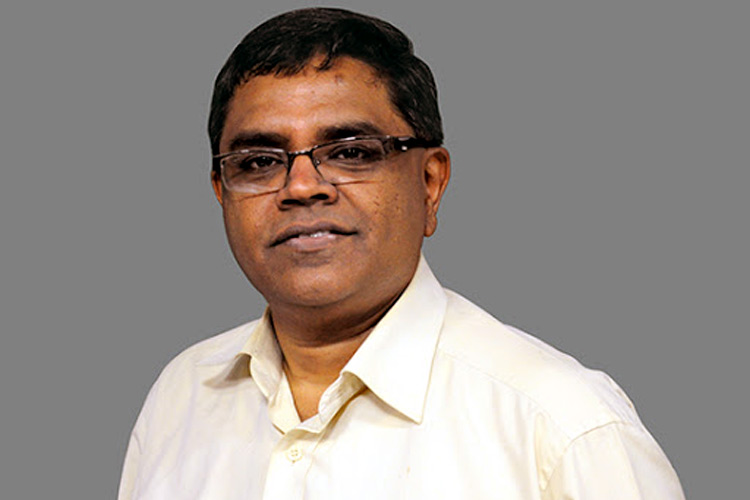
According to the UN, by 2050, almost 2.5 billion people will be the part of urban population and we all know that the current housing and transportation infrastructure is inadequate and is not going to help meet the needs of the rising number of people. To do so, we need to expand our cities speedily and economically. Besides, to combat the transportation issue, there is a need to divert our focus to urban aerial mobility that will help cities grow laterally.
Who knows, in days to come, we find ourselves waking up amidst green trees and chirps, tens of miles away from the dense city centers. The future has a lot in store for us. Besides, breakfast, groceries, etc. being drone-delivered, you will be able to fly to work and will not get stuck in a traffic jam.
The Chennai based startup named ePlane is pioneering in aerial mobility. With Ek Hanz, a fully autonomous compact electric aerial vehicle that can take off from anywhere and can be used to deliver items, the company is sure to bring a revolution in aerial mobility.
Mr. Satyanarayanan Chakravarthy, the co-founder of the ePlane company, shared with us the details of the startup, the team, future goals, and much more. Mr. Chakravarthy is a professor of Aerospace Engineering at the Indian Institute of Technology Madras and specializes in the propulsion of aircraft and rockets. He holds a Bachelor’s degree in Aerospace Engineering from IIT Madras and Master of Science in Aerospace Engineering degree (1992) and Doctor of Philosophy (1995) from the Georgia Institute of Technology, Atlanta, GA, USA.
Not just that, he has been a passionate teacher for over a couple of decades at IIT Madras and a researcher on combustion, laser diagnostics, etc. He persevered to establish a large center for combustion R&D center, NCCRD, at IIT Madras, before turning his attention to electric aircraft propulsion lately. He is passionate about working with industry in solving real-world problems and in developing products for societal impact. Read on to know what he has to say about ePlane, Ek Hanz, and more.
Q. ePlane is working on Autonomous Hybrid Electric Aerial Vehicles, how did it all start, and what are your plans?
A lot of rapid changes are happening around us in the energy and mobility spaces. Thermal power is fast being replaced by renewables, and electric vehicles are fast replacing combustion vehicles.
As an aerospace engineer by basic training and with propulsion as my specialization, I asked myself, if I am not going to look at electric propulsion for aircraft at this point in time, what else would I do! Let go of the past, no matter how glorious it has been and embraces the future, no matter how uncertain it is, is the mantra. This is the motivation that led to my founding the ePlane Company. Not only that, in fact, in the past year, I am the first to my knowledge to offer a full-fledged semester-long course on Electric Aircraft Propulsion, twice over the two semesters, and I have got the lecturers video-recorded the second time, to be uploaded on YouTube after the edits!
ePlane’s quest is in enabling rapid mobility of people over short and intermediate distances within and around cities in the future by means of electric aviation. We have our eyes set on making a two-seater autonomous VTOL electric plane for intra-city air-taxi services. In my view, this is reasonably possible mainly with hybrid aerial vehicles – hybrid not as in propulsion by combustion and electric, but in the sense of a combination of VTOL with fixed wings, i.e. take off like a drone but fly forward like a plane! It would have to be fully electric to keep it simple and relatively inexpensive if we are to populate the skies with air-taxis for people’s daily commutes.
Q. Tell us how ePlane initially got off the ground? How did NCCRD and IITM help?
ePlane got off the ground first in our minds! All these crucial decisions – why should it be all-electric, why not hybrid propulsion between electric and combustion engine, is it just a fad or a fetish to go all-electric to look ironical coming from a leading combustion expert or does it really make techno-economic sense (that’s a lot of soul-searching!), why does it have to be a VTOL, why does it have to be a VTOL-fixed wing hybrid, why a two-seater, why autonomous, what would be an appropriate price point for the Indian market, etc. Each of these had to be ideated and debated, and genuine answers had to be evolved for ourselves, instead of just looking at what others are doing. Because we are acutely conscious of the Indian market and the urban mobility situation we are in.
India is particularly in a sweet spot for embracing eVTOLs for urban air mobility (UAM) unlike China, which in my opinion seems to have peaked slightly too early ahead of the mobility transformations, we are witnessing today and has gone ahead with massive infrastructure investments that could be obviated with the new tech! I have coined a term for “defrastructure”! The situation with advanced nations is similar, with all the highways and flyovers already in place, their mobility pain point per person is not as painful as in India. For India today, UAM seems to be a “must-have”, not a “nice to have”, unlike other places. And, yet being an extremely cost-sensitive market, we need to put the best out there, so a lot about the ePlane is in configuring it just right.
NCCRD has fast developed into a cauldron of ultra-deep tech startups and projects, many of which I am proudly the part of, such as Agnikul, Aerostrovilos, X2fuels, Tan90, hyperloop, space gun, etc. which synergistically energizes ePlane with its space and facilities. We are incubated at the IITM Incubation Cell, which opens up a lot of exposure to the external stakeholders and business and technical mentors. IITM itself is a beehive of an entrepreneurship ecosystem, with the CFI, Nirmaan, E-Cell, GDC, etc., besides NCCRD.
Q. Ek-Hanz is the company’s first Hybrid Aerial Vehicle. What are the technical specifications and features of this AAV?
The Ek-Hanz is part of a three-stage vehicle development process comprising Ek-Hanz, Do-Hanz, and the ePlane, the last of which is our ultimate goal for the next few years, to carry people across city skies. The approach is to develop tech that could be tested at smaller scales, which could themselves find commercial use cases. The Ek-Hanz is a small HAV capable of lifting up to 6 kg, but could go as far as 100 km with a 2 kg payload in a single charge of the battery pack. It falls under the “small” category of UAVs and its flight altitude is restricted to 120 m by civil aviation regulations. It is fully autonomous in the sense, it can navigate itself with waypoints as well as to detect and avoid obstacles along its course.
Q. There are many heavy-lifting electric autonomous aerial vehicles, how is your product Ek-Hanz different from those?
The Ek-Hanz has been configured to address the holy grail of HAVs, namely, the vertical rotors meant for VTOL is a deadweight during forward flight while the wing meant to produce aerodynamic lift during forward flight is a deadweight during VTOL. The Ek-Hanz is not a mere slap of a multi-copter on to a fixed-wing plane but attempts to combine them into an aerodynamic configuration where the rotors would aid the wing in additional lift generation synergistically, and the wing would aid the rotors during the climb and descent phases. These two aspects enable an extended range for the Ek-Hanz when compared to a simple juxtaposition of the vertical rotors and the wings together.
Q. Being a complete Autonomous Aerial Vehicle, how does Ek Hanz map the real world? What sensors and hardware drives your vehicle?
We need to understand that the Ek-Hanz is more challenging for sensors to be mounted when compared to bigger aircraft because of stringent weight restrictions and the small real estate available. As such, we are having a combination of several 1D lidars pointing at different directions as proximity sensors to estimate the distance from any obstacle as well as cameras to decipher the form factor of the obstacle. The form factor information of the obstacle is fused with the distance estimates and translated into point clouds that the controls should get the aircraft to fly around. A combination of long-range low-frequency lidars and short-range high-frequency ones are used for dynamic obstacle avoidance as well as to avoid static obstacles. Other alternatives such as 2D lidars and stereoscopic cameras are either too heavy or of poorer range/resolution for the speeds involved and the response times required, but this is an emerging area, so we are open to improving our autonomous flight package by reconfiguring it as specs of the components improve.
Q. The Drone is said to be using machine learning algorithms for autonomous flight, how does that work and how close are we to complete autonomous flights?
Machine learning depends on the availability of learning datasets. While we have developed simulations of waypoint navigation with obstacle avoidance in a typical flight environment, these are insufficient for evolving ML to be deployed in realistic flights. We are in the process of flight tests, and gathering a lot of flight data to develop learning datasets. The ML can then be adopted in the simulation environments first before getting on to a flight system. It is yet to be seen if certification standards can be evolved for this purpose, so it will take time through the year or later to develop a sense of its complete adoption. One specific aspect that could find acceptance is a computer vision-based landing tightly at a particular spot with marks like they have for helipads. Machine learning is not mandatory for autonomous flights per se, including obstacle avoidance, but it would be a ‘good to have’ feature, so the two should not be mixed up with each other.
Q. Ek Hanz uses a patented energy-efficient design, to attain long-distance flight with a heavy payload. Tell us more about the design.
The energy-efficient design is based on viewing the fixed-wing and the vertical rotors as a single entity in an aerodynamic environment instead of a mere juxtaposition of the two with their independent flow fields. So, the question of how the flow field over one affects that over the other has been taken into consideration in order to augment the lift produced and decrease the drag incurred by the combination when compared to the two units acting independently. Fundamentally, most other drones do not operate the vertical rotors during a forward flight in order to save on energy consumption, but an optimum level of their operation leads to further energy savings! The rotors can then be used for additional control against gusts and finer adjustments, which offers redundancy in controls as well.
Q. Your company was among the top 10 finalists in Qualcomm Design, India Challenge. Please share your experiences.
The Qualcomm outing has been a big boost to eplane as a validation. Plus, we have had the opportunity to explore their flight stack, smart-cams, and other products for our use. We have developed a combination of hardware and written software to integrate those, which could lead to patents being filed. The QDIC journey has been exciting, with workshops conducted by them at different locations for the cohort we are part of. We also look forward to the opportunity with investors that Qualcomm itself would open up for us. Their launch of the cohort at the Startup India office in the august presence of the Secretary of Ministry of Electronics and Information Technology provided very good visibility to us. Qualcomm engineers and managers of the Design Innovation Challenge program have been very pleasant to work with. It is definitely one program, I would encourage a lot of deep tech hardware startups to consider looking towards.
Q. How do you see the market for AAV in India? What do you think are the potential applications of Ek Hanz?
As India is fast developing, there is rampant urbanization. With infrastructure development being hard to keep pace with this trend, people clamour to stay clustered to where amenities are concentrated, so it results in huge traffic congestion. Consequently, people want to stay at home and let things get to them by ordering online. The food delivery business alone has been growing 300% in the last few years! This is unparalleled anywhere. This is where the Ek Hanz will be the most useful. The retail e-commerce business does not require AAVs for last-mile delivery but could witness use for mid-mile, i.e. from godowns to fulfillment centers. For this, a larger payload-capable AAV, namely, our Do Hanz, the next bigger vehicle would be very much appropriate. Lastly, although goods movement is a bigger market than people's movement, it’s people who really matter, so our ultimate goal would be the ePlane that enables urban air mobility by means of air taxis. And, needless to say, it could transport large cargo across the city for logistics companies too. I foresee that the long-range, we are typically focusing on for our aerial vehicles would ultimately enable decongesting cities and spread services to be available easily in far-flung areas beyond the urban sprawl. The market size for all of this can be obtained easily in terms of billions of dollars from reports of consulting firms and other studies, but it is the above philosophy of how to view these trends and enable their reversal through our tech that’s exciting!
Q. What problems did you and your team face during the initial prototyping of Ek Hanz?
Design for manufacture and interfacing with the manufacturers took more time than anticipated. Controls for a twin-wing configuration in combination with the quad-rotors were not obvious at first and, sensor development for obstacle avoidance for such long-distance and the fast-moving vehicle was a challenge. The no-permission no-takeoff (NPNT) protocol mandated by the Indian regulatory authority, namely, the Directorate General of Civil Aviation is another facet we had to develop along the way, both in terms of hardware and software implementation. In fact, we are still developing mobile network-based long-distance communications for remote piloting (for manual intervention) and video feed to ground station for live feedback on the flight during its course, as an alternative or a redundant measure.
Q. Being one among the few AAV companies in India, how did you source components for your vehicle? Did you face difficulties?
Our AAV is an amalgam of a multi-copter drone and a fixed-wing plane. The drone parts of it can be sourced through a reasonably well-established vendor base. In fact, the design is based on what is readily available. The plane part of it had to be manufactured by us. We have partnered with specialists in carbon fiber manufacturing as well as the attempted combination of plastic 3D-printed non-load bearing structural elements with carbon fiber sheets, tubes, and pre-pregs. We have 3D printers in-house for these trials. The IIT Madras technological support base and entrepreneurial ecosystem of startups come in handy to try out different options for the first time on a configuration such as ours.
Q. At the moment, how do you measure success? What are your metrics?
Timing is the key to the success of startups! We are at the cusp of easing of regulations of unmanned autonomous aerial vehicles and are glad to be a part of pushing those boundaries. Through this process, the outlook is bright on customer identification and acquisition, partnering in demonstrating user flights to regulatory bodies, and in carrying out commercial pilots. While there, deepening our focus on developing subsystems such as motors, customizing battery packs, flight controllers, communications, sensors, computer vision algorithms, etc. and graduating to ducted fans for the next bigger level AAVs is all part of a fascinating journey that we have embarked upon. These expanding opportunities improve our value proposition to investors, which is a direct metric of our success at this stage.