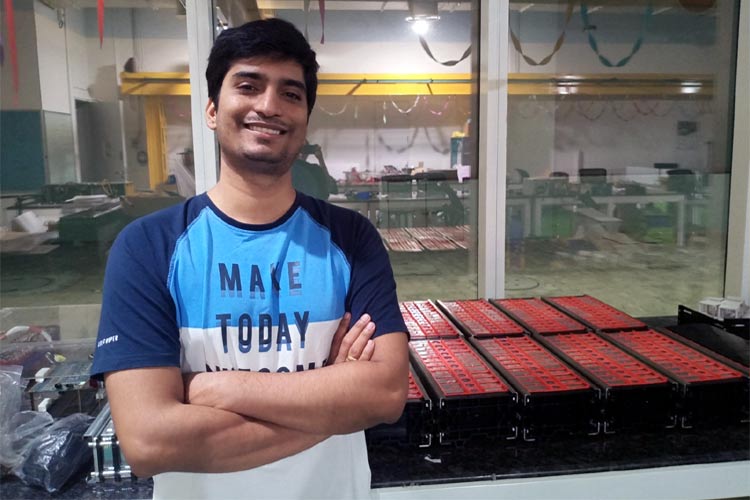
Transport is one of the major contributors to global warming, representing more than 23% of global energy-related carbon dioxide emissions. Today, Electric Vehicles are looked upon as an alternative green way of commutation but to make EVs more affordable and practical, we need much more efficient batteries and battery-charging technology.
Grinntech Technologies, a bootstrapped lithium battery technology company is making continual efforts to address the issue of carbon dioxide emissions and to bring about electric vehicle revolution in the country. With some of the major battery manufacturers licensing Grinntech’s technologies & solutions, the company is fast paving a way for electric vehicles and stationary energy storage to go the mainstream.
In the quest to know more about the company and to understand how their lithium batteries are bringing about changes, we asked Nikhilesh Mishra, CEO, and co-founder of the company some questions. Here is what he has to say.
Q. Today, Grinntech is India’s leading lithium battery technology provider, how did it all start?
It all started in the winter of 2008 when I was in my final year of B. Tech (Mechanical) at IIT Roorkee. At that time, I used to take lectures for juniors on the automotive topics under the SAE IIT Roorkee chapter. Midway through the series, I covered some lectures on EV drive train and EV batteries. It struck me then that my career span will see the transition from gasoline engines to EVs and the journey of learning about EVs and battery systems started.
After graduation, Puneet (a friend from college) and I decided to start a company in the EV domain. We started experimenting with different types of batteries and EV business models. We experimented with Zinc-Air Battery, Sodium-Nickel-Chloride Battery, Lithium-ion Battery, Battery swapping, EV conversion kit, etc.
Long story short, we finally settled with developing Lithium-ion batteries. We started with developing batteries for automotive applications as well as Stationary energy storage applications. We were ready with basic level technology and some prototypes by 2016, but the high cost of battery and EV was a big hurdle for its adoption. Keep in mind that there was no FAME subsidy at that time.
That was the time when we came into contact with CBEEV (Centre of Battery Engineering and Electric Vehicle) at IIT Madras. CBEEV is a collaboration of startups, Industry, and Academia aimed at finding solutions for problems of strategic importance. Our initial development was focused on swapping ecosystems since we had the dual goal of creating a product as well as a market. We used this opportunity to develop a wide range of products from small 2-wheeler batteries to larger Car, Bus and even Tractor batteries. We had the opportunity to work with Big OEMs like Mahindra, Tafe, and Tata Motors, etc.
Q. What type of technology is required to enable domestic mass production of Lithium Batteries? How is Grinntech helping to make this happen in India?
The Lithium-ion battery value chain can be broadly divided into three parts.
Raw Material: The value chain begins with the mining and refining of raw materials like Lithium, Nickel, Cobalt, Manganese, Graphite, Copper and Aluminum, etc. These materials are then processed to make the Anode, Cathode, Separator, and Electrolyte materials. This activity is about 35% of the value chain and is currently dominated by big Chinese companies, although there are some Korean and European companies as well.
Cell: The second stage is the conversion of these raw materials into Lithium-ion cells. This process involves some customization, mostly in the form of additives and electrolytes that define the behaviors of the cells. This activity adds another 30% in the value chain and is being done by companies like LG, Samsung, Panasonic, CATL and BYD, etc.
Cell to Pack: The third and most upstream activity is taking these cells and making a battery pack by adding BMS (Battery Management System), Mechanical Packaging and Cooling solutions, etc. This activity is adding the last 35% in the value chain and is being done by Grinntech and companies like us.
The technical capabilities needed to perform these tasks are in ascending order, more importantly from the time requirement point of view. For example, developing the technology to convert the cell to the battery could take 2 to 3 years while 5 to 10 years could be needed to develop technology for superior quality Lithium-ion cells. Making raw material is more of fundamental research and could take decades.
That’s why Grinntech has started from the cell to pack technology because that will take the lowest amount of time while we will still add 35% of the value chain. Grinntech has developed these technologies in the last 3 years and started commercializing them.
The technology needed to develop these batteries are related to Mechanical Design (Strength of battery), Thermal Design (Cooling of battery), and Embedded Design (BMS for the safety of battery). These technologies although complex have been successfully developed by Grinntech and now we have world-class batteries for safety-critical Automotive applications.
Q. Please share some technical aspects of your battery Packs and Battery Management Systems.
There are a lot of parameters that define battery superiority. We generally group them as Performance, Safety, and Features
Performance covers the usability aspect of battery like how much power you can draw (Pickup and speed), how much energy you can store (Range of vehicle), can you use it in extremely high and low temperature, many kilometers and years the battery will last before you have to change it, etc. Our batteries are class-leading in packing more energy and power in a small space. We have reached the magic figure of 300Wh/ltr for our 2-wheeler batteries. This number is around 30% higher than our competitors and results in a lot of range in a small volume for the user.
Safety covers the aspect of making the battery safe in every situation. The battery should be safe not only in intended application conditions but also in abuse conditions. Grinntech is leading the battery development with functional safety standards which are a gold standard in Automotive applications. Functional safety compliant batteries are safe in normal use but it’s also safe when it fails by failing in a controlled manner that safeguards the user.
Features cover the interaction of battery and user. Unlike traditional Lead-acid batteries, Lithium-ion batteries are a smart device that can do a lot of functions because of the onboard computer (BMS). Most of these features are to make the user have information and control over using the battery and vehicle. Grinntech batteries are loaded with a lot of features that are industry-leading and make it fun to use our battery. Our batteries are also having BLE (Bluetooth), 4G, and NBIoT. This makes the battery ready for swapping applications as well. NBIoT, in particular, is very important for swapping application and shared mobility as it makes possible to use the underground parking places because of NBIoT low frequency and thus better penetration.
Q. Establishing a supply chain in India for Lithium Battery Technology should have been challenging, how did Grinntech get over it?
We have faced challenges in multiple aspects of the supply chain. In order to produce a product that can compete on the world stage, what we ask of our vendors must also be cutting edge. There are processes and capabilities required which are currently unheard of in India. Grinntech is built on the belief that a “design and make in India philosophy” is what will put us on the world EV stage. Because of this, we have put tremendous resources and efforts into domestic vendor development and have simply not taken “not possible in India” for an answer. We still have some ways to go to compete with China in terms of costs and timelines, but over the years, we have been able to build an eco-system that we believe will soon be world-class.
Q. What type of technical difficulties or technological barriers that Grinntech faces when working with Lithium Batteries?
The most important one is developing the team. Being a new technology, there simply are not enough people with prior experience of developing Lithium-ion batteries. Our approach has been to hire people, train them on this technology and then they start contributing. This makes the process slow and costly. With persistence and a culture of knowledge sharing Grinntech has been able to develop a team of 50+ professionals from different domains, fully experienced in developing Lithium-ion batteries now.
Another important problem is that customers right now are also not fully aware of the technology and we have to put a lot of effort in finding what customer needs instead of what customer wants (as wants are many times influenced by the wrong perception of technology or marketing gimmick).
On the technology side, most of the problem comes from getting the supply chain right as I have previously discussed. Getting the right part with the right quality and timeline has been a nightmare, but now things are much more in control. Continuously changing technology and changing market dynamics is also not helping as well.
The silver lining is that all these challenges are being faced by everyone. Grinntech with its agile approach of product development has been better able to respond to challenges much faster and come up with a variety of products suitable for Indian needs.
Q. Grinntech has presented its lithium-ion batteries to our Prime Minister, Narendra Modi. How was the experience and response?
It was an honor to host our Prime Minister Narendra Modi at IIT Madras Research Park where he spent time looking at our products and technologies. Along with us, there were other companies that are working towards the making of other EV components like Motor and Controller, etc. The moment PM arrived and saw all the things, the first-line he said was “Mujhe to Battery Chahiye” i.e. “Most importantly I need batteries”. This solidifies our belief that battery is playing the most important role in EV adoption and localizing battery manufacturing in India is of most significant strategic importance.
Q. What is Grinntech currently working on and what are its future plans?
Grinntech has developed a vast array of products and technologies by now. We have developed batteries with all cell form factors i.e. Cylindrical, Prismatic, and Pouch for different applications like 2-Wheeler, 3-wheeler, Car, Bus and Tractor, etc. Now that we have covered the base technology, we are starting the volume production of batteries. For that, we are setting up our first assembly line which will manufacture in large volume batteries for 2-Wheelers and 3-Wheelers.
We will be putting efforts into two different aspects now.
Volume production of 2-Wheeler and 3-Wheeler Batteries, since, these are the only high-volume consumption applications right now. We have come up with our flagship line of products which will be unveiled soon. Check out the sneak peek image below.
Joint development of custom batteries with OEM’s for applications like Car, Bus and Tractors, etc. We believe these applications are going to be in volume production very soon and they will all need custom developed batteries. We call this custom development of batteries with OEM “Co-Creation”. We are already working with multiple OEMs on these Co-Creation products and they will be unveiled in due course of time.
Q. Where do you see the EV market in the next 5-10 years?
We believe the Indian EV market is going in the right direction. The FAME-2 subsidy has been helpful in increased EV adoption and I appreciate the government’s move - especially the approach of localization and quality improvement in order to qualify for the FAME-2 subsidy.
Although the initial adoption of EV has been slow in India, we believe that in due course of time, this will change and Indian EV adoption will be faster than the global pace. The reason is that Indian automotive applications such as the distances traveled, and traffic conditions are well suited for EV adoption. We do not believe that India is a cost-sensitive market but rather a value-sensitive market. We are very close to the point when the value derived out of EV ownership will surpass that of ICE vehicles. Complete adoption of EV is a herculean task that may take decades to complete. We believe the 2-Wheeler and 3-Wheeler will lead the adoption followed by Bus and then Car. In the next 5 years, we will see a significant portion of 2-Wheelers and 3-Wheelers shifting to EV while Buses and Cars will probably take 10+ years to significantly shift to EV.