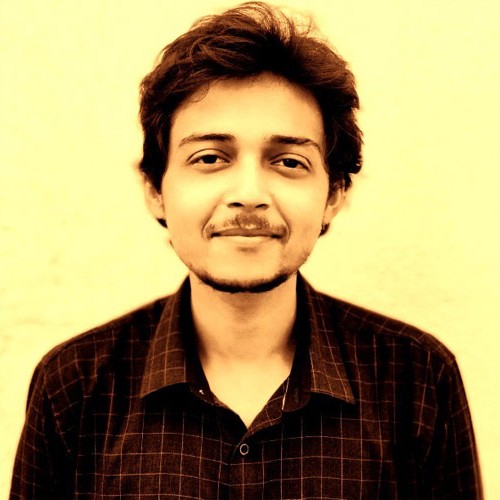
Electric mobility is the need of the hour and over the past few years, the interest level around Electric vehicles has increased tremendously. Batteries are an important part of electric vehicles and they cover about 40% of the total cost of manufacturing of the electric vehicles. Study shows that the Li-ion battery market in India will grow by about 132 GWh by 2030 growing at a compound annual growth rate (CAGR) of 35.5% and Many automobile giants are diverting their focus on electric vehicle manufacturing.
‘Cell Propulsion’ is the only Indian start-up that is designing and developing electric power train technology for buses and other heavy commercial vehicles. In the quest to understand more about the EV market and get answers to some of the questions that we were curious to know about, the Circuit Digest team reached out to Mr. Supritam Naskar, CTO of the company.
Supritam Naskar holds a graduate degree in Aerospace Engineering from IIST. His area of interest is interdisciplinary technology development with a keen interest in the field of Robotics, Power Systems, and Electric Machines. He has worked in ISRO and was responsible for manufacturing, testing, assembly, and quality control of launch vehicle payload fairings. Besides, he has experience of working in multiple multidisciplinary projects in the domain of space robotics and spacecraft mechanisms.
Q. What is Cell Propulsion all about? What solutions do you offer and what are your core strengths?
Cell Propulsion is an electric mobility company based in Bangalore, India that designs and develops electric power trains and integrated electric mobility solutions to lead the electrification of commercial vehicles. We are building expertise and core IP in multiple areas like electric motors and motor drives, Li-ion battery packs, BMS, chargers, and associated operating software stack. These offerings are being commercialized as individual products, as integrated systems, and also as part of fully managed solutions for light electric commercial vehicles and electric buses.
Cell Propulsion is the only Indian start-up designing and developing electric power train technology for buses and other heavy commercial vehicles.
Q. How did the Cell Propulsion team come together and how did the company get off the ground?
The core team at Cell Propulsion came together from a common background of working for the Indian Space Research Organization (ISRO). Nakul (CEO + Founder) and I, both graduated together from the Indian Institute of Space Science and Technology under the Department of Space with Degree in Aerospace Engineering and started our careers in ISRO in 2011. There we met Paras (COO + Founder), a graduate in Mechanical Engineering from Punjab Technical University, who worked in the same division as Nakul. In 2016, after working for 5 years in ISRO, we decided to put all our learning to accelerate the growth of electric vehicles in the country as we believe that electric vehicles will have a very deep impact in the world of mobility in the years to come.
Nakul has experience of working in the domain of launch vehicle and spacecraft propulsion. He has worked at the Indian Space Research Organization (ISRO) on their launch vehicle engines. Subsequently, he has led the design and development of the lunar lander propulsion system, and the design & development of solar-powered electric aircraft. At Cell Propulsion, he handles leading the fundraising, and overall strategy of the company.
Paras has worked on developing all-terrain vehicles. He has worked at ISRO on launch vehicle engine ignition systems. Subsequently, he has worked on the design and development of thermal control systems for a lunar lander, satellites, the solar-powered aircraft, electronics hardware, and space grade lithium batteries. At Cell Propulsion, he handles managing company operations like general administration, HR, Finance & Accounts, Compliance, and Supply Chain.
The company began full-time operations in Feb-2017 and planning for beginning this venture began in 2016 when the core team saw a big opportunity in developing solutions for the electrification of terrestrial vehicles given their experience of working on electric aircraft, and other safety-critical aerospace systems.
Q. Your company was one of the three to win the Better Bus 2018 award from WRI India and FedEx. How was the experience?
The Better Bus Challenge was a great opportunity as we had begun scaling up our technologies and 48V systems for high voltage and high power applications (eBuses and eTrucks) at the beginning of 2018. Better Bus provided the right platform to deploy our technology in the field by working with Bangalore Metropolitan Transport Corporation (BMTC) to convert one of their buses to electric, getting it homologated and operating it for public transportation. We have successfully converted the bus to electric and currently we are doing road tests for preparing the bus for homologation. This project has been a roller coaster ride for us, working with BMTC, and with all the support from WRI, it has been a learning experience like no other. As of today we have successfully test run the retrofitted bus a few times and hoping to start some rigorous testing soon after the COVID 19 situation improves in Bangalore.
Q. Please shed some light on the technical details of the LCV retrofit kit.
Cell Propulsion’s powertrain for LCVs is designed to meet the demanding requirements of the Indian logistics and transportation industry. The modular battery pack architecture enables easy customization of the powertrain for 80km range to 150km range on a single charge. The powertrain can be offered at different operating voltages (48V/ 72V/ 96V) basis the range, power, and tonnage requirements of the customer. The electric powertrain offers at par performance to an ICE drive-train.
The design of the powertrain can be easily customized to offer multiple payload capacities ranging from 600kg to 1200kg. This integrated powertrain can be used for building new eLCVs and can also be used as a conversion kit to retrofit existing LCVs. The major technical specifications of eLCV powertrain are as follows: Top Speed - 60kmph, Grade ability - 21%, Peak torque - 200Nm, Peak Power - 40kW, Continuous Power - 20kW
Q. Cell Propulsion designs high power battery packs ranging from 1KWH to 100KWH. What are the challenges in designing these high current and high voltage battery packs?
All our products are designed keeping the prime focus on safety, reliability, and modularity. The battery pack for EV applications has also been designed keeping in mind these governing drivers. Each battery module has been rated for high currents (upwards of 500A) and low voltage (24V) while being compliant to AIS048 standards for use in the automotive industry. These modules are connected in series to achieve higher voltages (48V to 800V). Our in-house developed Battery Management System (BMS) along with the High Voltage Power Distribution Unit (HV-PDU) enables operation of these modules for all voltages and capacities.
Some of the key challenges in designing the battery modules for high current output are:
- Stringent requirement of safe and reliable high-performance thermal management system, we have implemented a highly compact and cost-efficient liquid cooling system for our battery packs.
- Design and development of current conductors for the battery pack. As the voltage drop and the power losses in the conductors have to be minimized, material selection for the conductors is of utmost importance.
- Insulation monitoring of HV system and implementation of detection of breach of insulation in the powertrain is a challenge to ensure quick response for the utmost safety of the system
Q. Indian companies are facing logistics problems when importing cells. How does your company deal with the problem? How does your supply chain management work?
The performance and reliability of the battery packs are highly dependent on the cells used. Due to the lack of indigenous manufacturing of Li-ion cells, every Indian EV company will have to face logistical challenges to source cells. However, there are few methods to reduce problems related to the cell supply chain: Source cells from suppliers already having BIS certificate for their products to reduce delays at customs, work with multiple cell suppliers and logistics (3PL) firms to reduce shipping risks and delays, proper due diligence of the manufacturing facilities of various cell suppliers to assess their process reliability and process risk, and managing a large inventory of cells for R&D and realization of battery pack hardware.
Q. Tell us about your 48V Battery Management System (BMS). Are you planning to expand your designs on BMS?
The BMS has been completely designed in-house for EV applications as per established automotive standards while complying with ISO26262 and ASIL B/C standards. The BMS is responsible for managing and ensuring the safe operation of battery modules. BMS is responsible for over-voltage protection during charging, pre-charging during discharging, over current protection during charge/discharging, short circuit protection, cell balancing, SOH, SoC, capacity fade, and useful battery life estimation and reporting.
The 48V BMS is currently being upgraded for high voltage eHCV applications. Due to their modular design, multiple BMS are connected in series via CAN for high voltages up to 800V. They are connected in a Master-Slave architecture where the slave BMS in every battery module is connected to Master BMS via CAN. Besides upgrading to high voltage operation, development work is being done to develop more features for BMS connectivity like Over the Air updates for the firmware.
Q. What kind of charging solutions does cell propulsion provide? Where are they deployed?
We are involved in the design and development of single-phase and 3-phase, on-board, and off-board EV Chargers. Our chargers are OCPP compliant. We have developed both AC and DC chargers, working currently towards high power charging system design. We partner with charge point operators and solar companies for planning and commissioning of EV charging infrastructure and upstream power supply infrastructure.
Q. Cell Propulsion also provides Vehicle to cloud (V2C) connectivity using its telematics module “LINK”. Please share some of the technical aspects of it.
Connectivity is an indispensable part of operating electric vehicles. In contrast to ICE vehicles, the EVs (specifically battery packs) require constant monitoring for their safe and reliable operation. This tracking is enabled remotely by our telematics module LINK which interfaces with an EV’s on-board computer to gather data of all ECUs (including BMS and motor drives). This data is pushed to the cloud for vehicle health monitoring and advanced data analytics. Some of the key features and technical specifications of LINK are 4G enabled, OTA capability, 9 axis IMU, GLONASS/GPS.
LINK also comes with Cell Propulsion's client-side application, which provides the client with analytics based on the vehicle and powertrain data.
Q. How do you see the market for EV solution providers in India? Why do you think the adaption of EV is slow in India?
We see massive growth potential for EV solution providers in India. EVs bring considerable benefits to owners on a total cost of ownership basis. These benefits are not only linked to savings in fuel and maintenance costs but are also about ease and convenience in use and operation. The driving experience and comfort are also much better compared to ICE vehicles. Encouraging government policies and initiatives also instill confidence in the growth of the EV market. The e2W, e3W, and electric CV segments will drive the growth of this market with other segments like personal passenger vehicles, off-road vehicles, etc. following the trend of EV adoption.
Lack of indigenous technology and product development has led to low competition in the market. Due to this, there is a lack of good quality EV products which are also reasonably priced. This coupled with low penetration of charging infrastructure has resulted in slow adoption of EVs. We believe that the market is currently not being driven by demand rather by the supply of EVs. We expect that in the coming years there will be an acceleration in adoption as more players enter the market and supply constraints get resolved.
Q. As an electric mobility company from India, what technical problems do you often face when developing new solutions?
Some key technical problems that we currently face are the lack of qualified technical talent to work on the development of high voltage, high power equipment for EVs, lack of technical expertise and know-how to lead the development of such multidisciplinary projects. Moreover, lack of robust power grid to support large scale deployment of EVs, and lack of standardization across the industry.
Q. Who are your current and future potential customers? How are you planning to take your products to the market?
Our target customer segment is commercial vehicle fleet owners and operators. We work with logistics and cargo companies involved in intra-city (first/last mile) delivery of cargo and goods. We also work with intra-city bus operators like STUs, school buses, corporate employee transport, etc. In the coming years as our EV technology matures, we’ll also begin serving inter-city logistics, inter-city buses, and long-haul trucking.
Our go-to-market strategy is to offer retro-fitted/re-manufactured eLCVs and eBuses to our customers as part of our fully managed mobility solutions. This reduces the risk for our customers as they begin to experiment with EVs in their operations using old assets converted to electric at a lower cost. We act as a one-stop solutions provider to our customers and provide support in all aspects of using and deploying EVs in their fleets. We are currently doing pilots with few early adopters and taking large volume orders for eLCVs while gearing up for their mass production.