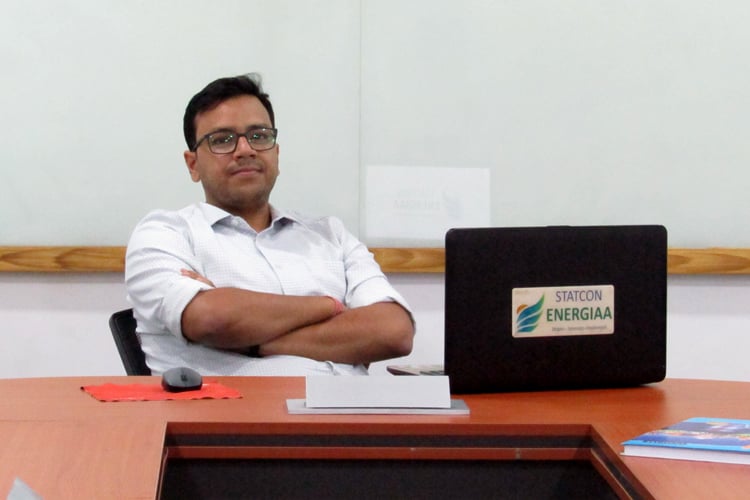
In today’s time, Electrical Energy is essential for running the world. But the climate change and depletion of non-renewable resources have forced us to look for alternative sources of energy, sustainable sources of energy, and hence Renewable sources of energy. But be it a renewable or conventional source of energy, the Generation, Transmission, Distribution, and even Storage of energy depends upon the Power Electronics. Statcon Energiaa is one of the leading manufacturers of high-power electronics in the country. They deal in renewable energy systems, energy storage systems battery charges, frequency converters, load banks, and much more. To know more about the company, the power electronics industry, and renewable energy systems, we have with us Mr. Pranjal Pande, the Director of Statcon Energiaa.
Q. Please tell us more about Statcon Energiaa, its vision and the product and services your company provides?
Statcon Energiaa is one of India's leading power electronics manufacturing companies. The company was started in 1987 by Mr. Manoj Pande who is the Managing Director of the company. The initial idea was to cater to the high-power supply demands in big industries and government sectors like Integrated Power Supply, huge battery chargers, etc. At the time when the company was started, the team realized that India is in a dire need of efficient and scalable high electronics manufacturing companies, which can cater to the huge growing demand. It was then that the team thought of indigenizing as much as they could - to make almost all of their components or use those made in India. The idea was to be a global player based in India. and be one of the global players who are based in India. For the years that have gone by over the years, the company has successfully adopted a sustainable development vision, where India’s and the world’s supply can shift onto renewable power electronics. We want to assert that world supply can shift onto renewable power electronics.
Q. The company is focusing on Renewable Energy, can you shed some light on the current Renewable Energy Market both in Indian as well as in the global context?
India is one of the blessed countries to have a lot of solar energy and there has there been a sufficiently experienced ecosystem in India to cater to the rising demand. The key factor in rooftop storage/solar across the world is that in more developed countries, it is mainly to do with cost reduction of the grid electricity that they are getting. Because, they are already getting 24x7 electricity supply, and of course, it is a bit high. So, they are using solar to offset the entire usage.
In India, apart from the cost reduction of the grid, a major application is to use solar energy as backup power in order to meet the country’s energy demands. So, compared to the other developed countries where they are replacing their existing generation units with a renewable source, in India we also have to harness solar energy in order to fulfill our demands on top of the cost reduction demand. This makes India one of the key markets globally. And that's why you see so many suppliers dealing in renewable energy equipment here in India. Renewable-wise, we are very confident that 10 years down the line, there would be no decrease in demand; the growth would always be there.
Q. What challenges do you face while developing a product, since you are competing globally, you have to keep innovating and adapting new technologies. So, how difficult it is, and what procedures do you follow while developing a product?
On the development part, the only thing that you can do is to listen to your customers about their requirements. We have a variety of different customers, distributors, system installers, direct, and tender-based products. Each application is different and you don't have a one-size-fits-all solution. We have specifically built a Projects Team that goes to the customer to understand the entire application. They go with the entire electrical study and survey the site. Next, they discuss with their R&D team to design a specific Installation Plan. For example, we had a case of a Cold Storage in Etawah, U.P. that had a very high motor load of 150 hp. The plant also suffered from eight hours of power cuts daily. We designed a system where the entire plant with 150 hp of motor and 40kW of load would run on a specialized solar inverter that has VFD panels attached to it. It has flooded Lead-Acid batteries, and the entire plan runs uninterrupted and seamlessly using storage and solar energy throughout the day. The amount of savings that you get is the amount of electricity that you were using earlier. Our solar solution offset all the diesel that was going into the Digital Generator (DG) set – whose use is negligible now.
Cold storage is a unique application - whenever there is a power cut, the ammonia level goes down. Since now the interruption is not there, therefore, you don't have to compensate extra energy to build up the ammonia levels again, it stays right there because you have an uninterrupted, seamless power supply. This is one of the applications that we have developed and that has come to us because our Projects Team is working very hard along with the customer/clients to understand their needs and customization.
Q. Statcon Energiaa is one of the largest manufacturers of solar inverters and energy storage systems in our country, would you like to tell us about your clients? Do you cater to global clients too?
If you make one equipment or technology in power electronics, its applications cover several sectors. For example, the converter that goes inside an inverter, the same kind of converters in a larger setting would be very useful for the Defence sector too, because when these large ships and large submarines come to the shore, their batteries have to be immediately discharged and then charged again and then it has to go back sailing because it cannot stay on the shore for a long period. We have catered heavily to the Indian Defence sector as our long-standing good client. We make Rectifiers and Load Banks in Megawatt capacities which no one in India has sustainably been able to do till now. We also design and manufacture the Ground Power Unit (GPU, the starting units) for the Indian Air Force aircrafts.
Since no aircraft can start on its own, they all need a GPU to get started. Globally, we found that there are ABB and Siemens in this sector. They have a good brand name that comes up with A-line inverters being installed, but we are confident that we are in no way lesser than such global names. We have built even more advanced systems which replaced a lot of such big companies’ systems in microgrids across Africa, Southeast Asia as well. Today, we have around 250 units that are working as microgrids in Myanmar. We supplied to a lot of hydropower stations in hydro microgrids in Africa as well. It is more ‘where’ the requirement is - if the customer wants an energy solution, then you have a global market available to supply your products.
Q. You recently completed a project (DC converter) for the Indian Navy. Would you be able to tell us about that project?
It is a rectifier that converts AC to DC like mobile chargers. It has 1520 kilowatts of power. When a ship goes sailing or when a submarine goes for sailing, it has huge battery banks. Whenever this comes on to the shore after days of sailing, the batteries have to be discharged through a load bank. This also is good for its health and then it is charged. So, the rectifier does the charging part of the entire thing. This AC-DC charger is a very high-capacity charger to compensate for the heat that is being generated into the system. So, you need the kind of components that will withstand the vibrations when this thing moves. It should not so bulky thing else transportation would be a problem. This is where we excel. We work according to the local conditions of the project. It is about the engineering that is specific to the kind of application that you have to fulfill. This was a highly successful product for us and this is the first time that such a high-rated project is developed. We are making it up to double this rating now. It is almost 3 MW – 3000 Kilowatts – and it will be completed very soon.
You can check the video of the 1.5 MW mobile rectifier charger here.
Q. What impacts did covid have on the power electronics market and Renewable Energy Industry? How did the lockdowns and semiconductor shortages impact your company and other companies working in the Renewable Energy Sector?
Everyone who is using some kind of chip or semiconductor is facing either huge lead times or increased costs. For example, we were using an IC for Rs 290, that price has gone to Rs. 2900 and if we want it at the same rate as before, the time of delivery is increased to 52 weeks. After Covid-19, there was a lot of pent-up demand and the market again bounced back but the supply is yet to meet the demand as it was doing before. And this semiconductor shortage is not something that I see being resolved very fast or within this year, it will take at least the first quarter of next year, if not more, to normalize. It has caused a domino effect. So there will be some shortages, but then again, companies have to plan for that better.
Q. How do you see the current energy crisis that is looming over China, how will it impact your company, and also the small EPC companies in our country? Do you think that Indian manufacturers might get some advantage out of it?
Even before this, China's factories were facing problems because of this Covid-19 induced lockdowns. The invasion of their ports had closed, so supply chains are already suffering. Now, with this news that their factories are running for three hours or four hours daily, their production output will decrease. If their production output decreases, then the world's production output also decreases, given the global dependency on China. Power electronics is globally a highly connected, dependent economy, and everyone depends on everyone else to do their part. If China’s factory production goes down, then one of the major things to suffer would be steel, and if it suffers, then almost everyone suffers. We are hoping that they find some turnaround fast enough that their power industry can provide enough power during these times. Because even if Indian manufacturers may have some short-term gains but what we need to realize is that we need to immediately invest those gains into our permanent capability increase. Otherwise, it'll run into the same problems. So, some very few people for very little time will see some gains. But other than that, it's not very good for the global industry.
If we have to take advantage of this situation, we have to innovate a lot faster. For example, almost all the displays that we use on the phone and everywhere else, come from China. There are a few things that if you take from China, as compared to if you take from somewhere else, there is a huge difference in cost average. The power sector industry worldwide is dependent a lot on some key components for China only - like the SMT components that are used in circuits. So, if that stops, then the electronic market will eventually slow down a bit. Whatever we have right now, will get us through in the short term, but we have to plan for the future.
Q. Your company’s forte is manufacturing Power Electronics Systems, which is a bit of niche domain in Electrical Engineering, so how hard it is to get the right talent? Do you prefer people with M.Tech in power electronics or take in B.Tech freshers and develop them?
The amount of expertise that is needed for product development is not taught right now in the B.Tech schools, and hence, we are not hiring freshers in large numbers right now. There is a disconnect between the educational curriculum and the industry. So, we usually hire experienced B.Tech candidates or M.Tech students who have done other projects in a similar kind of field since M.Tech is a very dedicated and specialized study. I always talk to the professors first, and then on their recommendations, we interview M.Tech. students before hiring them.
Innovation for the product obviously is taken by power electronics engineers, but in a company, innovations have to take place across a variety of departments. Quality is one such department where there are a lot of B.Tech graduates who study the production techniques and bring about a lot of innovation that helps activate develop the product into what you see right now.
Q. What do you feel about the scope of power electronics as a career in our country and what about the global scenario? Do you have any suggestions for students pursuing their Bachelor’s in Electrical Engineering or want to pursue Power electronics or control systems for masters?
I have completed my Engineering degree from HBTU Kanpur. What I felt during my engineering was that teachers were not very connected to the industry professionals. This, in turn, translated to the students not knowing a lot about these core engineering companies, such as power electronics firms. If I asked fresh B.Tech graduates to list down around 20-30 large companies in India that are doing research in power electronics, it would be very hard for them. That kind of saturated internet presence or marketing presence is not there for such companies, which are the backbone of the overall industrial sector in India. I feel that from the first year itself, students should reach out to these companies and explore on their own. There are a lot of forums where they can go and they should talk to these companies and get some kind of paid/unpaid internship to enhance their knowledge. These things help you understand like what is happening in the industry alongside what they are being taught in the college. My advice would be that students should reach out from the first or second year itself and go to the industry to do some basic research well, and then when they come back, they should select a product project, which is of actual significance to the industry. Like, for example, you were mentioning that you are doing something in EV Auto, so you have such a kind of project, if someone is doing it, then it drastically increases their employability once they are out of college.
All the companies are looking for students who have taken some initiatives on their own while they are in college because, in the four years of B.Tech, they get time to learn about everything, and then, once it opens up their minds to the kinds of things that they can do. We have to realize, and people have to become slightly confident about their abilities in colleges, that they can do things that are relevant in the industry. But for that, they have to go into the industry and study about these things.
Also, the future scope in power electronics is very good. There is a high demand for talented engineers. Furthermore, the salaries of senior power electronics engineers are at par with that of senior IT engineers, albeit having a lower starting salary.
Q. How do you think that R&D in India can evolve? Do we have such a culture in India? Is the government doing something about that?
In one incident where I was in a seminar along with Mr. Anand Mahindra and some prominent industry and country leaders, a Navy officer raised his hand and asked, “Why are you not making indigenous products for India when you have so much money? You should be doing a lot more”. Mr. Mahindra responded, “What you're saying is not wrong. We have money, but we don't have that kind of money to risk. We have it to invest into the business, but we cannot risk so much capital by building some things when the market is not there”. The key takeaway is that money exists for the research, but there is no risk capital for research.
This is a thing that has been a concern for the government too. They have come up with a lot of good things to address that as well. One such thing is TIH which is the Technology Innovation Hub that has been opened up in some eminent colleges like IIT Roorkee, and in a lot of other colleges as well. The industry and the college together submit a project and then evaluate it, and that company has to put in some amount of funds, almost around 10% of the entire budget. The rest of it is supplied by the government. We will get capital, the participating students are going to learn a lot, and the college as a whole will get a lot of knowledge/recognition because the professors will be involved too.
This kind of risk capital mitigation, when it comes to R&D projects has been initiated by the government. There is another scheme called the Technology Development Fund by DRDO. These kinds of projects bring in money from both India and European Union. Also, the colleges get the money which they can then give to the industry to develop the entire project. This is crucial when it comes to Indian companies because we are a very cost-competitive nation. We still take out such amounts for R&D, which is tough for any entrepreneur otherwise. So, this is a good initiative by the government that should be used widely by companies in India.