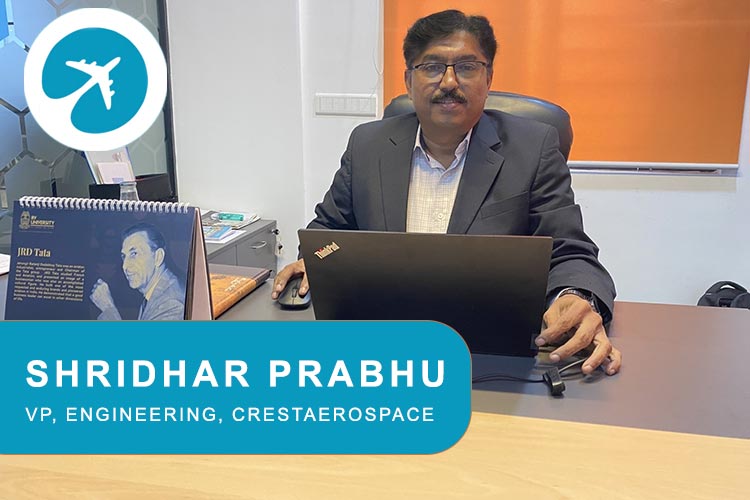
Over the past few years, India has escalated its in-house production of electronic products, but in spite of that growth, import of these items, mostly components, continued at the same volume. The picture shows that there are various impediments in the sector, which still needs to be addressed like the companies must manufacture finished goods in large quantities and at competitive prices. Also, there is a lack of investments in producing ICs, irregular power supply, supply chain disruptions, and many more. Moreover, import of electronic items has turned out to be the nation’s second largest contributor to Current Account Deficit (CAD). In this regard, we spoke to Electronic Manufacturing Service (EMS) expert Shridhar Prabhu, VP, Engineering, CRESTAEROSPACE who highlighted in detail about the current growth and progress of EMS sector in India, how the country can become globally competitive in the coming years, and how government initiatives and schemes can boost the growth.
Q. What are your views on the current growth and progress of the EMS sector in India? Can you elucidate where India currently stands in EMS when compared to countries like China, Vietnam, Japan, Europe and the US?
The EMS sector is one of the most rapidly growing sectors in India and its market share in the global electronics manufacturing industry has increased from 1.3% to 3.6% in 8 years by 2020. India is aiming to achieve US$ 300 billion worth of electronics manufacturing by 2026, out of which the ambition is to achieve US$ 120 billion worth of exports by 2026. The high growth trajectory is because of the availability of skilled labor, raising domestic demand, raising income and low-cost labor & favorable government policies.
With the government's implementation of National Policy for Electronics, with successful application to benefit from the PLI scheme, due to the rapid economic growth, India has emerged as the 2nd largest mobile phone manufacturer within 1 year with a 126% jump in production in 2022. Out of these exports reaching a noteworthy milestone of $11 billion USD is a significant achievement.
China has dominated the Asian manufacturing market for over four decades & will remain the dominant player. Things started changing because of reasons like geopolitical issues, increased cost of labor, de-risking the over dependency. Even Chinese firms are moving supply chains out of the country. For sure India has benefited because of this shift, so does nearby Southeast Asia countries such as Vietnam, Thailand, Malaysia, and Indonesia. Vietnam has the geographical advantage of proximity to China along with low labor cost has attracted significant investments. Japan, Europe & US has Strong, well established and Technologically advanced EMS Industry, specialized in High value products with precession and advanced manufacturing technologies.
While India has made tremendous progress, it still has some catching up to do in terms of scale, technology, and capabilities as compared to Giants. The present success in Smartphone manufacturing will have to be replicated in other products as well like consumer electronics, IT Hardware & telecom products by diversifying manufacturing capabilities.
Q. Which are the various sectors you have worked over the years and how is your journey as an engineer so far? Kindly highlight some of the EMS based solutions, products and services you have worked and what is the response so far?
Soon after my post graduation, I started with Tool Design in a commercial tool room in Singapore, in 1996. My EMS journey started back in 1999 with Flextronics in Singapore where I used to manage the tooling (Plastic Injection molding and stamping) in Southeast Asia. When the value added from EMS was expected from the OEMs, I moved into R&D & started my career in the product design field. There was a lot of scope for new product design as well as upgrading existing products which were either going through end of life or new feature/functionality addition. Some products need to comply with new regulatory requirements, some need standardization because of interoperability, and commonization (especially when competing products within the same organization because of acquisitions).
That was a time when there were cost pressures on electronics manufacturing & reducing margins. China was giving tough competition in electronics manufacturing. The companies started moving to places like Malaysia and China because of cost arbitrage. The high value add manufacturing continued in Singapore & some because of FTA with US. The ODM design was maturing at the point in time, The NPI (the bridge between Manufacturing & Design) was emerging & gaining significance in ensuring smooth transition into production. That’s when I moved into Venture Corporation supporting printer, plotter, scanner manufacturing for customers like HP. We had a couple of manufacturing lines transferred from Europe to Singapore.
I moved back to India in 2007 & joined Wipro’s Product Engineering Group. Managed teams in Product design of thermal printers, telecom routers, switches, telematic products, health care products etc. Went on to build electronics & software business unit at Creative where we managed dedicated ODC for Transportation customers who were into LED signages, Video surveillance, entertainment systems which goes into Rail and Road transport. Now I am with Crestaerospace managing Embedded SW development.
Q. As a VP of engineering, what is your advice to the younger generation who are developing electronic products in India and which are the key areas they must focus? Youth these days are more into software, and therefore how we can influence them to work in hardware engineering?
The younger generation has great exposure to the knowledge, focus needs to be on the application of it into products. We need to encourage building hands-on electronics projects & we should build the ecosystem for the same with Industry academia collaboration. This not just builds the practical exposure, but also makes industry ready engineers.
There needs to be a lot more emphasis at system level approach to any product design & manufacturing. The collaboration & networking is the key in coming out with smart, intelligent, futuristic products.
Encouraging internships in HW design organizations and EMS companies is one way to induce interest to take up HW engineering. The exposure and industry trends help them look for challenges and gives them the opportunity to think of problem solving based on their learning. Strong fundamentals are very important to build a strong foundation. Once you have capabilities to expand your career in the adjacencies like design, manufacturing, sales, NPI, Project Management, Vendor Development, Quality will be easier if one is able to relate and apply the technical competencies.
Being flexible, upskilling and adapting are few traits for success in the present day especially when technology is changing rapidly. There is no shortcut to success & there is no replacement to hard work. To scale the EMS further in India the next focus is going to be more on Value add to OEMs by having inhouse design facilities & advanced manufacturing techniques. There are going to be a lot more opportunities in board design, Power System design, Sensor integration, Value Engineering, Debug & repair which would need good system level knowledge.
Q. Electronics manufacturing and EMS are growing tremendously over the years in India owing to various schemes and initiatives by the government. In this regard, can you highlight any additional challenges and which are the areas the government should currently focus on?
I can see there is clear vision, intent & sense of urgency in enabling the kind of growth in EMS.
Government has permitted 100% FDI in the consumer electronics manufacturing segment through the direct route and offered capital expenditure subsidy under the Modified Special Incentive Package Scheme (M-SIPS).
Here are some of the areas needs further support:
- Develop Domestic Component ecosystem – as most of high value components are imported presently.
- Strengthening the domestic supply chain for electronic components and raw materials which can reduce import dependence.
- Reliable and efficient Infrastructure & Logistics.
- Further ease the complex regulatory procedures.
- Skilling the workforce to fulfill future needs to address massive scale.
- Process engineering specialization - Lack of such degrees in the field of electronics or microelectronics. Same applies to the semiconductor industry which goes hand in hand with the EMS especially the OSAT.
- Incentives for companies to conduct research and develop new products & commercialisation of cutting-edge technologies.
Now that there is proven competency in electronics assembly (seen in the smartphone manufacturing), this will have to be replicated in other products like Consumer Electronics and IT Hardware. The other capabilities of EMS like Design and Engineering Services, Test Development & Implementation and Logistic services are yet to mature & scale in India. We still have many specimens in PCBA, Subassembly, Box build EMS while we must start scaling full solution EMS where customer/OEM does not have to deal with multiple Vendors.
Q. What is your current role in CRESTAEROSPACE and which solutions are currently working on? Can you speculate its traction in the industry?
At Crestaerospace we always were very focussed on building niche skill sets in Embedded Software development space & build the in-depth capability working with Global customers for their success. In the last 7 years we have built Embedded SW for Control system for Cockpit Door locking, the Cabin Management System, Gally inserts for Avionics as well as Wastewater management Systems and Next Gen Lavatory management systems for Rails. We have also developed Test Automation for our customer where the time for the Validation cycle has reduced considerably. We work not just on new product development & also work on POCs for futuristic products like Centralised power control as well as Inflight IoT system for entire aircraft for data collection of seating comfort, passenger preference data for enhanced & customized unique experiences for individuals. We work with Innovation and Advanced Technology teams of our customers to commercialize futuristic technologies to their end customers.
Q. Going forward, where do you want to see India in terms of growth in EMS and engineering? Any specific solution you wish to highlight in the coming years?
With the present aspiration of India becoming the 3rd largest Economy by 2028, we must be a global leader in the EMS and engineering sectors by then. India has seen a service led economy & we have a great talent pool from Engineering Services perspective. There has been focus on Manufacturing in the last decade & by 2018 there were 120 mobile phones and components manufacturing units out of which 59 were with complete box build capabilities. The manufacturing capability will have to be expanded into advanced manufacturing capability and it must start scaling by capacity building. The supplier ecosystem for PCBA & subassemblies around the EMS must grow as self-sufficient independent clusters to better manage the supply chain & logistics. To support the scale the validation, compliance & certification labs need to be built to cater for the growing needs.
Here are some other areas of Focus for achieving exponential growth:
- Establish local component ecosystems, increased emphasis on R&D capabilities, availability of skilled workforce to manage the scale of growth, better industry academia collaboration & support Startup & MSME.
- With the introduction of advanced automation solutions and the rise of Industry 4.0 adoption, the electronics manufacturing services market is projected to experience continual innovations in manufacturing processes and technology. Digitisation will further optimize the manufacturing process, increase efficiency & enable data driven decisions.