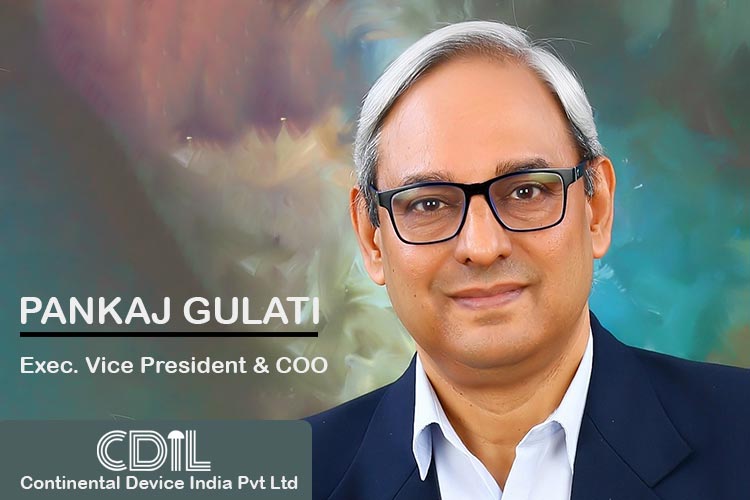
Around ten years back, there was a huge challenge in India in the ESDM and semiconductor manufacturing ecosystem mostly due to lack of proper policies by the government, concentration in the software ecosystem, and most importantly, there is no proper education about the importance of the ecosystem. Now, the government has undertaken various initiatives and unleashed schemes such as Production Linked Incentive (PLI), Scheme for Promotion of Manufacturing of Electronic Components and Semiconductors (SPECS), FDIs etc to boost the industry. But amid all these initiatives, the country is still grappling with numerous impediments to compete with other countries. In this regard, we spoke to Pankaj Gulati, Exec. Vice President & C.O.O. at CONTINENTAL DEVICE INDIA PVT Ltd (CDIL) about the current challenges in India’s semiconductor and EMS industry, and what are the various solutions that need to be taken care of to boost the industry.
Q1. India’s semiconductor revolution started way back during the 1970s, but after the late 80s the country’s dream of leading the industry shattered. What do you think were the actual challenges and the solutions required that time?
It was in the 1960s, we went through a semiconductor revolution with only two companies in India, Bharat Electronics Limited (BEL) [a government owned unit] which was manufacturing Germanium semiconductors and then in 1964, CDIL, the first private company started manufacturing silicon semiconductors in India. During the 70s, some more private companies started semiconductor manufacturing. In late 70s SCL started, this was also supported by the government.There is a very simple reason why other private companies who started semiconductor manufacturing didn’t do well later. In the 1960s to 70s, 8-10 companies were manufacturing semiconductors and they were doing well.
Then the focus of the policymakers moved towards electronics software. Indians are good in mathematics, logic, and we are good in software skills and English is our basic advantage. Most importantly, the labor costs were low and so design work started during the late 70s in India and that grew multifold. The chips are being designed in India for the US and European companies and fabricated somewhere else in the world. This chip design business needed much less infrastructure and logistics support unlike a semiconductor manufacturing set-up.
Indian companies manufacturing semiconductors, like CDIL had to do in-house R&D and were recruiting people from IITs to take it forward. We were growing, but it was becoming difficult to reach that cutting edge level of semiconductor chain.
In the late 1990s, the government of India signed a WTO agreement. While signing this, the policymakers did not realise the status of this industry and the support it needed. The industry was in the nascent stage and it is a highly capital intensive industry. When the WTO ITA 1 agreement came into force, semiconductors became one of the first products to come under zero import duty regime. By that time, China had already reached a very matured manufacturing stage. Almost every semiconductor manufacturing company in India had severe problems due to this “zero duty import” and many shut shop.
Q2. While speaking of the electronics industry it is growing immensely, but the component ecosystem is yet to be matured. So, what are your views in this regard?
The EMS industry started in the early 80s and almost all components were being imported from neighboring the countries. This continued for many years, without the government or the EMS companies realizing the importance of a domestic supply chain. It is only in the past couple of years that the supply chain value has been realized and keeping this in view the government introduced a couple of schemes to promote domestic component manufacturing.
Since then the process followed by the government has been logical and methodical. The first step is to increase and boost the EMS industry by imposing marginal import duty on populated PCBs. This encouraged the EMS industry to start full assembly in India. Now with the EMS industry at an advanced stage, the need is now being felt to have the component industry ecosystem in the supply chain. It is critical for the EMS industry to support the domestic components industry to reduce their inventory carrying cost and other logistics costs (shorter delivery time and technical support). The supply chain close to the manufacturers is always very helpful. However it will take time for the component ecosystem to develop and also initially the component may not be as competitive as the neighboring countries. This is something that the EMS industry needs to understand and thereby support the component manufacturers for a couple of years so that a strong component base is built within the country.
Q3. So, do you think the government is doing enough to boost the semiconductor and ESDM ecosystem? What are your messages to the government?
In the past few years the government has announced multiple schemes to promote the semiconductor manufacturing segment. Starting with the SPECS and thereafter the ISM allocation of US$ 10 bn (Rs. 76,000 crores) for a robust semiconductor manufacturing in India. Initially the focus of the policymakers was mainly on the wafer fab which involved billions of dollars of investment and high technology support. In the past few years it has now been understood that to boost semiconductor manufacturing it is important to have both front end (wafer fab) and backend (OSAT & ATMP) capabilities. The backend capabilities required much lesser investment when compared to front end and therefore it will initially be easy for companies to take a decision to move some backend manufacturing into India . The SPECS supports 50% of the Initial capital investment. Over and above this the state governments are offering additional incentives of upto to 25% (if the plant is set-up in that state). This is an excellent support for any manufacturing unit and this has encouraged the companies like Micron Technology to initiate a manufacturing set-up in India. However the SPECS is only an initial support for this capital intensive industry. It provides support for the capital investment, set-up of the plant. However there are additional disabilities that semiconductor manufacturing faces and these disabilities are on a running basis. To partly compensate for this, the PLI scheme by the government is a very good initiative. However the current PLI scheme is almost an extension of the EMS industry (mainly mobile) manufacturing PLI scheme. This needs to be corrected.
The investment to turnover ratio for a semiconductor manufacturing unit is very different when compared to the EMS industry. This could be 1:1 or 1:0.8 for the semiconductor industry. For the EMS industry manufactured goods this could be as high as 1:4 or 1:6. Keeping this low turnover for a high investment the government needs to consider a fresh PLI scheme for the semiconductor and component industry. I believe that if this industry is supported for 2~3 years by a good PLI scheme, the industry will be able to stand on its feet.
Q4. The government has recently notified that import of laptops and various IT electronic products will be required for a special license. What are your views in this regard? Do you think the decision is justified?
The government is doing this to encourage EMS manufacturing in India. Instead of importing a finished laptop, the assembly process would start. This is similar to the other finished products discussed earlier. There is a focus to increase EMS manufacturing and thereby encourage the rest of the component ecosystem to be initiated. However I believe it is little too early to impose such a strong measure. It should be done in a phased manner so that it does not hurt industry and the consumer base. A PMP can be worked out and international laptop manufacturers should be encouraged to move their component vendor base to India.
Q5. When was CDIL founded and what is its current mission and vision? What are your strategies that help you stay ahead of the competition curve?
CDIL was founded in 1964 under the leadership of Dr. Gurpreet Singh. He was a visionary - manufacturing semiconductors in India in 1964 was like a dream. CDIL was in a 10 year joint venture with an American company CDC. Since 1974 CDIL is a completely Indian owned company. CDIL is one of the first companies to introduce wafer fabrication in India. This wafer fabrication plant was run for over 35 years and in 2008 this was tapered down. The main reason for this wafer fabrication shutdown was because of the lack of necessary ecosystem and heavy capital investment to move the capability from 4" wafer to 6" wafer. This was in the year 2008 when there was no focus by the policymakers to encourage semiconductor manufacturing. CDIL continued with its ATMP lines and added new packages and products in the manufacturing range. As said earlier CDIL has been exporting semiconductor components since the early 70s. We exported almost 50% of our production during the late 90s. This strategy of exporting components kept CDIL in line with the international quality standards and also manufacturing at competitive prices. This very much helped CDIL tide over the ITA1 crisis. Thereafter CDIL continued to expand and grow. In the last couple of years CDIL’s focus has been to support the domestic industries with high quality products, suitable for Defense and Space (ISRO, HAL, etc.), Automotive segment (AEC-Q101) & ATMP for international semiconductor companies. CDIL has a full fledged backend assembly line, from Wafer Dicing to complete finished products both for leaded and surface mount packages.Our Mohali unit has the capacity to manufacture 25 million units per month of semiconductor components in leaded and surface mount packages. This unit also has a full AECQ and a reliability lab. Currently CDIL is working on new products and & will very soon introduce Silicon Carbide, MOSFETs and Schottky Diodes in India - meeting the demand in the EV, Solar & Inverter industry.
Q6. Currently, what are the various products and solutions you were offering and your roadmap for the coming years?
CDIL product range is very wide, covering a full range of discrete semiconductor components. These are offered in leaded and surface mount packages. Currently the trend is moving towards surface mount and keeping this in view CDIL new plant, under the SPECS scheme is for SMT components. More surface mount packages will be introduced in the next 18 months. The product range covers a full range of Transistors, Diodes, Schottky Diodes, SCR/ TRIACS, MOSFET etc. The latest introduction in the CDIL range is SiC (Silicon Carbide) product range of MOSFET and Schottky Diode. CDIL will be the first company to manufacture the Silicon Carbide products in India.
CDIL SMT line set-up under SPECS covers SMA & SMB packages. I am proud to share the that this package has been designed inhouse by CDIL team of engineers to meet specific requirement of supporting 3000V capability in a package as small as 3mm*4mm size. In the next 18 months CDIL plans to introduce additional surface mount components like DPAK (TO252) mainly for Power Electronics, MOSFETs and SiC products, to meet the increasing demand in the EV and Industrial Electronics segment. CDIL will continue to add new products and packages in the coming years.