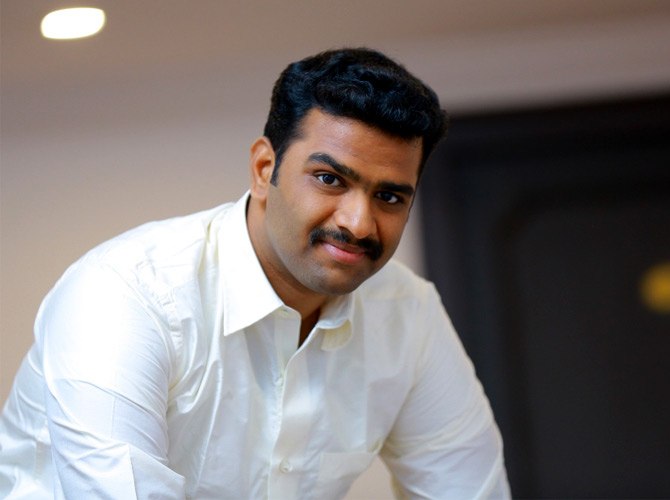
The rise of Internet of Things (IoT) has taken the evolution of sensors to a completely different level. Sensors are an integral part of any engineering company that works on the IoT platform. Various industries and organizations use different types of IoT sensors like temperature sensors, proximity sensors, water quality sensors, etc. as per their requirement. Founded in 2019, XYMA Analytics offers a complete Industrial IoT based analytics platform to provide smart process monitoring.
Using advanced ultrasonic waveguide sensors for the harshest environments was the main idea that persuaded the team of well-qualified engineers to start a company. Today, the company boasts of building smart sensors to enhance operational efficiency and offer more than just measurements. Curious to know more about the company, team, work style, problem solutions, and future plans, we asked Dr. Nishanth Raja a few questions. Read on to know what he has to say!
Dr. Nishanth Raja is the Chief Executive Officer of XYMA Analytics - an IIT Madras incubated company and a spin-out from Centre for Non-destructive evaluation. He was a Senior Research Fellow in Fluid Control Research Institute, Palakkad in Kerala and later joined as the project officer in Centre for Non-Destructive Evaluation (CNDE) - IIT Madras and received his Ph.D. from Anna University. He has also worked on several industry-related projects in the area of Ultrasonic Waveguide based temperature and flow measurements and has rich industrial experience.
Q. What inspired you to start XYMA Analytics? What problems does the company aim to solve?
XYMA Analytics is a result of the profound interest invoked from industries in the oil and gas, manufacturing and aerospace sector. During my research period at Centre for NDE, I was involved in the development of guided wave-based ultrasonic waveguide sensors for hazardous/hostile environments in process industries; the challenge was to solve their pain points. The measurement of the process parameters is vital in processing and manufacturing industries where our waveguide based sensing technology helped them in measuring at hostile and inaccessible regions in a distributed manner. We observed that there is a huge demand for sensing technologies in industries. That was the point when we decided to incorporate XYMA Analytics as a start-up which could provide sensing solutions to industries to enhance their process efficiency and improve their product life.
XYMA Analytics addresses issues with conventional process sensors with its novel ultrasonic waveguide-based sensor technology that helps the industries to continuously monitor their process parameters with Industrial IoT with a vision to democratize its sensor-based process efficiency for industries and also provide plant-wide distributed and concurrent sensing solutions for data-driven decision making. This is difficult using conventional sensing solutions.
This sensor is currently in field trials in several industrial applications including mould cooling jacket temperature monitoring during the steel manufacturing process as well as for furnace wall temperature measurements in the petrochemical process, glass manufacturing industries.
Q. Tell us about your “Ultrasonic Waveguide Sensors”, what is the technology behind it?
The ultrasonic waveguide sensor can be of different cross-sections such as wire, rod, strip selectable based on the access for the waveguide, different materials either metals or ceramics and is configurable for different measurements applications including adjustment of special distribution of the sensors.
The principle is that an ultrasonic wave is excited and travels along with the thickness of the waveguide. By tracing the interaction of the propagating ultrasonic waves with intentionally designed geometric discontinuities (bends, notches, and so on) and by tracking the shift in time-of-flight and frequency, attenuation, change in amplitude of the reflected ultrasonic signal from appropriately spaced reflectors (bends, notches, and so on) the localized information on the surrounding medium is extracted (for example, temperature).
In general, ultrasonic waveguide sensors measure changes in waveguide velocity due to the variations in its material properties (α, E, G, and ρ) arising from the changes in the surrounding medium such as temperature, humidity, etc. The change in time of flight, change in velocity, phase shift of the ultrasonic waves as compared at room temperature signals, help to measure the changes in temperature and other properties (rheology) in the surrounding media.
Q. How are Ultrasonic Waveguide sensors advantageous over conventional sensors?
Many industrial processes operate at very high temperatures. For example, refining crude oil and generating electricity require temperature levels that exceed several hundred degrees Celsius. Conventional sensors such as thermocouples, RTD and level sensors have accuracy issues due to sensor drift during their long-term operation.
Thermocouples, in particular, when used at elevated temperatures in hostile environments are prone to mechanical failure of the junction. Also, thermocouples can provide local temperature only in a single region of interest. Whereas the ultrasonic waveguide sensors are more robust since we use the same thermocouple wire material (e.g: Kanthal, Chromel, Stainless steel, etc.) is used as our waveguide and it doesn't have any junction to fail. Besides, this sensor has a smaller footprint and can be designed for different configurations such as helical, spiral, multiple bents, etc. The use of multiple sensors in the same waveguide for distributed sensing over a wide range of temperature (30°C -1400°C ) and multiple parameter measurement (e.g: Level, Temperature, and Rheology) of using a single waveguide sensor provide an advantage to our Ultrasonic Waveguide sensors when compared to conventional sensors.
The waveguides guide the ultrasonic wave from the sensor electronics to the measurement region of interest, while holding the sensor electronics (transducer) safely away from the hostile and remote inaccessible environments as shown below.
Also, the proposed waveguide sensor is very robust and can adapt to complex industrial environments for more versatile and redundant measurements of temperature, rheology and fluid level in critical enclosures. Distributed temperature measurement is difficult using conventional thermocouples due to their ability to measure a single point measurement withstand hostile environment size constraint. The Guided Wave based waveguide sensor provides a reliable, stable, and cost-effective solution for interface /accurate process measurements.
Q. Can a single sensor measure multiple parameters like temperature, viscosity, density, etc.? How is it made possible?
During my research, we founded the fundamental guided wave modes Longitudinal L (0,1), Torsional T (0,1), and Flexural (1,1) can simultaneously be transmitted/received using a single waveguide sensor where each wave mode travels at a different speed and sensitive to different displacement/properties.
For example, longitudinal wave mode (Sensitive to axial displacement) can be used for temperature measurement, Torsional wave mode (Sensitive to angular displacement) can be used for rheology measurement (Viscosity/Density/Temperature), and flexural wave mode (Sensitive to out of plane displacement) can be used for level measurement. By tracking the change in attenuation and phase shift and frequency shift of these wave modes (Longitudinal, Flexural and Torsional), we can monitor the surrounding medium properties. This patented technology is tested in an industrial environment to simultaneously measure temperature and viscosity of resins at high temperatures using a single waveguide sensor. These waveguides can be custom designed for a specific application in industry and can also be designed in different cross-sections.
Q. What type of sensors are offered by XYMA for Heavy Industries and Process Industries?
XYMA Analytics develops novel sensor technology-based platforms for Industrial IoT with a vision to democratize sensor-based process efficiency for industries and also provide plant-wide distributed and concurrent sensing solutions for data-driven decision making. Our patented technology products, PoRTS (Portable Rheology and Temperature Sensors) and uTMS (Multi-point Temperature Measuring System) focus on boosting the productivity of industries by increasing process efficiency and reducing opportunities for manual error and enhance product life.
Q. Are all the sensor solutions manufactured by XYMA Analytics itself? Tell us about your manufacturing and supply chain process
XYMA sensors are customized and designed in-house for a wide range of temperatures. We develop a waveguide sensor based on their temperature range and the environment where the sensing is required. Also, the selection of waveguide material, size, length, and the number of sensors designed mainly depends on the customer prerequisites and application environment.
We have a state of the art manufacturing facility and soon, we are planning to expand our current R&D/calibration facilities to meet all client testing requirements. We always maintain QHSE (Quality, Health, Safety, and Environment) values at the maximum during manufacturing, installation, and after-sales service with the help of completely dedicated young engineers. In each stage of our supply chain process, we have well defined KPI’s (Key Performance Indicators) to ensure the process which matches our core values. Since technology is evolved from the XYMA Team, we developed our master data for all entities to ensure the reliability of our products. We always ensure to meet all the client's quality requirements also. All our suppliers undergo a technical evaluation process to ensure the reliability and quality of the supplied items. For product improvement, we have a customer feedback system also.
Q. XYMA Analytics also provides IIoT Connectivity and Data Analytics. What wireless solutions and IoT platforms do you use?
XYMA-IoT (XIoT) products are currently low-power Long Range wide-area network technology (LoRaWan) besides MQTT as standard communication protocols with edge computing and visualization, to automate and optimize the process flow through edge deployed self-tuning algorithms. For the application of these protocols standard, IoT platforms like Arduino, raspberry pi, Semtech (LoRa) and AI thinkers are used along with mutual interfacing with two or more platforms (Arduino and Python interfacing) for data analysis and transfer has been implemented. Other optimization techniques such as HART protocol and Modbus are used for other industrial requirements. These end-to-end wireless communication solutions have been used to enhance the connectivity in the present condition or as an integrated part of proprietary solutions for various industrial applications.
Q. Who is currently being benefited by these Ultrasonic Waveguide Sensors and how? Can you give us an example/case study?
A wide range of industries including (a) Manufacturing industries involving metals, furnaces oven, etc. (b) Process industries such as refineries, chemical industries, fertilizer industries for improving the life of the high-temperature components as well as the efficiency and robustness of the industries. (c) For industries such as fast breeder reactor where imaging and measurements under the liquid metal is a challenge (d) Temperature-controlled storage industries. (e) Polymer industries for cure monitoring including aerospace, composite, etc.
There are certainly quite a few cases where our sensors helped process industry to optimize their efficiency and identify the curing of their product. For example, continuous temperature cure monitoring of composite used in aircraft industries remains a challenge. We have embedded our waveguide sensors during the manufacturing of the composites and monitored continuously until the curing is completed. Using the temperature and curing data provided by our sensor, the manufacturers can enhance the product life and process efficiency to 50- 70%.
Another example of this revolutionary technology that helped in preventing product failure of the leading manufacturing industry is by measuring the distributed temperature of its furnace during its process. Distributed temperature measurement is difficult using conventional thermocouples due to their ability to measure a single point measurement withstand hostile environment size constraint. Our waveguide sensor can do measurements by maintaining the sensor region in a hostile environment and operating it from a remote location and also waveguide sensors can make distributed temperature measurements in multiple locations. The geometry constraint (1.5 mm slot) to insert multiple thermocouples is also addressed by using a single waveguide (1mm) with multiple sensors.
Q. Apart from XYMA Analytics, who are the other players in the industry that provide solutions using Ultrasonic Waveguide sensors?
To our knowledge, XYMA is the only industry that provides guided wave-based waveguide sensing techniques for process measurements in the industries. There are well-established industries such as ABB, Honeywell, Omega, and Emerson that are involved in the process measurement business but IIoT enabled waveguide sensing with data analytics to make XYMA different from the existing players in the market in terms of technology and solutions provided. The key advantage of waveguide sensors are robust and have a smaller footprint, capable of multi-point and multi-parameter sensing over a wide temperature range.
Q. How do you see industries in India adapting IIoT? What are the hurdles?
In the past decades, the IoT has transformed itself from being the 'Internet of Things' to 'Intelligence of Things'. In industries, IoT is used to maximize efficiency to upgrade health and safety conditions, reduce downtime, and also provide a customized product. The major hurdle regarding IoT is the lesser awareness among industries in India about its usage and intelligence that can help in improving operational efficiencies for industries at large by helping them enhance monitoring and increase safety and accuracy.
The main challenge in Indian industries is data storage and ownership issues, conflict in standards followed by each industry, data security issues, lack of skilled people in the plant and restriction to the internet inside the plant, access and integration of IoT to their dashboard, etc.
Taking innovation from laboratory to industry is not an easy job for any startup. The product should be robust, certified and reliable with high accuracy. These are some of the major challenges in the Indian industry.
Q. Tell us about your team and workplace
XYMA has a strong talented team of young engineers with both industrial and research experience from eminent institutions like IITs, NITs, CSIR labs, and MNCs, etc. This group of young scientists helps XYMA develop its indigenous products which are competitive and robust enough to compete with large industry players.
Moreover, my co-founders Prof. Krishnan Balasubramanian and Prof. Prabhu Rajagopal are pioneers in the field of Ultrasonics and NDE. They have guided, motivated, and mentored me in making XYMA a reality and using XIoT for addressing industrial problems. Prof. Krishnan Balasubramanian is currently the Head of the Centre for Non-Destructive Evaluation (CNDE) and a Chair Professor with the Department of Mechanical Engineering, Indian Institute of Technology Madras. He has been involved in the field of non-destructive evaluation for more than 30 years with applications in the fields of maintenance, quality assurance, manufacturing, and design. He has more than 300 technical publications. His areas of interest include non-destructive evaluation, intelligent manufacturing, and in-process monitoring, structural health monitoring, and applied data analysis. Prof. Prabhu Rajagopal has been involved in the field of non-destructive evaluation for close to 20 years. He has expertise in high-temperature transducers and feature-guided ultrasonics. His areas of interest include feature-guided waves (FGWs), meta-material lenses, the waveguide-based sensor for condition/cure monitoring and NDE using robotics.
IIT madras incubation cell ecosystem supported us in such a way that we could start right out of the lab. We use best-in-class facilities to build and test your products. IIT-M helped XYMA to take the product to the industry, which takes you a mile ahead.
Q. What are the future plans for XYMA Analytics and how do you see the market?
India is a small portion of the global market where we have currently deployed our products. Our expansion will also involve collaborating with research centers and universities across the globe to boost R&D on our future AI-based XIoT sensors for process optimization. This helps to perform intelligent asset monitoring to perform risk evaluation and estimated life prediction for improving safety and efficiency is at the core industries. XYMA is focused to deploy our high end patented solutions to global Oil and Gas Markets, manufacturing industries and take indigenous core technology built in India to the rest of the world.