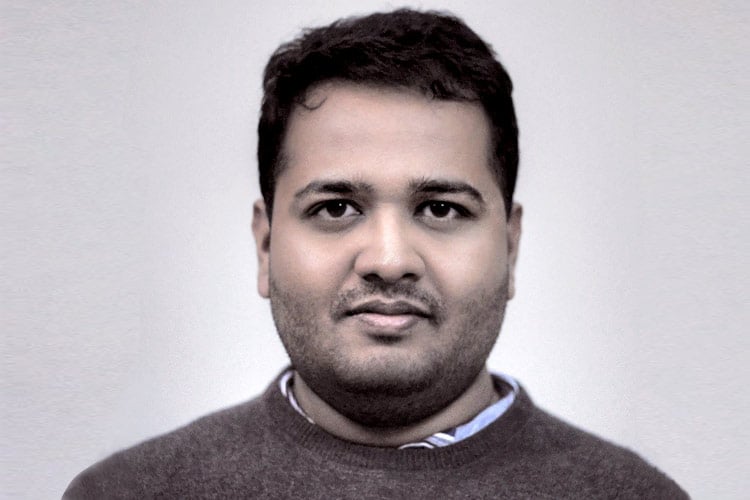
The robotics sector is revolutionizing various industrial sectors at a very high speed, but experts claim that the pace of transformation is not sufficient as expected. The sluggish growth in the robotics sector can be prone to several barriers such as software and hardware capabilities. In fact, there is not much transformation in the manufacturing processes of these products. When we speak of hardware, a chunk of commercial and industrial robots are still crafted from actuators, gears, and motors. Although these assists in the movement of robots and other functions, it also makes them unbalanced and inflexible. In this scenario, we spoke to Arvind Nagaraj, Chief Architect, Mitra - Invento Robotics about how to overcome the challenges of the robotics sector, how to make these products more flexible and less prone to damage, and most importantly, the latest technologies deployed in manufacturing these products.
Q. How are robots in India different from the rest of the world, advanced in robotics? In terms of technology and efficiency, what are your predictions for the coming years?
When someone thinks of commercially available robots, they are usually referring to robotic arms used for precision tasks in manufacturing like spot welding, palleting, and placement. These robots have existed for a while now and they are programmed to carry out hard-coded repetitive motion tasks. Similarly, there were mobile robots that could carry items from one point to another along a pre-programmed route in a controlled environment.
Only in the past decade, we have seen the rise of deep learning technologies that have allowed machines to handle some of the uncertainty and irregularities present in real-world environments that cannot be solved purely by traditional software programming. This gave rise to a plethora of new devices like smart speakers, convnet powered cameras, etc.
With the rise of AI, we have been able to equip our robot’s hardware with more sophisticated algorithms. Our robots make use of cutting-edge AI technologies to recognize/generate speech, detect objects, navigate in obstacle-filled environments by themselves.
We expect AI technology to continue to evolve, but at present, a machine’s intelligence is nowhere close to a human. Human-level intelligence is the holy grail for AI research and we will have to augment robot’s capabilities with human intelligence until then. We expect humans to make complex decisions for machines when they get stuck.
Dr. Rodney Brooks, one of the pioneers in robotics and AI technologies made a series of predictions three years ago where he called out when specific aspects of robotics will reach a certain level of maturity. He predicts that the conversational capabilities of robots and other AI systems will mature much sooner than generally available dexterous hands and complex indoor navigation systems. We agree with this take and have bet heavily on conversational robots - we expect this technology to rapidly improve and allow our robots to have more natural sounding and smarter conversations.
Mitra Robots: Source- Invento Robotics
Q. Currently, what are the various challenges of making or unleashing bots in India? What are the various steps required to ease the impediment?
Manufacturing hardware in India is a huge challenge. It is very expensive to import components, the infrastructure support and education are very low as compared to manufacturing powerhouses like Germany and China. These major factors make it very difficult to start a manufacturing project regardless of how well established the brand is (whether it’s Tesla or any small player - the complications remain the same). We are taking on these challenges one by one and have been successful in overcoming them to a great extent. We have managed to hire the right talent, source locally, and innovate by 3D printing our own components to bring down the costs to a great extent.
Customer education is another challenge. People have high expectations (all thanks to the movies) and it's highly challenging to present realistic use cases. We have done more than 400 events and have managed to be able to present bots as a friendly robotic avatar through crowd engagement activities. Bringing down the customer expectation is one of the most crucial steps towards enabling mass adoption of robots in India.
The popularity of robots is rising massively in India. People generally welcome the presence of a robotics avatar in day-to-day places like Malls and hospitals. We have managed to deploy our robots with 40+ corporate clients in India alone and receive 100+ inquiries every week from event managers, businesses, and curious individuals from all walks of life enquiring about robots. Our safe estimate is that robotic avatars will become a common sight in malls, airports, and the hospitality sector in the next five years.
Q. What is the current business model of Mitra Robots and how much has it changed over the years? Also, kindly elucidate your mission and vision in the coming years?
Mitra is our flagship robot with a humanoid form factor and has been primarily deployed as a friendly, conversational companion in a variety of settings. Mitra has multimodal conversation capabilities through voice and gestures that make it friendly. Mitra also can autonomously navigate in complex indoor environments and use its computer vision algorithms to make sense of its surroundings. It has helped in a wide gamut of use cases such as retailers trying to understand the pulse of their customers through live data collection; to companionship for the elderly in senior care homes. When the pandemic hit, most in-person events for Mitra were brought to an abrupt halt, and we pivoted to the use case of visitor screening at hospitals and clinics. Mitra was fitted with thermal sensing capabilities to collect body temperature and issue visitor passes. We were able to quickly deploy the robots across India and other countries because we were able to build on top of Mitra’s conversational visitor management platform.
In the future, we see our robots work with humans as partners and help them be more productive and resourceful by taking up the repetitive and risky parts of their work. We see human and machine intelligence working together to accomplish tasks that either of them individually would find very hard. In order to get to that point, we have been primarily investing in a fleet management system for our robots that can allow humans to monitor, teleoperated, and guide them.
Mitra Robots: Source- Invento Robotics
Q. What kind of products, solutions, and services you are currently offering to your customers? Kindly share an in-depth picture.
We offer robotic solutions for collecting real-world data from live conversations. This is done through a 3-part strategy we call Greet-Guide-Engage. Imagine walking into a hardware store of a major retailer. A friendly robot meets and greets you at the entrance. The robot can recognize your face if you had visited previously and use its knowledge of your past visit to completely personalize your experience.
You convey your home improvement project idea by answering a few quick questions. If the project is simple, the robot would be able to directly offer you suggestions using its intelligence — such as guiding you to the drilling machine in aisle 5, nails in aisle 8, and photo frames in aisle 10. If the project is more complicated, it connects you to a human expert (working offshore) who guides you appropriately and adds the items you desire to the robot’s list. The robot then walks you through the store and helps you with the pricing.
At each point, you can show the robot the product and it can give you details, including videos of usage, pricing, and related products over its tablet. At the end of the purchase process, it checks you out, takes your feedback, and sends the live ‘Voice of the customer’ data to the analytics backend system to slice and dice the data, allowing the executives to glean insights. We are talking about creating customer delight based on data, expert connect, and human-robot interaction — that works not just in a hardware store, but also in malls, pharmacies, hotels, hospitals, and more.
Q. What are your biggest differentiating aspect that helps you stay ahead of the competition curve?
At Invento we make our robots end-to-end. We design and manufacture the hardware - we write the software in-house and we manage our robotic fleets. Having end-to-end ownership of the technology and processes allows us a level of control that would not be possible if we only did a subset. Our company also improved its own local supply chain for manufacturing as the pandemic brought sudden changes to our industry.
In terms of social events, we have the experience of working with scores of brands across industries through which we were able to acquire valuable insights on human-robot interactions. Our treasure trove of information and insights guided our software development teams to create unique plug-n-play features and integrations that make us quite unique. We also see a huge benefit in operating our fleet management teams in Bengaluru - we can offer human-robot operator services at a fraction of the cost compared to western countries.
Q. Your roadmap for the coming years?
We will continue to deploy robots in business environments for the foreseeable future. The amount of data collection and rate of data processing in the physical world(retail) is a tiny fraction of what is happening in the online e-commerce industry. We wish to fill that gap as much as possible through our robots. Our robots help supercharge your retail shopping experience.
We will also continue to help empower remote caregivers in senior care homes - these are unique challenges in an aging world where India as a country blessed with a large, young population can take charge and lead.
As the technologies in AI, wireless connectivity, hardware, and computation improve, we see robots not just in business settings but also in people’s homes enriching lives.