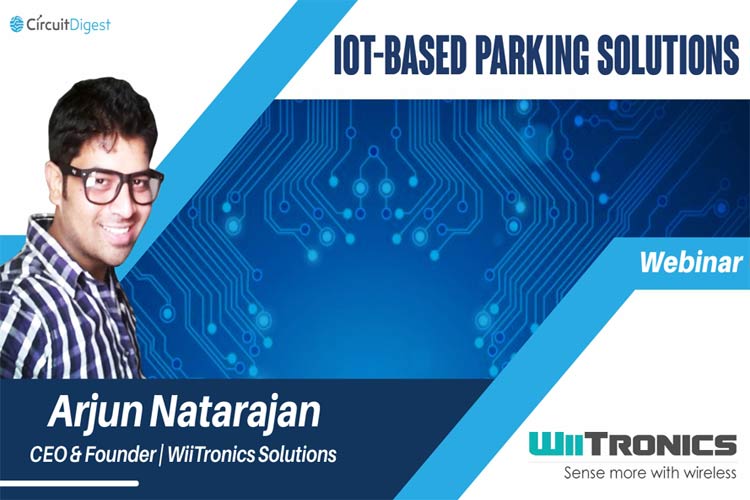
Due to the rapid increase in the number of vehicles on the road, traffic and parking problems are bound to exist. The reason being, the inability of current transportation infrastructure and parking system to cope up with the increasing number of vehicles on the road. Factors like office occupancy, employment, car ownership, travel, and discretionary spending are impacting the way parking facility is used. The smart cities of today have every facility but alleviating the parking issue remained unaddressed for long.
Concern over the lack of sufficient parking has increased to a great extent. Understanding the criticality of the situation and need of the hour, Arjun, a hardware engineer, and Siva a software veteran came up with the idea of starting a venture aiming to provide IoT-based parking solutions through their company WiiTronics. Keen to know more about the company, we asked Arjun (who is the CEO and the founder of the company) for one on one interaction with him and here we are ready to get the ball rolling. So, let’s start with the article to get insight into the products that WiiTronics is offering and how are those proving beneficial in terms of proper parking management.
Q. Tell us about your company WiiTonics. What kind of parking management solutions do you provide?
WiiTronics is an IIT Madras incubated company that was started back in 2013 to develop hardware and software platforms specifically with IoT in our minds. I am a hardware engineer from Silicon Valley and my partner Siva is a software veteran. He was working in Wipro previously in India and then he went to Singapore for further studies. There he was working for a company that was owned by the Singapore government in the R & D side. So I invited him to come and join me after I started WiiTronics.
We build IoT products. We have a hardware platform, WiiTronics hardware platform, which in simple words means wireless electronics. Our software platform is called Random Mouse. We have designed sensors that can detect vehicles, so we use it with our hardware platform. With this, all the communication from the customer/client side to our cloud server can be facilitated. The platform can be used to have any other sensor as well, other than vehicle detection sensors. Our goal is to take all the products that we are designing and all the solutions that we have and go global with it and that’s our focus for the next three years.
Q. Please explain the basic architecture of your IoT Parking solution system and how they work.
We have different types of parking sensors that are installed in each slot of the parking lot. For indoors, we have specific sensors, for outdoor parking like on-street parking, we have specific sensors. The indoor sensors are all ultrasonic sensors that detect if a vehicle parking is available or not. They then communicate with the sensor controller. To reduce the cost, we put a transceiver on the central controller from where it is wired to all the sensors. These sensor controllers detect the status of each slot and send the data wirelessly to our gateway which is a Linux-based computer connected to the internet and we have a huge application running on it. It's the brain or the CPU of the entire solution.
The status updates from individual plots are sent to the gateway that puts it on the cloud and also updates the displays. The display is extremely crucial for our application where for each driveway in a parking lot, be it indoor or outdoor; we'll have a display that says how much parking is available in either direction that they go. So if the sensor changes the status, the gateway knows which all displays need to be updated. In case, there's a driveway leading up to say, five different driveways, and if there is a sensor at the end, where a car leaves, for example, all the displays leading up to that driveway, and to that sensor gets updated. So it's cumulative! That’s what we do with the IoT sensors, we take it to cloud.
WiiTronics stand out of the crowd for the fact that in other companies, the display participation for a particular driveway is confined to the sensors. So, if there are a hundred slots and hundred sensors, the display is wired to those sensors and it shows the availability for those hundred slots. But because of IoT, we can provide cumulative data on each of the displays.
Q. Why did you make that conversion from ultrasonic to the Magnetometer sensor? Do all the sensor nodes have an ultrasonic sensor or the magnetometer ones or is it a combination of both?
It entirely depends on what kind of parking that we are looking at. For indoor applications, the parking lot owner is very touchy about installing sensors on the floor, because they have an epoxy coating on the floor and they get warranty for the epoxy coating. And you can't touch the floor. That's one of the reasons why we wanted to come up with a sensor that can be put on the ceiling. It can detect if the slot is available and there is no intrusion on the structure on the flooring.
As far as the magnetometer sensor is concerned, we specifically designed it for outdoor applications. It is battery powered; you can't really cut the road and bring power wires inside, there's a lot of civil work involved. That's why we just designed a cup, which is cylindrical. You just dig and then you fix in that and it's battery-powered, so it's less intrusive on the road. The magnetometer is not a replacement for ultrasonic but we use ultrasonic for all our applications. We found ultrasonic to be quite reliable and it is working so well that now we are taking ultrasonic to the outdoor application as well, where we are having a small post on the side of the car. Even outdoors, we will put our LCDs showing availability.
Q. You have used ZigBee for the communication between your gateway and your hub. Why? Why not other protocols like LoRa? Also, are you planning to move into using other protocols in the future?
One of the main reasons for choosing ZigBee is primarily because of how parking lots are designed in India and globally. Parking lots have got several pillars which are of steel-reinforced concrete and all the cars are made of metals. There is a huge attenuation. If we have the gateway installed somewhere, chances are that we are not going to get a line of sight. That's why we wanted to use a multi-hop protocol where even if the gateway is somewhere around the corner, and there are lift lobbies and escalator lobbies in between, the data that we are sending can hop onto other transceivers and get to the gateway. Wireless is the line of sight so we can bring data from basement three of a parking lot to outside about 50 meters away from the parking lot to a display. So that's what ZigBee brings on the table, it's able to hop and get to a destination which is something that Lora cannot do. We wanted mesh protocol and a multi-hop protocol.
Q. How does your revenue model work? Is it like just a onetime installation fee or is it like Software as a service kind of thing?
It's a combination, the software is provided as a subscription for the malls, or the airport or wherever, whoever is the operator, and the hardware is sold. They make a Capex investment and buy the hardware and install it.
Q. How do the Magnetometer-based sensors work? How good is it for the vehicle sensing applications?
Magnetometer based sensor is a magnetically sensitive material that's installed on the road as a bridge network. So whenever there is a change in the magnetic field, there is a change in resistance too. And that's captured as the change in voltage across the bridge. This is amplified and brought out. It’s like we are reading registers to understand the change in the magnetic field in the relevant axis. Once that is done, we write our algorithm and we do a small statistical calculation to ensure that it's a vehicle that's on top of the sensor. The magnetic flux density changes because the chassis on the vehicle is made of metal and it's extremely heavy and it has an impact on the magnetic field surrounding the sensor. That's how it detects a slot if a car is parked on top of the sensor or not. So this is probably the most challenging of the products that we've developed so far.
Q. How are these magnetic sensors installed on the road? What kind of maintenance is required after installation?
The magnetic sensors are installed by core cutting, core drill is done on the road, we remove the cylindrical tar out, and then our enclosure is put in it. There is an insulating material that goes all around our sensor so that the surface temperature from the road does not directly come in contact with the sensor enclosure. Even though they're all plastics and they're all insulated, we try to minimize that effect. There are two enclosure designs for various reasons. One reason is that the hardware shouldn’t directly come in contact with the enclosure that is in contact with a tar road and temperature should not come in contact with the hardware. The second reason is that the application is battery-powered. So for changing the battery, there is no need to remove the entire enclosure out and change it, the enclosure top is removed and replaced with the other one enclosure by just removing the top.
The thing is that which is slightly tricky is when you're installing the sensor to make sure that there's no metal component around. Otherwise, the sensors are pre-calibrated for that piece of metal. Also, while designing the sensor, you should make sure you understand that the sensors behave differently at different temperatures. We need to do a proper temperature calibration before we deploy sensors.
The way the hardware is designed is that it's always in sleep mode and we've gone through different iterations of the design. Initially, we used to have two sensors. So one sort of inaccurate sensors that can detect some kind of obstruction on top and then we would turn on the magnetometer-based sensors to figure out the slot is available or not. Later, we moved on to a chip which in a low power state would give us an interrupt when there is a change in the magnetic field. That's how we were able to achieve this so the entire circuit was in sleep mode. Whenever there is a change in the magnetic field, we'll get an interrupt and the circuit wakes up, and then we do our calculations to see if there is in fact, a vehicle or not. So based on usage, we could go somewhere between two to four years of battery life. We use a lithium-ion battery and we use a controller that had a drain current of 40-50 nanoamps.
Q. Do you manufacture these sensors completely in India? You're a few, one among the few companies who are into this IoT parking solution, what kind of technical difficulties you faced when you developed the product like this?
Yes, we do manufacture these sensors completely in India. We faced a lot of challenges. While designing the magneto-based sensors, we found out that the sensor output varied with temperature. That’s why we went to great lengths to insulate it from the surface of the road because the surface of the road can go up to say 65-70 degrees Celsius, you've seen in some places that the tar melts on the surface of the road. Our hardware basically can handle that temperature but only thing is that the sensor output varies with temperature. So if you design the sensor and put on the road, at seven o'clock in the morning, your sensors are showing some value, at one o'clock in the afternoon, they show different values. So for each sensor, we had to do temperature calibration, because we were designing these products for the global market viz. Edmonton in Canada, where you have minus 40 degrees Celsius during peak winter, to places like Dubai, where you have 55-60 degrees Celsius where the surface of the road will probably be higher. So that's one of the biggest challenges we had to figure out what is the process that we bring in to make sure we do temperature calibration, and the sensor works reliably after that.
The second aspect is that we had to sort of go beyond our knowledge in electronics because these sensors are installed on the road. A 16-wheeler truck can decide to park on the side of the road and go have tea. So we have to design the enclosure in a way that it can handle heavyweight of that container if they went on top of the sensor. So we designed it and got it certified, I had to take a load of about seven tonnes. So that's about, 2-3 tons more than what a single wheel would handle in a big truck.
As there were not many competitors, it was the journey we had to take up alone but we had a lot of people to help us that's where IIT Madras incubation cell came in, we have several advisors, both on the technology engineering side, and we got a lot of help and lot of it was trial and error. That's why developing hardware and getting it to the commercial market takes considerable time to achieve that.
Q. As a manufacturer in India, how do you manage your supply chain?
Several distributors in India take the headache off your shoulder. You just give them the BoQ, and they handle everything; all the logistics, everything involved with this, and we work with multiple distributors and our PCB assembly processes are outsourced and so we introduce our distributors to the PCB assembly people and they have their setup distributors as well so that we can see the cost-benefit. I've never faced any sort of issue in terms of getting a component or getting a product out on time. As far as designing our hardware is concerned, designing PCBs and doing the assembly, it's not at all hard, and especially in India, I don't think it's a challenge at all.
Q. Tell us about your computer vision-based vehicle detection, this is a completely alternate way of providing a parking solution. Why did you opt for this?
The third product we are working on currently is computer vision-based vehicle detection and using the same tracking is also done. We have our cameras talking to an edge box. The detection takes place is at the edge level. We don’t have to take the image of the parking and send it to the cloud and have a process. So all the processing happens at edge level which is a requirement in India because we don't have the kind of bandwidth we require to handle so many images and big processes. Only the information whether a slot is available or a slot is occupied is then sent to the cloud. We take up an existing model that is there and do transfer learning. So that this application that model can be reliably applied for our application, which is the detection of the vehicles.
In this method, we are not drilling holes on the road. So, it's not very intrusive on the surface. Apart from the fact that we are detecting if a slot is available or not, there is a huge camera infrastructure already on roads that are used for surveillance purposes. So, we can repurpose some of the cameras that are already installed. By doing that, we can bring down the cost for the customer. Besides, we can add certain features like for example, we can add algorithms to detect the vehicle’s number plate, which means that if a specific slot is a result by a specific user with a certain license plate number comes in and parks, we can validate if he is a right user or not. All this is kind of difficult to achieve with only sensors. Developing this is somewhat driven by what our competitors are offering as well. A lot of our competitors are offering computer vision-based technology solutions. We are also able to do that with additional peripheral services that would help enhance the experience for the user and the operator.
Q. How safe we can bet on the reliability of computer vision technology like when it rains or when the sun goes down? How practical are these solutions?
There have been challenges in computer vision-based technology. We are doing several rounds of tests to figure out as to what can be done to improve accuracy if we need more sensors apart from the cameras or do we have multiple combinations. The most accurate form of sensing along with that complements computer vision as millimeter-wave radar sensors which we are exploring now; we have just started doing that. The advantage of having two sensors is that you know, our accuracy reaches very close to a hundred percent when it comes to detection of vehicle and radar can work through all kinds of weather conditions. Millimeter radar is something that's picking up slowly especially without self-driving cars that are coming up. They use millimeter radar and we are looking at it as add on for computer vision technology.
Q. Has WiiTronics installed any of these computer vision technologies anywhere? How has been the performance?
We have done that in a mall in Chennai, we've deployed computer vision-based cameras, and we do number plate recognition, and we've integrated it as part of the billing system. Whenever a vehicle comes in, we pick up the number plate and we get a confidence factor from this. When it's quite high, we just open the barrier, we don't ask the vehicle to stand and get a ticket or anything. Similarly, at the exit when they come, the number plate is captured and we just tell them how much they have to pay.
The accuracy, the NPR is not as high as it should be. But we are getting reasonably okay output unless the number plate is damaged or you have regional language on the number plate. Other than that, there is high accuracy.
In a year, we've collected more than three lakh images of various cars and the number of plates and we constantly keep training the system with the data that we collect. So, that way we can improve accuracy. There are a lot many things to be done we would like the government to standardize the license plates and come up with proper fonts so that the accuracy can increase.
Q. How does data collection through IoT help in optimizing Parking systems?
Our clients are B2B and not B2C. B2C is end customer; they have clear benefits of knowing where immediate parking spaces available. For the B2B clients, we provide a lot of analytics, we give them the data such as what is that the average occupancy time and based on entry/exit vehicle rates, we tell them how many parking slots are going to be available, say, three hours from now or four hours from now. This helps them in planning their parking. Other than that, you know, one of our clients, they thought their peak hour traffic is on a Sunday at five in the evening. But when we went and looked at the data, it was 11 in the morning, and why the data is relevant is because the malls try to have more manpower during peak hours. So it's important to know what the peak hour is. On Sunday evenings because the parking lots are already full and vehicles are coming in, they think that it's their traffic. When we went to look at the data, we saw that the parking lot is empty at 11 in the morning on a Sunday; the rate of arrival of the vehicle was a lot higher. So, you need manpower when the parking lot is empty, and you want to direct vehicles and see how you want to fill the parking lot rather than when your parking lot is full. These kinds of important analytics we provide to the end customer so that they can go in and see individual slots usage.
There are several times we've seen in a parking lot. You will see that the parking gate is closed and the parking lot is full. The next day we look at the data there were like 20-30 parking lots that were never used for the entire day. So how do we maximize it so that's why we put a big display outside the parking showing what is our current availability so they don't blindly close the parking lot and say it's full even if one slot is available, it's shown on the big display outside the parking lot that there is a slot available, and you can let people go.
Since there is a constant flow of vehicles in and out, very rarely does the display show parking is full, it happens very rarely. These are all the added advantage that we get to give the b2b clients that buy these products could be a mall owner airport authority or in a stadium owner, etc.
Q. How have sales been so far and how do you project the future for this market in India? What are your plans for WiiTronics?
The sales have been great. From 2017, we've been growing at more than 3x every year, and last year we grew 10x in terms of revenue. In terms of sales, the next three years, we are focusing on the North American market, the Middle East market, and the Southeast Asian market, where we are working with a few distributors to figure out what is the right path. We're trying to target a hundred crore plus revenue in the next five years. That's where we want to be. Once we do that, we'll figure out, of course, there are several other applications that we are thinking today as well on the agriculture side. So when the time is right, if the opportunity is right, we will jump into that as well.