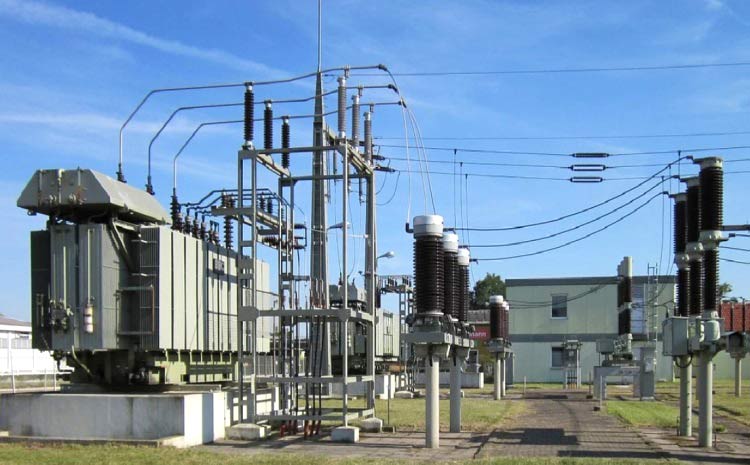
Transformers are one of the most critical and expensive components of any distribution system. It is an enclosed static device usually drenched in oil, and hence faults occurring to it are limited. But the effect of a rare fault can be very dangerous for the transformer, and the long lead time for repair and replacement of transformers makes things even worse. Hence power transformers protection becomes very crucial.
Faults occurring on a transformer are mainly divided into two types, which are, external faults and internal faults, to avoid any danger to the transformer, an external fault is cleared by a complex relay system within the shortest possible time. The internal faults are mainly based on sensors and measurement systems. We will talk about those processes further in the article. Before we get there, it is important to understand that there are many types of transformers and in this article, we will discussing mainly about power transformer that is used in distribution systems. You can also learn about the working of power transformer to understand the basics of it.
Basic protection features like overexcitation protection and temperature-based protection can recognize conditions that eventually lead to a failure condition, but complete transformer protection provided by relays and current transformers are appropriate for transformers in critical applications.
So in this article, we will talk about the most common principles used to protect transformers from catastrophic failures.
Table of Contents
- Transformer Protection for Different Types of Transformers
- Common Types of Transformer Protection
- Overheating Protection in Transformers
- Overcurrent Protection in a Transformer
- Differential Protection of Transformer
- Restricted Earth Fault Protection
- Buchholz (Gas Detection) Relay
- Over-fluxing Protection
Transformer Protection for Different Types of Transformers
The protection system used for a power transformer depends on the transformer's categories. A table below shows that,
Category | Transformer Rating - KVA | |
1 Phase | 3 Phase | |
I | 5 - 500 | 15 - 500 |
II | 501 - 1667 | 501 - 5000 |
III | 1668 - 10,000 | 5001 - 30,000 |
IV | > 10,000 | >30,000 |
- Transformers within the range of 500 KVA fall under (Category I & II), so those are protected using fuses, but to protect transformers up to 1000 kVA (distribution transformers for 11kV and 33kV) Medium Voltage circuit breakers are usually used.
- For transformers 10 MVA and above, which falls under (Category III & IV), differential relays had to be used to protect them.
Additionally, mechanical relays such as Buchholtz relays, and sudden pressure relays are widely applied for transformer protection. In addition to these relays, thermal overload protection is often implemented to extend a transformer’s lifetime rather than for detecting faults.
Common Types of Transformer Protection
- Overheating protection
- Overcurrent protection
- Differential Protection of Transformer
- Earth Fault Protection (Restricted)
- Buchholz (Gas Detection) Relay
- Over-fluxing protection
Overheating Protection in Transformers
Transformers overheat due to overloads and short-circuit conditions. The allowable overload and the corresponding duration are dependent on the type of transformer and the class of insulation used for the transformer.
Higher loads can be maintained for a very short amount of time if it is for a very long time, it can damage the insulation due to temperature rise above an assumed maximum temperature. The temperature in the oil-cooled transformer is considered maximum when it is 95 °C, beyond which the life expectancy of the transformer decreases, and it has detrimental effects on the insulation of the wire. That is why overheating protection becomes essential.
Large transformers have oil or winding temperature detection devices, which measure oil or winding temperature, typically there are two ways of measurement, one is referred to hot-spot measurement and second is referred to as top-oil measurement, the below image shows a typical thermometer with a temperature control box from reinhausen used to measure the temperature of a liquid insulated conservative type of transformer.
The box has a dial gauge which indicates the temperature of the transformer (which is the black needle), and the red needle indicates the alarm set point. If the black needle surpasses the red needle, the device will activate an alarm.
If we look down, we can see four arrows through which we can configure the device to act as an alarm or trip, or they can be used to start or stop pumps or cooling fans.
As you can see in the picture, the thermometer is mounted on the top of the transformer tank above the core and the winding. it's so done because the highest temperature is going to be at the center of the tank because of the core and the windings. This temperature is known as the top oil temperature. This temperature gives us an estimate of the Hot-spot Temperature of the transformer core. Present-day fiber optic cables are used within the low-voltage winding to accurately measure the temperature of the transformer. That is how overheating protection is implemented.
Overcurrent Protection in a Transformer
The overcurrent protection system is one of the earliest developed protection systems out there. The graded overcurrent system was developed to guard against overcurrent conditions. Power distributors utilize this method to detect faults with the help of the IDMT relays. That is, the relays have:
- Inverse characteristic, and
- Minimum time of operation.
The capabilities of the IDMT relay is restricted. These sorts of relays have to be set 150% to 200% of the max rated current, otherwise, the relays will operate for emergency overload conditions. Therefore, these relays provide minor protection for faults inside the transformer tank.
Differential Protection of Transformer
The Percentage Biased Current Differential Protection is used to protect power transformers, and it is one of the most common transformer protection schemes that provides the best overall protection. These types of protection are used for transformers of rating exceeding 2 MVA.
The transformer is star-connected on one side and delta-connected on the other side. The CTs on the star side are delta-connected, and those on the delta-connected side are star-connected. The neutral of both transformers is grounded.
The transformer has two coils, one is the operating coil and the other is the restraining coil. As the name implies, the restraining coil is used to produce the restraining force, and the operating coil is used to produce the operating force. The restraining coil is connected to the secondary winding of the current transformers, and the operating coil is connected in between the equipotential point of the CT.
Transformer Differential Protection Working:
Normally, the operating coil carries no current as the current is matched on both sides of the power transformers. When an internal fault occurs in the windings, the balance is altered, and the operating coils of the differential relay start producing differential current between the two sides of the transformer. Thus, the relay trips the circuit breakers and protects the main transformer.
Restricted Earth Fault Protection
A very high fault current can flow when a fault occurs at the transformer bushing. In that case, the fault needs to be cleared as soon as possible. The reach of a particular protection device should be limited only to the zone of the transformer, which means that if any ground fault occurs in a different location, the relay allocated for that zone should get triggered, and other relays should stay the same. So, that is why the relay is named a Restricted earth fault protection relay.
In the above picture, the Protection Equipment is on the protected side of the transformer. Let's assume this is the primary side, and let's also assume there is a ground fault on the secondary side of the transformer. Now, if there is a fault on the ground side, because of the ground fault, a Zero Sequence Component will be there, and that will circulate only on the secondary side. And it will not be reflected in the primary side of the transformer.
This relay has three phases; if a fault occurs, it will have three components: the positive sequence components, the negative sequence components, and the zero sequence components. Because the positive sequence components are displaced by 120*, so at any instant, the sum of all the currents will flow through the protection relay. So, the sum of their currents will be equal to zero, as they are displaced by 120*. Similar is the case for the negative sequence components.
Now, let us assume a fault condition occurs. That fault will be detected by the CTs as it has a zero-sequence component and the current starts flowing through the protection relay. When that happens, the relay will trip and protect the transformer.
Buchholz (Gas Detection) Relay
The above picture shows a Buchholz relay. The Buchholtz relay is fitted between the main transformer unit and the conservator tank. When a fault occurs within the transformer, it detects the released gas with the help of a float switch.
If you look closely, you can see an arrow, gas flows out from the main tank to the conservator tank. Normally, there should not be any gas in the transformer itself. Most of the gas is referred to as dissolved gas, and nine different types of gases can be produced depending on the fault condition. There are two valves at the top of this relay, these valves are used to reduce the gas build-up, and it's also used to take out a gas sample.
When a fault condition occurs, we have sparks between the windings or between the windings and the core. These small electrical discharges in the windings will heat the insulating oil, and the oil will break down, thus producing gases. The severity of the breakdown, detects which glasses are created.
A large energy discharge will have a production of acetylene, and as you may know, acetylene takes a lot of energy to produce. And you should always remember that any type of fault will produce gases, by analyzing the amount of gas, we can find the severity of the fault.
How the Buchholz (Gas Detection) Relay Works?
As you can see from the image, we have two floats: an upper float and a lower float. Also we have a baffle plate that is pushing down the lower float.
When a large electrical fault occurs, it produces a lot of gas that the gas flows through the pipe, which shifts the baffle plate, and that forces the lower float down. Now we have a combination, the upper float is up and the lower float is down, and the baffle plate has tilted. This combination indicates that a massive fault has occurred. which shuts down the transformer, and it also generates an alarm. The image below shows exactly that,
But this is not the only scenario where this relay can be useful, imagine a situation where inside the transformer there is a minor arcking that is happening, these arks are producing a small amount of gas, this gas produces a pressure inside the relay and the upper float gets down displacing the oil inside it, now the relay generates an alarm in this situation, the upper float is down, the lower float is unchanged and the baffle plate is unchanged if this configuration is detected, we can be sure that we have a slow accumulation of gas. The image below shows exactly that,
Now we know we have a fault, and we will bleed out some of the gas using the valve above the relay and analyze the gas to find out the exact reason for this gas build-up.
This relay can also detect conditions where the insulating oil level falls due to leaks in the transformer chassis, in that condition, the upper float drops, the lower float drops, and the baffle plate stays in the same position. In this condition, we get a different alarm. The image below shows the working.
With these three methods, the Buchholz relay detects faults.
Over-fluxing Protection
A transformer is designed to operate at a fixed flux level. Exceeding that flux level and the core gets saturated, the saturation of the core causes heating in the core that quickly follows through the other parts of the transformer, which leads to overheating of components, thus overflux protection becomes necessary, as it protects the transformer core. Over-flux situations can occur because of overvoltage or a reduction in system frequency.
To protect the transformer from over-fluxing, the over-fluxing relay is used. The over-fluxing relay measures the ratio of Voltage / Frequency to calculate the flux density in the core. A rapid increase in the voltage due to transients in the power system can cause overfluxing, but transients die down fast therefore, the instantaneous tripping of the transformer is undesirable.
The flux density is directly proportional to the ratio of voltage to frequency(V/f), and the instrument should detect the ratio if the value of this ratio becomes greater than unity. This is done by a microcontroller-based relay which measures the voltage and the frequency in real-time, then it calculates the rate and compares it with the pre-calculated values. The relay is programmed for an inverse definite minimum time (IDMT characteristics). But the setting can be done manually if that is a requirement. In this way, the purpose will be served without compromising the over-flux protections. Now, we see how important it is to prevent the tripping of the transformer from over-fluxing.
Hope you enjoyed the article and learned something useful. If you have any questions, leave them in the comment section or use our forums for other technical queries.