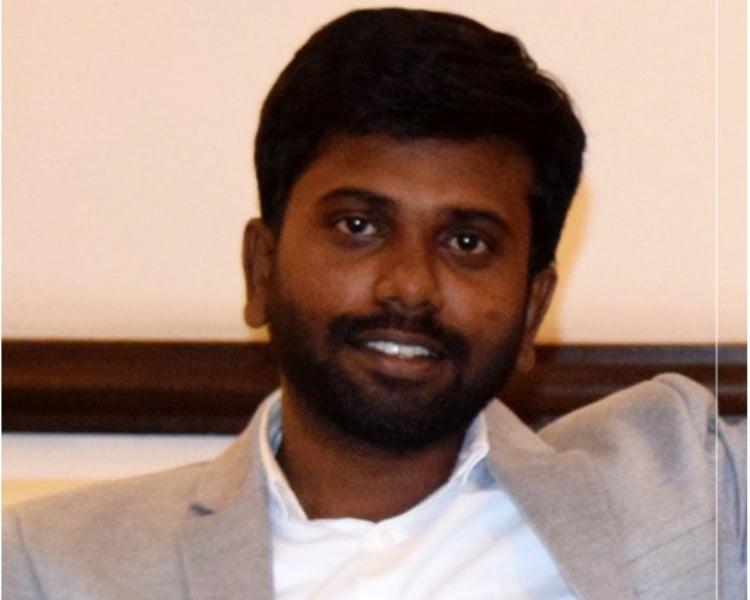
Incubated at IIT-Madras Incubation Cell, Planys Technologies is India’s first OEM of compact ROV firm that has gained immense popularity since its inception. The ROVs developed by the company are underwater drones used as inspection and survey solutions. Besides, being an industry leader that provides smart underwater inspection solutions, the startup has been in news for the great contribution it made in the search operation for missing miners in Meghalaya.
We sat down with Mr. Dinesh Natarajan to know about the company, the team, and the vision of the company, the challenges, and a lot more. He is a Power Electronics graduate from SSN Engineering College, Chennai, and is the R&D head at Planys Technologies. He has served as a senior project officer at IIT Madras and possesses experience in developing power converters for novel renewable applications and commercial units targeted towards energy generation and conservation.
Q. Planys Technologies is India’s first Original Equipment Manufacturer (OEM) of compact underwater robots (Remotely Operated Vehicles or ROVs) for performing the underwater inspection. What motivated you to start, what problems does Planys aim to solve?
Planys Technologies is India’s first Original Equipment Manufacturer (OEM) and an industry leader in offering smart underwater inspection solutions. The need for a better inspection solution and our passion for marine robotics led to the inception of Planys Technologies. Aging infrastructure is a pressing issue across the globe. Subsea structural assets such as dams, bridges, ships, oil & gas platforms, etc. need to be inspected at regular time intervals to sidestep catastrophic failures. With its disruptive innovation in the field of marine robotics, NDT methods, and post-inspection data, Planys helps asset owners make data-driven decisions for maintenance and repair.
Q. Planys technologies has come a long way and has done a tremendous job in the field of submersible robotic inspection. How has the journey been till now?
The concept that we introduced in the market was completely new and it was a challenge to win the client’s trust. Our team had a tough time convincing the customer regarding the capability, robustness, and accuracy of our service. We just completed 5 years in business this June. The journey has been incredibly rewarding and a learning experience in equal measures. Over the tenure of just half a decade, Planys has completed 125+ projects across 8 sectors and 3 countries. With a fleet of 6+ ROVs, a young team of 80+ members, an entirely owned subsidiary in the Netherlands and scale up operations in the Middle East, Europe & South-East Asia, Planys is all set to make an impactful global footprint in the underwater inspection industry.
Q. Please shed some light on remotely operated vehicles (ROVs) manufactured by the company. Also, share some technical details as to how it works. Please explain briefly Mike, Beluga along with the differences and applications.
Underwater ROVs can be analogous to quadcopter (drones). When compared to drones, ROVs are meant to be bulkier, they can weigh anywhere between 10 kilos to a ton. They are classified as heavy work-class, observation class, and mini ROVs based on the size, depth rating, and capabilities to perform tasks.
The ROV system comprises a power conversion unit that manages to deliver the quality power required for the ROV and the control station. The control station is nothing but a customized computer hosted in a ruggedized carry case to withstand the outdoor tough environment. This serves as the control unit for the pilot to have a live visual for the ROV and pilot.
The ROV is packed with individual modules such as power conversion units, computation blocks, cameras, data acquisition units to take care of the collection of data and processing it. A special-purpose neutrally buoyant cable serves two purposes. One, as a high-speed communication link between the ROV and control station, and two, it carries the power to the ROV from the Sending end power conversion units.
Planys started its journey by designing a portable class ROV “Mike” which can perform a visual inspection. Mike being a portable-class ROV, the volume allocated to the electronics was small, the team had a tough time to engineer the electronics related to power, communication, and computations into compact form factors without trading off the performance. An elemental level of analysis of every module was mandatory to achieve a compact yet performing design.
We did not stop our experimentation there! Many types of communication protocols, power architectures on Mike, and we can claim that the team acquired humongous exposure to underwater robotics during the developmental phase of Mike. After all the hard work, we ventured into still waters up to a depth of 100 meters and achieved a tether length of about 300 meters.
The next ROV to be manufactured was Beluga, it was an entirely different ball game. We raised the bar and wanted beluga to be a tough and powerful machine that can be put to work in open water and near offshore conditions to battle ocean currents. The weight, size, and power requirement went up by three folds; it weighs around 50kgs and a payload capacity of 15kg, and guzzles power like a 4-ton air conditioning unit.
At Planys, a thought prevails that ROVs are not limited to specific tasks that are presently being carried out, rather it has vast potential and can perform contrasting tasks, hence we make sure that all ROVs are customizable and can accommodate diversified payload clusters.
Q. How was the experience of sending the marine robot, Mike underwater and carrying out 700 hours of operation?
It was a great experience as a pioneer in this field. We are the first company to work on marine robotics in India. At that time, the market was completely unaware of ROV systems and it was extremely difficult to showcase our capabilities. Mike served tendentiously for over 700 hours of operation. Its functional ability validated that our hardware, software, and mechanical systems were designed to handle rough sea conditions with world-class quality. Mike is one of the masterpieces that we build from scratch and its reliability has been proved time and again. We have imposed various operational challenges to mike, and it handled quite well in the field. It gives us a feeling of accomplishment when we look at Mike after each operation.
Q. What Technical difficulties do you normally face when manufacturing and deploying Underwater ROV? How do you deal with it?
Since marine robotics is very new to the Indian market and there was no existence of an ecosystem to search for major systems like propulsion, sensors networks, and mechanical system. We started building an ecosystem with all our vendors, figured out precise machining processes, ways to achieve tight tolerances demanded by the system. India has a tremendous manufacturing facility but one of the difficulties is to make the technicians understand the system to get the best out of it. We have had multiple visits to our vendors’ locations and vice versa; we work together to achieve a world-class product.
The vendor interaction offers them an insight into our technology and our specific requirements and the quality we are aiming for. Some of them went out of their way and suggested efficient manufacturing methods and processes which evolved our manufacturing capability.
Q. How is Sonar and Ultrasonic inspection used in Beluga? What are its applications?
Sonar is an acronym for the ‘Sound Navigation and Ranging’ technique, which is used as a tool for underwater communications, navigation, and detections of objects and it can be either active or passive type. Sonar has widespread applications, it can be used to conduct surveys and seabed mapping, and often required to understand the underwater topography, presence of any obstacles before the commencement of any maritime infrastructural project or for study purposes. A practical application of this survey is to quantify catchment areas of dams, which is essential information both for estimating hydropower generation and for dam safety aspects.
On the other hand, ultrasonic inspections are related to evaluating the integrity of submerged objects or structures that are subject to a high degree of corrosion. High-frequency waves are transmitted towards the object and received. Frequency domain analysis is performed over the received signal. The results can be then interpreted by experienced professionals to quantify abnormalities. It may be corrosion, physical damage, structural defects in any of the parts, etc.
Q. Last year, the company launched the new version of its remotely operated vehicle (ROV) Mikros. Tell us something about that, how does it differ from Mike and Beluga?
As mentioned earlier, every ROV is designed to operate and function in different environments and for varied operations. One such requirement gave us an idea to develop Mikros. It is a purposefully mutated successor of the ROV’s serving the fleet of Planys, emerged to be the most powerful version, which can take long haul jobs over a single stretch. An indigenously developed power conversion architecture has pushed the capabilities beyond limits. Mikros’ unique ability allows it to enter confined areas that are completely inaccessible by any of Planys’ other ROVs or other solutions available in the market.
The form factor of Mikros is very different from Beluga, on the other hand, much powerful than Mike; this feature enables it to enter and maneuver in long narrow trenches and confined spaces. Talking about the form factor of Beluga, it’s a cuboid construction that is meant to be used in open waters and near-shore applications.
Mike is our super performer, it is the first ROV Planys has designed and still functional and one of its kind, taking advantage of its very compact dimensions, this was found to be the right tool to work with the Indian navy during the Meghalaya mine rescue mission in 2018 where it was used to scan for ratholes inside flooded coal mine shafts.
Q. As an Indian OEM working with Robotics, do you face difficulties in sourcing components? How does the supply chain of Planys Technologies work?
The discussion on the supply chain is not limited to the robotic companies alone, it applies to all the hardware-based companies that are trying to create and build things locally. There are various parts and components not available within the country and hence there exists an inclination towards importing those components. Planys’ has been on top of indigenization efforts right from the very beginning. I would say this will be the right time to put efforts to produce it locally, as the long-term success of any organization is to create an environment that should eventually evolve to become sustainable.
Q. According to the Markets and Markets report, the global smart robotics market is expected to reach $14.29 Bn by 2023. Where do you see your Planys Technologies and what other products and services can we expect to see?
There is a considerable increase in safety standards and practices in Indian industries and it is bound to increase in the forthcoming years. Safety forms a pivotal part in the industry 4.0 revolution. This encourages the invention of mechanized solutions that can outperform conventional methods without compromising on the safety standards.
Planys, pioneering the field of underwater robotics will be eyeing on opportunities to develop ROVs that have the capabilities to perform complex tasks at greater depths. We are working with defense through the iDEX program initiated by the ministry of defense (MoD) and Atal Innovation Mission (AIM) to develop indigenous products, customized for defense applications.
Furthermore, we are working towards the indigenization of certain submodules to overcome the challenges associated with long lead-time and achieve increased electronics packing density. This will help Planys in creating much smaller and portable versions of ROVs and also pave a path to create a sustainable ecosystem.