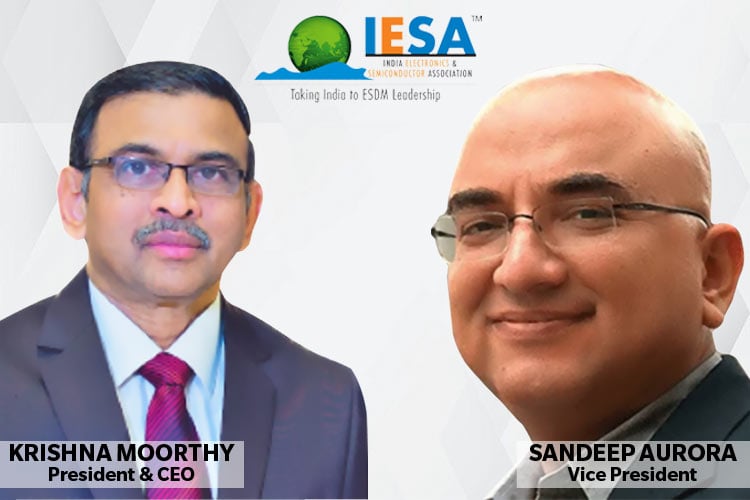
The Indian electronics manufacturing service (EMS) sector, including semiconductor has been moving through various turmoil since the outbreak of the global coronavirus pandemic. For quite a long time, the government of India and industry associations have undertaken several imperative steps to boost electronics and semiconductor manufacturing in the country. But there are still severe challenges that are hindering the growth of the complete manufacturing ecosystem of semiconductor FAB units and other electronic components. In a candid interaction with IESA’s (India Electronics and Semiconductor Association) Sandeep Aurora-VP and K Krishna Moorthy- President & CEO highlighted key challenges of electronics and semiconductor manufacturing, what India needs to do to boost its FAB units and several key criteria of this sector.
Q. Could the US’s anti-China strategy spearheaded by the Trump administration help India to perk-up its own semiconductor FAB units?
K Krishna Moorthy: I would say not an anti-China strategy is what India should start looking at this time, but it must focus on the real India-centric ESDM strategy. India has a huge demand for electronics, we are already doing $150 billion import today, which would be double to $400-500 billion by the end of 2025-26. If we apply this strategy correctly this year, then in the next 9-10 years, we will be able to add as much as 25% of India’s GDP from ESDM. If we are talking of a 5 trillion-dollar economy by 2025-26, we can easily target trillion from ESDM alone. In fact, the PLI scheme is great, but that strategy is not enough. Global companies like Samsung shifting its manufacturing of OLED panels to India is also a huge move.
Q. A month back IESA chairman Mr. Rajeev Khushu stated that India is now targeting 100 fabless semiconductor companies in India? What are your views on this statement and how do you think it could be realty?
K Krishna Moorthy: The big part of the strategy of India becoming an ESDM powerhouse is how do we develop the products, how do we own the design, how do we own the IPs, and that has to happen quickly. It must be noted that we cannot create an IP unless we know how to design it, how to fabricate it, how to assemble it and test it to prove that IP is good to be put in the product. So, fabless semiconductors will be one of the strongest pillars in India’s ESDM strategy in this decade. For example, take the initiative of the SAFAL program of the government of Karnataka. Today, eight fabless companies already working in SAFAL premises. The best country to learn about fabless semiconductors is Israel, which has many fabless semiconductor companies and they are so successful.
Q: As per few studies, the semiconductor industry is still in a state of production catastrophe, especially in the context of the automobile and electronics industry. Can you kindly share some statistics or numbers about the demand-supply mismatch, in the Indian and international context?
K Krishna Moorthy: The whole issue is production had to be stopped due to the Pandemic. But the system level demand has not really dropped. So, people are still buying gadgets and automobiles. In 2020, the worldwide sales of semiconductors increased 6.5 percent approx. So, now if production stops even for a month and even if sales increases, there will be a thrust in manufacturing. So, how this could have been avoided. One is the semiconductor industry must diligently work to ramp up production to renew demands, but the supply-demand imbalance cannot be easily solved by turning on a switch. It is still going to take some time. Even there is a report from the US defense department saying that they are affected immensely in spite of being the most prioritized sector. Big companies like Samsung, TSMC, Intel manufacturing FABs are also extremely concerned, they are trying to increase the capacity as quickly as possible. They are setting up new production lines. Global shortage of chipsets is going to stay for at least one year.
To perk-up the scenario in India, IESA already had multiple meetings with government authorities so that they influence the manufacturers and Indian industry is not badly impacted.
Q: Is India going to fulfill its dream of setting up semiconductor manufacturing firms? How soon it can be achieved because there is a serious crisis in terms of investments and availability of components required for this segment in the country.
K Krishna Moorthy: India will definitely have semiconductor manufacturing companies, but we have to break it down into small pieces because it is not only wafer manufacturing but there are other components of semiconductor manufacturing like assembly, testing, marking, packaging, or what we call ATMP or OSAP. Production of these elements is easy to set up in a period of 1.5 years. Only if we have these things done in the next 1.5 years, then setting up a proper wafer fab will take place in another three years. For example, Cochin and Chennai have started producing system-level products like battery chargers. It has to be done step by step because when the other small components are already available, then only we can have proper wafer fab in the coming three years.
Q: During lockdown 1, there were certain impediments in the electronics industry, but the industries were slowly recovering. During the sudden second wave of COVID -19, the electronics industry again started facing turmoil. In this context, where do you paint the picture of the Indian EMS sector, and what could be the possible solutions?
Sandeep Aurora: The pace of vaccination is picking up. When the second wave hit, we took a lead by working closely with the industry, and fortunately, the good thing is that the industry is able to vaccinate all its employees. The biggest challenge faced by EMS industry is the supply chain disruptions due to pandemic and it is taking a lot of time to get sorted out. Our industry is very cost-conscious, and you want to make sure you are doing everything right. When the disruptions happened, nobody had enough stock to meet the demand. The industry is now working together with large manufacturers, already announced investments into bending manufacturing. A large section of industries globally has realized that they need to hedge and there need to be multiple places of manufacturing, which imply that there must be more than one hub. A lot of global manufacturers are now looking into Indian EMS companies to create this as a second important hub.
Q: How IESA as an association catering to find the solutions to the challenges? Can you highlight some recent policies and initiatives undertaken by your association talks with the government and EMS companies?
Sandeep Aurora: When any problem or issue arises, we as an association start looking at it proactively. We are working very closely with the government and the industry and trying to find solutions to the several challenges caused due to COVID-19. We are also working with multiple companies to see how we allocate a certain state of resources from large companies in India. But the longer-term issue is how do we build a resilient supply chain where India does not suffer like this again. Another important thing is how do we place India in the middle of the supply chain in the electronics segment. We are doing a very deep study on what all supply chains of the electronics and semiconductor industry comprises of and what all elements of supply chains are there where India can participate.
Q. What will be your upcoming roadmap in the coming few months to boost the electronics sector in India?
Sandeep Aurora: If you look at the complete ecosystem of the electronics industry you have the active semiconductors and passive components in tripping blocks. Then there are some very big components like SoC or processors, which also get added with other components to make a system. So, our clear strategy on the roadmap is capturing the data on whatever the components we have imported, what is the value of that, and which industry has been utilizing it. Another roadmap is to help companies build up a 100 percent manufacturing of electronic end products and components.