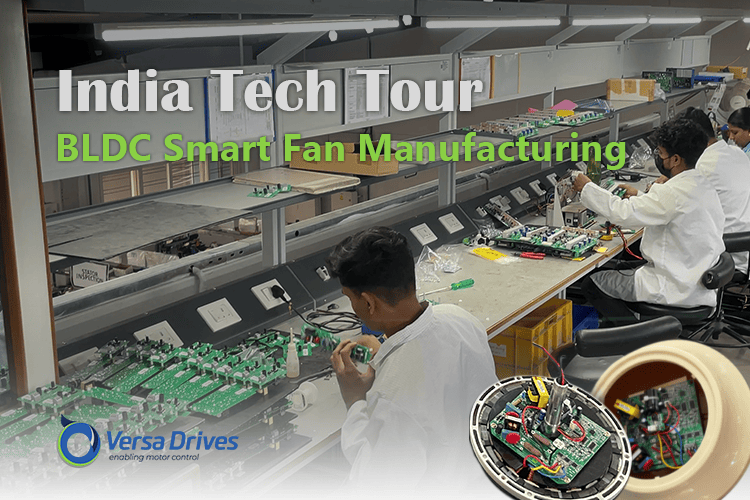
In the busy industrial city of Coimbatore, India, a company has been quietly transforming the way we think about motor control and energy efficiency. Versa Drives Private Limited, founded in 1989 by Durga Krishnamurthy and Sundar Muruganandhan, has grown from a small partnership firm into a prominent leader in custom motor control solutions. During an exclusive industrial visit for the “India Tech Tour Series”, the Circuit Digest team had the opportunity to have an interactive session with the key persons behind Versa Drives including Sundar Muruganandhan (Managing Director and Founder), K. Maheswari (Executive Director) and Dr. Mayur Sundararajan (Business Head). What emerged from these conversations was a story of innovation, determination and a persistent drive to create a sustainable future. In this article of India Tech Tour, let’s explore the insights, knowledge, and vision behind the innovations of Versa Drives, and take a look at their operations on how they are manufacturing India's most efficient BLDC fans.
This series of India Tech Tours is proudly presented in collaboration with DigiKey, a global leader in electronic component distribution. With an extensive catalog of over 15.9 million components from 3,000+ top manufacturers, DigiKey ensures engineers and innovators have access to high-quality parts, fast shipping, and exceptional customer service. Whether you're working on a cutting-edge project or sourcing components for mass production, DigiKey is your trusted partner for all your electronic needs.
Journey of Versa Drives
Versa Drives began its journey as Computer Controls Corporation (CCC), a company focused on designing and manufacturing embedded control systems for machines. Over the years, CCC built a reputation for delivering innovative and aesthetically pleasing solutions to Original Equipment Manufacturers (OEMs) across India. In 2004, the company decided to specialize in motor control products, launching the Versa Drives brand. The name “Versa” was derived from “versatile motor drive” reflecting the company’s commitment to creating adaptable and efficient solutions.
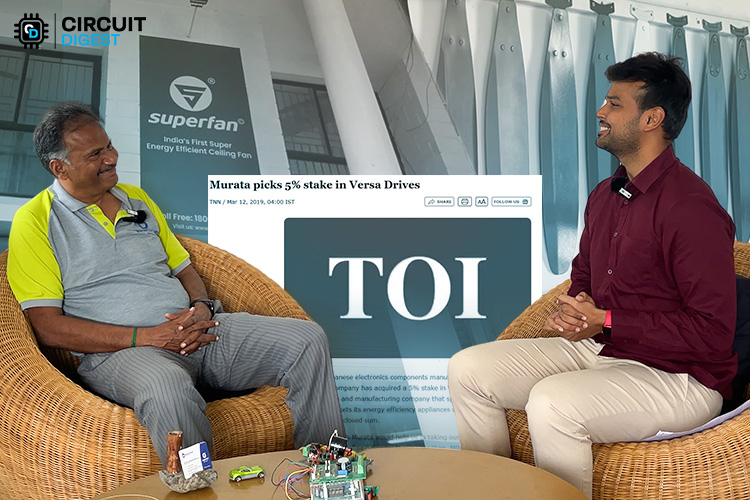
By 2010, Versa Drives had become a private limited company, marking a new phase in its evolution. One of the innovative products of Versa Drives, the Superfan, which is India's first BLDC fan, became a sensation in 2012 when it was launched. Building on the extensive reach and goodwill established by the Superfan, Japanese electronics components manufacturer Murata Manufacturing Company acquired a 5% stake in Versa Drives in 2019. Today, the company is known for its expertise in designing and manufacturing custom motor drives including Variable Frequency Drives (VFDs), Brushless DC (BLDC) motors, and Permanent Magnet Synchronous Motors (PMSM). These products are used in a wide range of applications, from elevators and textile machines to exercise equipment and solar pump controllers.
Expertise of Versa Drives in Motor Control Solutions
The company offers a wide range of custom-designed motor control solutions including:
-
Brushless DC Motors & Drives: Versa Drives designs BLDC motors and drives for appliances and machines, offering a complete motor control solution for OEMs. These motors are highly efficient, making them ideal for replacing traditional single-phase induction motors.
-
Custom-Designed Variable Frequency Drives: VFDs of Versa Drives are designed to meet the specific needs of OEMs. They offer flexibility in motor compatibility (ACIM, BLDC, PMSM), advanced user interface features and conformance to international standards.
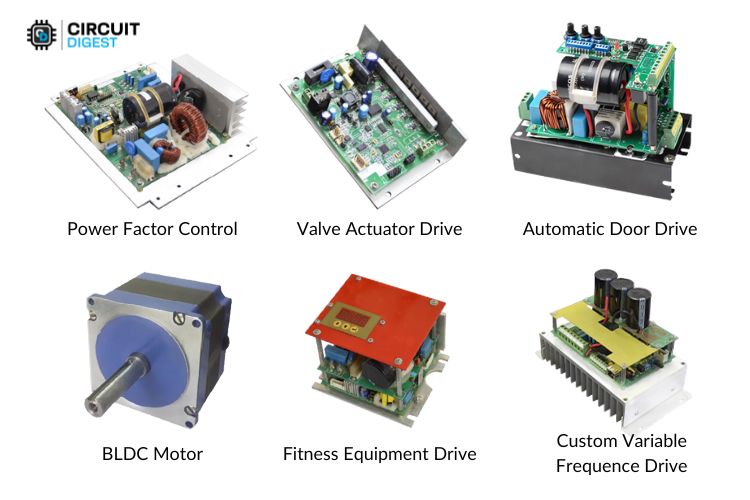
-
DC Bus Operated Inverter Drives: These drives are designed for applications like textile winding machines, offering individual spindle control and efficient power management.
-
Power Factor Control: Versa Drives incorporates active Power Factor Correction (PFC) in its drives, reducing harmonics and ensuring compliance with global standards like EN 61000-3-2.
Overview of Manufacturing Process and Strategic Partnerships
During our conversation with K. Maheswari, the Executive Director of Versa Drives, we gained valuable insights into their manufacturing process from procurement and assembly to the certifications required for electronics manufacturing in India and the challenges they navigate in this dynamic industry. K. Maheswari emphasized that upholding high quality standards and earning customer trust are priority, which is why Versa Drives has offered a 5-year warranty on all its superfan variants since its market debut in 2012.
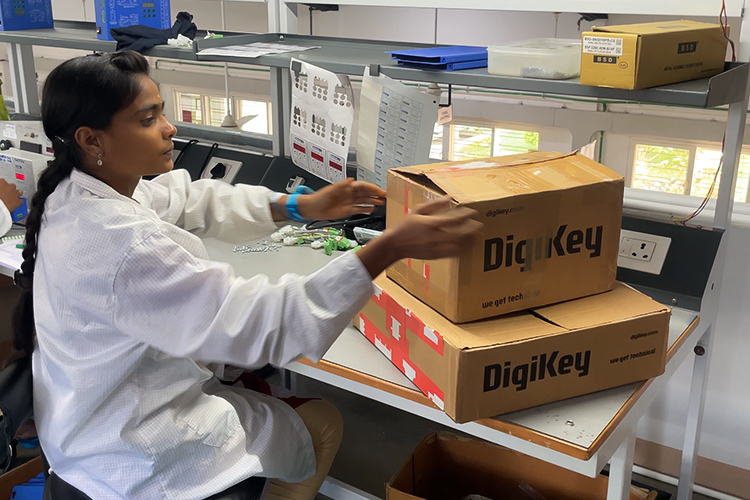
Since 2007, Versa Drives has relied on online distributors like DigiKey to procure essential components, benefiting from their dependable service and innovative solutions. K. Maheswari also commended DigiKey’s recent initiatives including enabling purchases in INR and addressing specific challenges faced by Indian companies. She also noted that some of their vital components for manufacturing are sourced from renowned companies in Coimbatore. Additionally, she mentioned that Versa Drives serves customers throughout India and exports its Superfan product to various international markets, having secured the requisite export certifications.
The Story Behind Superfan from Versa Drives
One of Versa Drive's most remarkable achievements is the creation of Superfan, India’s first super energy-efficient ceiling fan. The story of Superfan is not just about a product, it’s about a vision to transform an entire industry and make a meaningful impact on the environment.
In 2010, during a technology forum, Versa Drives was challenged to address the inefficiency of ceiling fans in India. A study by Prayas, an NGO based in Pune, revealed that the 40 crore ceiling fans in India consumed over 100 million units of electricity daily. This staggering consumption not only strained the power grid but also contributed significantly to carbon emissions and water contamination. Recognizing the urgency of the situation, Versa Drives took up the challenge.
After 18 months of intensive research and development, the company introduced a BLDC motor-based ceiling fan that consumed 50% less electricity than traditional AC induction motor fans. This groundbreaking innovation was launched under the brand name Superfan in 2012.
Impact of Superfan
When Superfan was first introduced, the fan industry was unconvinced about its market potential. The higher cost of BLDC technology and the lack of regulatory pressure made established manufacturers hesitant to adopt the innovation. However, Versa Drives was determined to make a difference.
The company decided to bring Superfan directly to consumers, offering features that were unheard of in traditional fans. The response was overwhelming. Superfan quickly gained popularity, not just for its energy savings but also for its superior performance and advanced features.
Versa Drives didn’t stop there. The company worked closely with government agencies like the Bureau of Energy Efficiency (BEE) and the Bureau of Indian Standards (BIS) to revise efficiency standards for ceiling fans. These efforts led to the introduction of mandatory star labeling for ceiling fans in 2019, effectively phasing out inefficient models by 2022. Today, Superfan is a household name, competing with major brands in premium fan retail stores. Its success has inspired other manufacturers to adopt BLDC technology, creating a ripple effect that has transformed the Indian fan industry.
Superfan’s Uniqueness in its Design
At the design and development wing of Superfan, we had the opportunity to speak with Mr. Shakti Vishnu and Mr. Mahendran, who provided insights into the unique aspects of the motor driver and motor used in Superfan’s ceiling fans.
Motor Driver Design
Mr. Shakti Vishnu explained that the hardware developed for Superfan is unique in its design. It has been built using discrete components and Tier 1 parts from reputed manufacturers, ensuring reliability and easy servicing. The motor driver incorporates components such as MOSFETs, microcontrollers, operational amplifiers and diodes from manufacturers like Infineon, NXP, Texas Instruments (TI) and Nexperia. This well-developed and market-proven design has demonstrated reliability over the past 12 to 14 years.
Discussing the motor driver’s functionality, he elaborated that it operates within a power supply range of 140V to 300V and drives a low-voltage motor. It includes a power factor correction (PFC) circuit, which regulates the power factor to unity from the second speed onwards, ensuring efficient power consumption. The motor driver also maintains a low total harmonic distortion (THD), achieving less than 6% at maximum output. These factors contribute to the overall efficiency of the drive system.
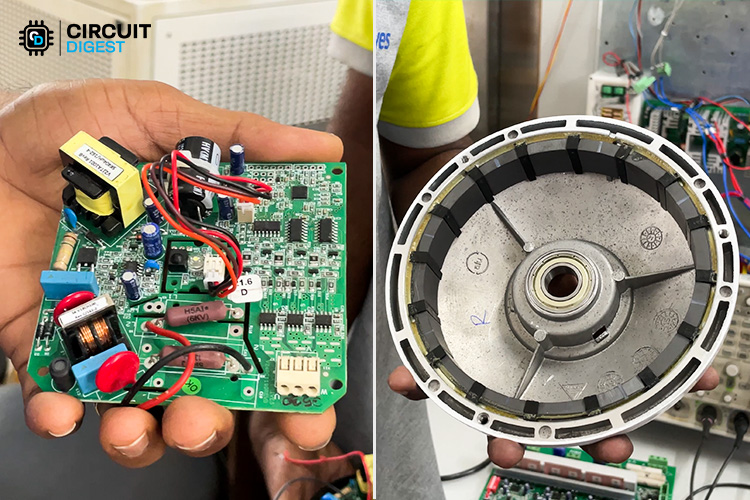
BLDC Rotor Design
Moving on to the motor’s construction, Mr. Mahendran highlighted that Superfan is India's first BLDC ceiling fan, achieving high efficiency due to its brushless DC motor. Unlike conventional AC induction motor-based ceiling fans, which experience energy losses due to induced current in the rotor, the BLDC motor in Superfan eliminates such losses by using a ferrite magnet rotor. This design significantly enhances efficiency.
Beyond efficiency, Superfan’s rotor assembly stands out in its construction. Most BLDC ceiling fans use adhesives to bond the rotor and magnets, which can lead to challenges in the manufacturing process. However, Superfan employs a unique patented method that eliminates adhesives, instead using plastic wedges to secure the magnets in place. The assembly process involves placing the magnets first, followed by inserting the wedges one by one between them, ensuring a precise and firm fit without adhesives. This innovative approach results in a cleaner and more efficient manufacturing process.
While the rotor construction is unique, Mr. Mahendran mentioned that the stator used in Superfan is a standard design without any special modifications. Overall, the combination of a well-engineered motor driver and an innovative rotor assembly sets Superfan apart, enhancing both efficiency and durability.
Marketing Strategy for Superfan
Online Channels
A robust digital presence has been established through an official website and partnerships with major e-commerce platforms such as Amazon and Flipkart. Since its launch in 2012, this online strategy has played a key role in reaching tech-savvy consumers nationwide. The digital channel effectively showcases product features while providing a convenient and accessible shopping experience across India.
Traditional Retail Markets
An extensive dealership network has been built across the country, recognizing that a significant portion of fans are sold through traditional trade channels. This established retail system ensures that Superfan products are available in every region, catering to customers who prefer in-store purchases and personalized service.
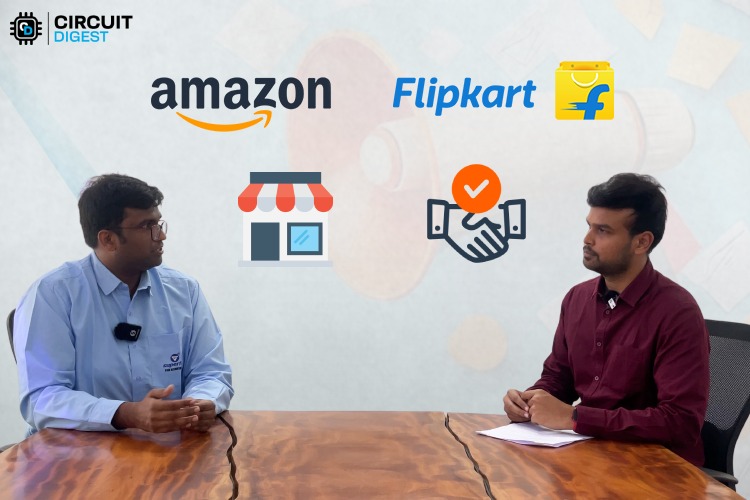
Government Collaboration
Collaboration with government initiatives has helped create a supportive market environment. Such partnerships promote energy-efficient products and build consumer trust, further enhancing market penetration and overall brand recognition in the competitive electronics landscape.
Challenges of Being an Electronics Manufacturer in India
The electronics manufacturing sector in India faces many challenges that must be addressed for growth and success. These challenges include strict regulatory rules, communication hurdles, reliance on imported components, a shortage of domestic semiconductor manufacturing and the need for consumer acceptance.
Regulatory and Certification Hurdles
Manufacturers in India must follow strict safety standards set by agencies such as the Bureau of Indian Standards (BIS). They need to prepare clear and simple documents that explain technical details in a way that regulators can understand. Often, the process requires many rounds of revisions. This means that companies must be patient and work hard to meet all the rules. Changes in staff at regulatory agencies can add to the difficulty because each new person may need the process to be explained again.
Good communication is very important for success. Manufacturers need to listen carefully to what regulators and other stakeholders say. They must change their presentations to match the expectations of the regulators. By building good relationships and trust, manufacturers can explain their ideas clearly. This open dialogue helps everyone understand the goals and improves the chances that new ideas will be accepted. So, these things involved in certification is one of most difficult things as electronics manufacturer from India.
Dependency on Imported Components
A major challenge for the industry is the heavy reliance on parts made in other countries. Although there are many global companies with offices in India, most of the essential components still come from abroad. This reliance creates risks. For example, changes in exchange rates or problems in the supply chain can make these components more expensive or hard to get. Companies must plan carefully to deal with these issues and look for reliable alternatives.
Lack of Domestic Semiconductor Manufacturing
Another big challenge is the shortage of semiconductor production in India. Despite government programs and investments by large companies, India is still far behind in semiconductor manufacturing. Without a strong local semiconductor industry, it becomes harder to build modern electronic products that compete in the global market.
Acceptance from Consumers
Finally, earning the trust of consumers is crucial. Indian consumers are very careful about product safety and quality. If products do not meet their expectations, they may reject them. Therefore, manufacturers need to work hard to show that the manufactured products are safe, reliable and of good quality. Building consumer trust is key to increasing the acceptance of Indian electronics in the market.
Sustainability at the Core of Versa Drives
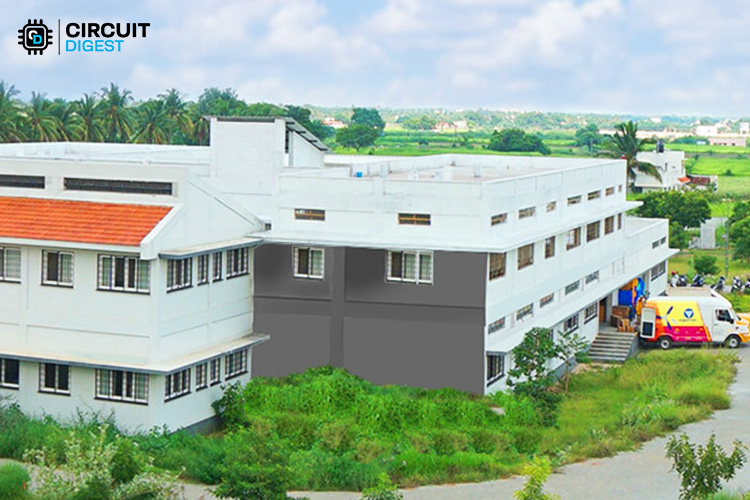
Commitment of Versa Drives to sustainability extends beyond its products. The Superfan factory in Coimbatore is a model of eco-conscious manufacturing. The facility features strategic design elements like high ceilings, atriums and rainwater harvesting systems to minimize energy and water consumption. The factory also avoids synthetic fertilizers and insecticides, maintaining an organic vegetable garden for its employees.
Future Plans of Versa Drives
Versa Drives continues to explore new applications for its motor control technology, extending its expertise to areas such as electric vehicles, drones and solar pump controllers. The company is also collaborating with global firms like Murata and other brands to enhance its technological reach and bring advanced solutions to a broader market.