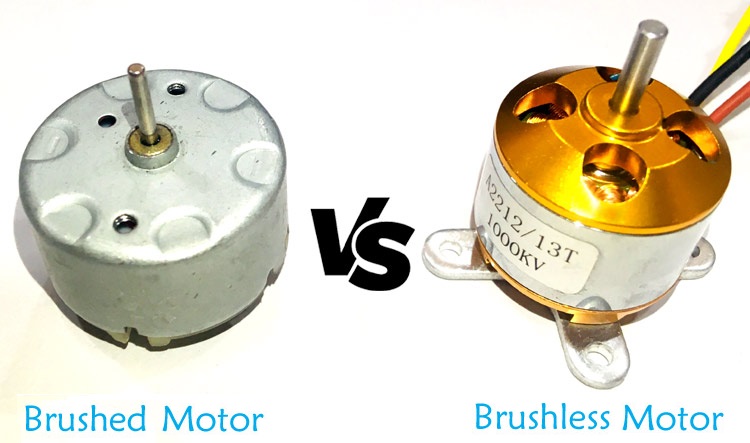
Electric motors have become a huge part of our lives. They are found in all sort of devices from electric cars to drones, robots and other Electronics Devices. In general terms, an electric Motor is a device which converts electrical energy to mechanical energy. They are usually referred to as the exact opposite of generators as they operate on similar principles and can theoretically be converted to generators. They are essentially use in situations where rotational motion is needed and they find applications in appliances (vibration motors), robots, medical equipments, toys, and much more.
Electric motors can be categorized into two broad categories based on the kind of power source used for them: AC Motors and DC Motors. As the name implies, AC motors are generically powered using AC power sources(single phase or three phase) and are mostly used in Industrial and heavy duty applications where a lot of torque is required. DC motors (which are our focus for today) on the other hand are usually smaller and are used in battery (or plugged in DC sources) based applications where significantly less amount of work is required compared to AC motors. They find applications in several devices ranging from everyday devices like shaving clippers to toys for kids, robots, and drones among others.
The requirement for DC motors differs from one application to the other, as one application may require more torque and reduce speed while another may require more speed and reduced torque, thus DC motors are sometimes classified by sales folks based on this. However, DC motors can be classified into three different categories or types including;
- Brushed DC Motor
- Brushless DC Motors
- Servo Motors.
For today’s Article, Our focus will be on the Brushless and Brushed DC motors, as we examine the difference between them along the lines of principle of operations, Construction, applications, advantages and disadvantages. For the third type, you can go through the detailed article of Servo Motor.
Operation Principle and Construction
The operation of all motors are generally based on two principles which are; Amperes law and faraday’s law. The first law states that an electrical conductor placed in a magnetic field will experience a force if any current flowing through the conductor has a component at right angles to that field. The second principle states that if a conductor is moved through a magnetic field, then any component of motion perpendicular to that field will generate a potential difference between the ends of the conductor.
Based on these laws, electric motors comprises of two main part; A permanent magnet and a bunch of conductors wound into a coil. By applying electricity to the coil it becomes a magnet and based on the fact that magnets repel at like poles and attract at unlike poles, a rotational motion is achieved.
Brushed DC Motor
The brushed DC motor is known to be one of the earliest and simplest motors as it implements the laws described above in the simplest manner. As described in the image below the construction of a brushed DC motor comprises of a fixed stator made of a permanent magnet and a moving armature (Rotor) on which components like the commutator, brushes, and split ring all of which is placed around the motor shaft.
When power is supplied to the motor (through battery or through an AC to DC plugged in source), electricity flows from the source to the armature through the brushes which are usually located on opposite sides of the motors shaft. The brushes (whose presence in the design is a major factor behind the motor’s name), transfer electric current to the armature through physical contact with the commutator. As soon as the armature (the coil of wire) is energized, it begins to behave like a magnet and at that point its poles start repelling the poles of the permanent magnet which makes up stator. As the poles repel, the motor shaft to which the armature is attached begins to rotate with a speed and torque that depends on the strength of the magnetic field around the armature.
The strength of the magnetic field is usually a function of the voltage applied at the brushes and the strength of the permanent magnet used for the stator.
Brushless DC Motors
Even though they use the same principle of electromagnetism, brushless motors on the other hand are more complex. They are a direct result of efforts made to improve the efficiency of Brushed DC motors and can be simply described as motors who do not adopt the use of brushes for commutation. However, the simplistic nature of that description gives way to questions on how the motor gets powered and how motion is achieved without brushes which I will try to explain.
Contrary to the construction of the brushed motors, In brushless motors things are flipped around. The armature which in the case of the brushed motor, rotates within the stator, is stationary in brushless motors and the permanent magnet, which in brushed motors is fixed, serves as the rotor in a brushless motor. Simply put, the stator for brushless DC motors is made up of coils while its rotor (to which the motor shaft is attached) is made up of a permanent magnet.
Since brushless motor eliminates the use of brushes to provide power to the armature, the switching (commutation) becomes more complex and is performed electronically using additional set of electronic components (like an amplifier triggered by a commutating component like an optical encoder) to achieve motion. Commutation algorithms for Brushless DC motors can be divided into two; Sensor-based and senseless commutation.
In sensor-based commutation, sensors (e.g hall sensor) are placed along the poles of the motor to provide feedback to the control circuitry to help it estimate rotor position. There are three popular algorithms employed for sensor-based commutation;
- Trapezoidal commutation
- Sinusoidal commutation
- Vector (or field-oriented) control.
Each of these control algorithm has its pros and cons and the algorithms can be implemented in different ways depending on the software and the design of the electronics hardware to make necessary changes.
In sensorless commutation on the other hand, instead of sensors being placed within the motors, the control circuitry is designed to measure the back EMF to estimate rotor position.
This algorithm performs pretty well and is at a reduced cost as the cost of the hall sensors is eliminated but its implementation is a lot more complex compared to the sensor based algorithms.
Advantage and Disadvantages
In brushed DC motors, the brushes are in constant contact with the rotating commutator. This leads to a considerable amount of friction being generated and this in turn leads to the loss of energy to heat and gradual wear of the brushes. Thus, Brushed DC motors have low efficiency and requires periodic maintenance. This creates a lot of friction, and friction equals heat (energy loss) and wear and tear. Brushless DC on the other hand are essentially frictionless and thus have really high efficiency, require zero maintenance and last longer than brushed DC motors.
However, brushed DC motors are very cheap compared to their brushless counterparts due to the simple nature of their design. Brushless DC motors on the other hand are quite expensive due to their complex design and the extra cost of the additional electronics components (controllers) required to drive them.
Applications
While brushless DC motors are more popular these days, brushed DC motors are still used in day to day home appliances, kids toys, and in industrial applications due to the ease with which their speed to torque ratio can be varied. Due to their low cost, they are used in applications where the host device could fail before the motors.
Brushless DC motors on the other hand have found applications in all sort of devices, from medical equipments, robots and drones to electric cars, power tools etc. They are essentially used in applications that require high efficiency, longevity and are worth the cost.
Factors to consider when selecting between the Brushless and Brushed DC Motors
Asides speed, torque, power rating and other basic requirements for your application below are three factors I feel could also be good to consider when making a decision on the type of motor to deploy for your application.
- Duty Cycle/ Service Life
- Efficiency
- Control/Actuation
- Cost
Duty Cycle/ Service Life
Service life describes how long the motor is required to operate before failing and at what duty cycle. This is important because brushed DC motor as mentioned earlier are susceptible to wear due to the friction between the brushes and the Commutator. Thus it is important to ensure the application is one in which the motor will be functional throughout the service life or an application in which servicing the motor will be deemed normal and inexpensive if brushed DC motors are to be used. A good example of this is in children toys, where the toys are usually thrown away or damaged before the motor wears out. In applications with long service life and servicing the motor is not a viable option, brushless DC motors are usually the wise option.
Efficiency
Generally, Brushless DC motors have a higher overall efficiency compared to brushed DC motors but there have been cases of Iron-less core brushed motors with superior efficiency compared to equivalent brushless motors. However, it is important to evaluate the overall required efficiency and compare it with that of each motor before making a decision. In most cases where efficiency is the deciding factor, brushless DC motors usually win.
Control/Actuation
This is usually one of the major setbacks when it comes to the use of brushless DC motors. The additional requirements like controllers etc., makes the actuation more complex compared to that of brushed DC motors which could be powered/actuated methods as trivial as connecting a battery across its terminals. You should ensure the amount of complexity involved with using a brushless DC motor for the project is justified and the supporting electronics like the controllers are readily available. Irrespective of the simplicity of brushed DC motors, they are sometimes not suitable for high precision applications. While Brushed DC motor can be easily connected to the controller like Arduino, it is much complex to connect a BLDC with Arduino Uno, however the ESC (Electronic Speed Controller) makes it easier to interface a BLDC with a microcontroller.
Cost