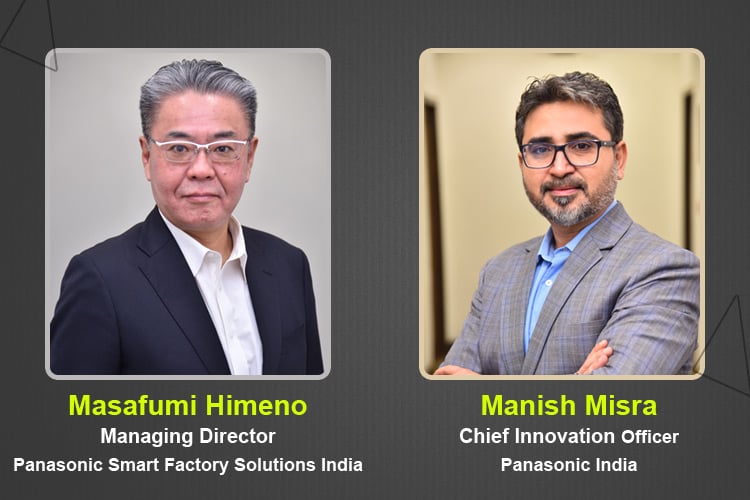
The conventional manufacturing facilities are equipped with lots of hindrances as they rely mostly on outdated machinery, which is very intricate to repair due to high cost. Workers in these factories are often without proper data and they have to constantly supervise the performance and call out for decisions based upon experiences, guess, and sixth sense. With the escalating multiplication of connectivity and data, the usage of industrial IoT is gaining more traction globally. Both industrial IoT and smart manufacturing solutions can transform the manufacturing facilities and help them to operate seamlessly along with crafting a lot of efficiencies. To ease the operations, a week back, Panasonic India has unleashed a first of its kind industrial IoT/smart factory solution, dubbed Miraie Profactory. In this regard, we spoke to Manish Misra, Chief Innovation Officer Panasonic India, and Masafumi Himeno, Managing Director, Panasonic Smart Factory Solutions, India about the current challenges of deploying smart factory solutions, current technology trends of manufacturing facilities, and the future roadmap.
Q. As an industry veteran, what do you think are the biggest challenges of deploying smart solutions in manufacturing facilities? Where do you see the trend?
Masafumi Himeno: First of all, from the customer's perspective, they have issues in capturing the real-time data on the shop floor in terms of breakdowns or in terms of defects. They are not able to judge why this defect is happening. If there is a system, they can capture this data through some digital connections and they will get the information in real-time. They always face the challenge of minimizing defects and breakdowns. Most of the machines are legacy machines that are very old and difficult to capture data. We should have the technology to capture the data through PCs or data loggers. Another challenge is investment because prints and paper works are very expensive for heavy industries. To minimize that we are offering subscription models through our solutions. Suppose if they want to do their own print business, they require a very big system, IT infra in terms of big servers, and IT teams also and that becomes very difficult for mid-sized companies to invest in these criteria. In the age of industry 4.0, machines need to be ready whenever production needs them. Without digitization, it is very difficult to gauge unreported stops or glitches, manual bias, historical data, and overall equipment efficiency.
Q. What is your business model in terms of B2b and how much it has changed since the pandemic?
Masafumi Himeno: Our business model is simply building hardware, manufacturing machines, appliances and then selling it to our manufacturing customers. Apart from this, we would like to promote more smart factory solutions as a subscription to our customers. Not just hardware, now we provide the entire platform and this is from the manufacturing equipment maker's point of view. Now people no need to go down to the factory in front of machines and do multiple paper-based works and this is what we are now changing and trying to bring more innovations in this regard. Pandemic has helped manufacturing companies to accept digital awareness. Two to three years ago before the pandemic, it was very hard to make the manufacturers understand the importance of digital technologies. Since the lockdown, people all over the including the workers in manufacturing facilities have accepted digital transformation as this is making their workload easier.
Q. Being a Japanese global business magnate you have various global competitors from your own soil and other parts of the world. So, how do you manage to move ahead of this competition curve?
Masafumi Himeno: We are basically the manufacturing company, a hardware provider and we understand the pain point of other manufacturers. We are not only a software solutions company because there are many solution providers who don’t have real experience in manufacturing and don’t know how to manage the hardware side like the heavy machines and equipment. We offer not only robots and SMT, but we can also offer solutions for all your machines whether press machine, molding machine, assembly or PLC based. Instead of going to different vendors for different solutions, Panasonic becomes a one-stop solution. We are one of the very few companies in the world that deals with both consumer appliances and B2B products like SMTs and microelectronics hardware. Panasonic ties up with its manufacturing customers to understand how to improve their technology.
Q. What are the biggest challenges you faced while launching Miraie? How it will be a game-changer?
Manish Misra: If you look at the manufacturing industry the area is very vast as there are different types of machines, makers, models, and protocols. Then there is legacy vs non-legacy machines. So, these are some of the things that you know anybody who gets into this space will face a massive amount of parameters to consider. This is when we started thinking about how to sort of abstract all that and make our customer's life easier and that’s when our gateway was conceptualized so that it can work with multiple protocols, various machines, and makers. Also, the idea was how quickly we can deploy this solution, it should not be years or months, it should be weeks or hours.
Q. Which kind of technologies you have implemented while deploying Miraie Profactory? What are the benefits of Miraie Profactory?
Manish Misra: Some of the core technologies are cloud, industrial IoT, and we are using sensors in our data loggers to collect data from non-IoT devices. Then, we are also using mobile technologies and also AI and data science and with these technologies you are able to achieve is that you can see the data in real-time, you understand what kind of wastages are there in the system and what kind of inefficiencies are there and then it helps you to take proactive actions. Earlier data was coming to you manually maybe after a few hours or in a day or two. Right now, data is seen in real-time through our dashboards. If a machine now goes down you can instantly start to understand the root cause of why the machine is down and correct it.
With numerous kinds of brands, machines, and models in the manufacturing domain, the solution Mirair Profactory is fine-tuned and it will assist the domestic manufacturers to make their industry operations completely digitized, which will ultimately help the entire enterprise to value the imperativeness of Industry 4.0. The solution is furnished with several new technologies such as mobile app, IoT, Cloud, and analytics that helps in crafting economies of scale, perk-up production efficacies by monitoring end-to-end operations. The solution is currently available in four variants and is customizable from basic to advanced depending on the requirement with value-added features.
Q. What is your roadmap for the coming years?
Manish Misra: There are a lot of things Panasonic India Innovation Center is working on. A couple of years ago, we launched the basic Miraie for residential IoT and AI-enabled solutions and now we want to expand it into manufacturing sectors through our Miraie profactory. We are looking forward to some innovations in the AR and VR segment as well where remote service will be a possibility so that will reduce the downtime of a machine substantially because if you look most of the factories today are located at the outskirts so it takes a lot of time for a technician to reach those spots.