian electronic industry was completely different than what it is now and was more driven by government requirements. CDot wireless was the primary consumer of PCBs all over India and was funded by the Government of India from the Department of Telecom (DoT). CDoT was responsible for connecting each and every city, town, or village, across the length and breadth of the country. There was a huge demand and a lot of companies were relying entirely on the zero markets, which was a very good business for most of us. Later, the reforms started coming in, and then India started opening up with global players that changed the entire landscape of the Indian electronics industry. There was a big shift from CDOT volume-based business to a private company, electronics requirement, especially for the components, including PCB that changed the entire way of doing business because now we as a PCB vendor had to approach private customers which is a lot different than a standard government procedure, where tendering was a standard way of getting and coding the orders. There are a lot of different ways of doing things when it comes to that and then we change our strategy and decided to focus more on a prototype small and medium volume for our customers. We realized that there is a possibility for us to make a difference for our customers and bring value to our customers. After that, a few years back, we started PCB assembly also where we offer customers, not only the PCBs but also give them a high-class world-class quality for PCB assembly, including component sourcing.
Q. How does PCB manufacturing take place, and what kind of machinery is used in the process?
Most of the customers don't really have much idea how the PCBs are made. It is a make to Order product in electronics supply chain, where most of the other components like capacitors, resistors, semiconductors, they are all available at stock. There is a manufacturing process to produce PCBs with specific specifications and the standard products which based on the design requirement, customer choose and order those . In our case PCBs are made after we receive the order, So, the customer sends the design that we study and process the design before manufacturing in order to avoid compromising on any of the requirements from the customer and then we make boards.
The process has to go through many stages as for double side and multi-layer boards, the process can be divided into 8 to 18 different stages based on the specification. These processes are sequential, so we cannot go from step 1 to step 5, and it has to do as per the requirement of the customer.
We start with the basic fundamental raw material of PCB which is called copper clad laminate. It is nothing but copper on both sides, and in between, there is epoxy, a resin, and a fibre glass cloth that gives strength and insulation to the PCB.
The copper-clad goes through the following steps. First, there is drilling, plating, etching and then we apply the solder mask, which gives the PCBs green color and the most popular is a green-colored solder mask. The solder mask can be white, blue, red, or even transparent, depending upon the customer’s specifications. After this, it goes for different surfaces and finishes Hot-air Solder Leveling (HASL), Electroless Nickle+ Immersion Gold (ENIG), ENEPIG, etc and then it goes to legend printing. At last, PCBs are routed as per the requirement of the mechanical dimensions, and then it is tested and fine inspections are done.
Over a period, the design has been very complex as for most of the customers, the size of the PCBs is getting smaller because the customer’s final products are becoming smaller. For example, most of the drilling machines that we have are CNC machines, which are high speed and high-quality machines, and are capable of drilling extra small micro holes. The plating lines are highly automated with the PLC control movement so that you can control each plating cell depending upon the amount of current. We need a sophisticated CNC routing machine, a flying probe testers, bed of nails testers which are fairly complex, and a lot of CAD, CAM software's to process those customer designs.
Q. Can you also briefly tell us about how multi-layer PCB manufacturing is different from a single-layer PCB?
Multi-layer PCBs which are also called the sandwich PCB are basically layers of PCB on top of each other and in between there is insulation which allows them to make sure that no 2 layers connect with each other and create a short circuit. We must bond multiple layers and then we must press it.
Each layer is separately processed first, then they are bonded together, and then they're pressed together after which it becomes a standard double-side kind of situation, and then it starts from drilling, plating to solder mask and everything. The reason for multi-layer is primarily to ensure that the real estate of the PCB can be reduced as small as possible because you can then practically wrap the circuits in the PCB. Lot of customers design in such a way, that layer to layer connection is pretty complex with blind and buried vias. We support many customers with those complex designs
Q. Does your company provides services such as designing circuits or making amendments to the submitted designs?
As a PCB producer and a PCB assembly supplier, we do not really have the vertical or domain knowledge of each customers’ application or the product they are developing. Since we service many verticals like IoT, telecom, railways, defense, etc., we cannot be an expert in every domain, so we only support our customers where we can bring value to them. Once the customer has a schematic and Bill of Material ready, then it becomes fairly mechanical tasks i.e., converting the schematic to a Gerber file, which is an input for manufacturing PCBs. So, we can provide layout support or design support aspect. Another thing is design for manufacturability. When a customer gives us a Gerber file, we analyze that before starting manufacturing and then let them know if there is something wrong.
On top of that, we do PCB assembly. When we receive the bill of material in the Gerber file, we realize that sometimes the pegs are too big for a component which could create a problem later. Or there is another issue like polarity or many normal standard usual things which can be a problem for the customer in future after boards are assembled. We highlight those things using our automated tools and then work with customers very closely for rectifying those issues.
Q. PCB manufacturing requires specialized machinery. What factors do you consider before purchasing a machine and where do you source these machines from?
There are many factors that one must consider before choosing a machine, like whether that machine is what you are looking for. When it comes to meeting those expectations, such as can it produce what customer wants, can it be serviced locally, or what is your budget. How much you want to end on those machines and how long you plan to use them are some of the standard criteria that we use. Generally, we tend to use either European or American machines.
Q. Since you're procuring machines from European or American companies, so you also require specialized people to operate and service them. How do you go about training and development of the people who are working in your company?
About 10-15 years ago, it was very difficult to find a local manufacturer from India, who can give us a world-class quality, but the government of India is promoting and incentivizing a lot of schemes. We have started working with a few partners within India who are able to give us a good value for money, and similar technology without compromising on our process time. We can use some of the machines especially in a web process area, but most of the machines are still European. It is not easy for us to maintain and service those things. We work with our machine manufacturers and have a very long relationship with them. They definitely understand the need for us to take care of those things. Moreover, we have developed human capital for servicing and maintenance of these machines in house as much as we can to ensure that the machines are regularly serviced, and the breakdowns are very limited for better productivity and consistency for our customers.
Q. PCB powers started around 23 years ago and your company has seen the PCB market rise from the root. So, can you just tell us how has the market grown over the years?
Two or three decades ago, electronics were not considered as lucrative or possibility of manufacturing in India. When I was a kid, everything was imported like the cassette player, VCR, electronic TVs, and these articles were considered as a de facto standard in terms of quality, reliability, and technology. But that has definitely changed over a period of time and now India is one of the top three mobile phone manufacturing countries in the world. Things have definitely changed and so is PCB manufacturing. The number of players has increased over a period of time and so is the requirement of PCBs in India. I was president of ELCINA, Electronics Industries Association of India focusing mainly on component manufacturing and electronics. We did a lot of studies and made a lot of reports in line with the government partnerships. The total estimated PCB requirement in India is more than $1.5 billion annually and the majority of that equipment is still imported. But domestic manufacturing is also growing up, especially in the last five years. We hope that in the next five years, the gap between local manufacturing versus import will be minimized, which is right now growing because the demand is growing at a faster rate. The manufacturing capacity is not growing as much as the demand is.
Q. Nowadays, international companies are also providing fast and cost-effective components and PCB services competing directly against Indian manufacturing. How does your company plan to tackle the international competitors?
There are a lot of factors and firstly we have to accept that we are in a global landscape of the industry. We have to be globally competitive as a default thing. Being competitive can be very efficient but we need to add value too! It actually can be a combination of many factors. We at PCB power market, have chosen the path of value added services to the services for customers. We believe in having a relationship with the customers, providing the reliability will definitely give us an advantage. Next, the factor for customers in India is the local language, the communication, and ability to talk to somebody over the phone really matters. We have to be as competitive as possible, and I think that we have been fairly competitive. For e.g., a small exception that we generate to the customer before we start manufacturing can save hundreds and 1000s of dollars. When a customer is in need of something, we are there for supporting you! Sometimes we get requested like, “Hey! I placed an order for two weeks; I really need these things? Can you push it faster, and give us a faster delivery”, which we do as long as we can. We have lately started manufacturing PCB assembly for our customers which is a great service as we think this can bring value to the customer and all these things are definitely going to be useful for our customers. We have to live with the competition, whether it's in India or outside India, and it's part of the business but as long as you do your job properly and you invest your money rightly in manufacturing, in technology, and in human capital, one can be very confident that their customers will be happy with their services.
Q. PCB fabrication requires high-quality fabrication and very effective quality checks. So, what kind of procedures and tests do you perform on the PCBs before they are sent out to the customers?
I think there are easy ways to manufacture PCBs because if you look at them, a lot of information and videos are available on the internet. There are amateurs who could produce a PCB in their bedroom, and then there are companies that are as big as a three-bedroom apartment, and they produce PCBs professionally for their customers. Also, there are companies like us, who are having 100,000 square foot facility for manufacturing PCBs. The fundamentals of PCBs remain the same but the challenge is that how do you ensure that those PCBs produce are consistently of the same quality. We have to invest a lot of money in our quality, standards, training, and the quality of equipment to check those things. It's a very complex and continuous process. We are very proud, happy, and conscious about this quality as we invest a lot of money in our quality process.
Q. Please tell us about your company's production capacity and do you have any plans to increase it in the near future?
The production capacity cannot be really quantified. For example, if I have to drill a five-millimeter diameter hole, and it’s a simple board, then I can produce 100 boards per hour. But now, if I have a very fine and complex design, where the whole size is of point one millimeter then I cannot produce 100 boards in 60 minutes and can only produce 10 or 15 boards in an hour because it takes a longer time to process. Another thing is, if I must produce only one board for 24 hours, my output will be a lot higher, versus if I have to produce 100 different designs in 24 hours, in that case, my output will be a lot lower. We try to manage and measure our capacity in how many orders we can produce on average, and we make sure that our capacity does not get more than 70-80% utilization because we want our delivery performance to be maintained throughout the process. It's a relatively complex process, but it's a continuously improved process. We are having a larger capacity, I cannot really quantify in terms of square meters, which is standard for our PCB industry, because I think that is not the right thing to quantify the capacity utilization, but we are able to manage a good number of orders per day and we make sure that we are ready for the future expansion.
I think I can give you some idea about it with regards to our plans and investments. In the last five years, we have invested a little over $5 million in our production capacity, infrastructure, and technology. We also have a similar amount of investment plans for the next five years, with our investments focusing on capacity and technology. We invest in technology that has nothing to do with PCB manufacturing directly. We invest in our software, E-commerce capability, and we invest in human capital, we invest in infrastructure. We are the first Company from India who start manufacturing PCBs in the USA. Initially, we invested in a company and now we have it as our own 100% subsidiary.
Q. First setting up a manufacturing facility in India and then in the US, you have seen both the markets. How is the market different in the US as compared to the Indian market?
It's a completely different market as their expectations and requirements are different. Initially, the USA used to be a major manufacturing hub for PCBs but not anymore. Now they are exposed to China, India, Europe, and some local manufacturing in the USA. In the US, the customer has a lot of information, just like Indian customers have, but their approach to the vendor is different than the approach that we received from our customers here in India. Both are good, but their way of working is different than ours. India has also opened, and customer’s expectations are also increasing day by day. But the USA is a bit more mature market, and our manufacturing focus is primarily for what we call ITAR jobs, which are export control jobs for the defence and aerospace and there are critical applications in medical and other industries. We do manufacture in the USA and for another thing, we support our customers in the USA from our India’s facility.
Q. Since the inception of this pandemic, compared to the pre-COVID-Era, do you see any growth in the volume of orders from hobbyists or individual electronic makers?
My understanding and interpretation of the pre-COVID and post-COVID scenarios are slightly different because I look at them from a different angle. What has happened is that pre-COVID was not easy for a consumer to differentiate local manufacturing versus outside manufacturing. During COVID we realized that we were exposed as a country and we had to rely on many things outside India, right from a simple mask to an oxygen generator. It was an eye-opener for our country, and we understood sentiments from an Indian consumer or innovator or electronics manufacturer has changed to some certain extent, because the innovation cannot be stopped, and it did not stop even during COVID. There was a time that we could not get anything from outside India, for obvious reasons, and we all know that the supply chain was massively disrupted, and that's where we realized as a manufacturer the need for a strong local supply as soon as possible because it is easier for us to innovate. If we don’t have to rely on others and then to improve our supply chain ecosystem. From that angle, we see that uptick in innovation, and we can see that customers are becoming more innovative. On top of that, the government also realized that we are exposed to many things and for various geopolitical reasons. The other thing that is not really known to most of us is that India has to be self-reliant. Our prime minister, Mr. Modi has come up with the Atmanirbhar Bharat and now it has been inculcated to our customers significantly, and we see that kind of support happening again.
Over a period of the last four months or five months, because of this COVID analysis, we realized that components especially semiconductor are in short supply and a lot of designs, manufacturing, and production is stuck, especially for those semiconductor chips and we are unable to produce those things. That is something we have taken into account also, but in general, the scenario has improved.
Q. According to the reports, the semiconductor shortage will last even next year. How is it affecting PCB manufacturers?
Definitely, it affected us also, because when there is no semiconductor chip available, customers will not give us orders for the components and PCB also. We see that there is a whole period where a lot of customers were just waiting for their bill of material to arrive. But now it seems that the situation has eased out to some extent, and we see that customers are now planning for the design and are ordering more. That's one scenario that I would like to draw to you.
The second scenario is that a lot of customers realise "Hey! My design is 5 years old and I have been using this particular IC for so many years, let me find out if I am not bale to find this IC, can I redisgn my board or can I find an alternative component? How can I make sure that my production is not suffered." So alot of activities also have started taking place.
Q. Do you have any advice for any electronic grad or people who design a PCB when they want to design their own product?
I believe that they should be prepared for their ecosystem. It's kind of pity and unfortunate that there is a little bit limitation that we have to tell to those who are innovators to exercise extra caution before designing, that whether at the drawing board level or schematics level, please ensure that you have a certain level of comfort with regards to the availability of those components. Because if those components are not available here then you're again going back to your drawing board and then restart which is not a very good idea to do.
Second thing is that there are standard service providers like us who can help them so that they can focus on their own tasks, which is the most important in designing and developing products. They can outsource their PCBs, PCB assemblies, and components as much as possible so that they can focus on their core business, which is design and distribution. If you start working on those things from an early stage of your career, it will help achieve more innovations and design things for a period of time.