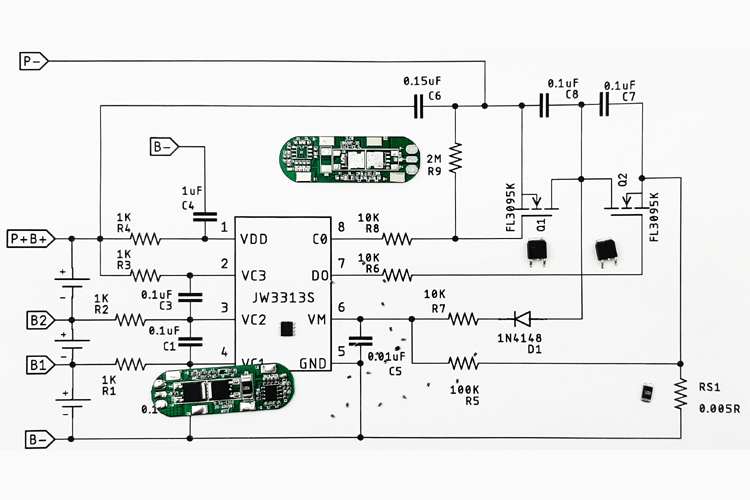
In this article, we will be learning about the features and working of a 3S 6A lithium Battery Management System or BMS along with checking out the components and the circuitry of this module. Furthermore, we have done complete reverse engineering of the module by removing all the components from the PCB and measuring all the PCB traces with the multimeter. For testing the BMS and the circuit, we have built a battery pack and we will charge and discharge the battery pack with it.
Protection Features Offered by JW3313S based 3S 6A BMS Module
A BMS is an essential component for any battery pack not only because it protects the battery from overcharge and over-discharge conditions but it also extends the service life of a battery by keeping the battery pack safe from any potential hazard. For this, we are using a 3S, 6A battery pack which houses a JW3313S Battery Protection IC. The protection features available in the Battery Management System are listed below.
- Overcharge detection
- Over Discharge detection
- short circuit detection voltage
Overcharge Condition:
When a lithium battery is charged beyond a safe charging voltage, the cell heats up extremely and its health is affected and its life cycle and current carrying capacity get reduced. To protect the cell from these types of conditions, a good battery management system must have an overvoltage built-in, and for the JW3313S IC, this is no exception. In our testing charging of the battery pack cut off almost at 12.75V which represents 4.25V for each cell.
Over Discharge Condition:
The same can be said true for the over-discharge protection. When the battery voltage goes below a certain threshold, the lithium cells get affected and the life cycle of the cells gets reduced. To protect this from happening, every BMS should have over-discharge protection and this IC is not an exception. In our testing, the cell voltage gets as low as 2.7V for each cell, and then the protection features kicked in and cut the output.
Short Circuit Condition:
Overcurrent protection in a BMS is necessary to safeguard the battery from high current load or short circuit conditions. When a short circuit condition occurs the current draw is way higher than the maximum rated current of the battery pack. This condition can affect the cell’s health or even cause damage to the cell leading to fires. This is also why there is an overcurrent and short circuit protection built into the chip.
Note: Please note that along with all the protection features, the JW3313S features hysteresis. When the overcharge protection kicks in, the battery gets disconnected and stops charging the battery. This causes the battery voltage to go slightly lower than the cutoff voltage. Now the battery will start charging again and the process will continue infinitely. Adding some hysteresis will prevent this.
Components used in 3S 6A BMS Module
Before we take a look at the schematic, here is the list of components that are required to build the 3S 6A BMS module. The main controlling IC of the board is the JW3313S Protection IC which is an 8-pin IC designed and developed by a Chinese manufacturer joulwatt. On the board, we have two FL3095K MOSFETs and a 0.005R Resistor. Other than that, we have a few resistors and capacitors as you can see in the image below. The list of components needed to build this module is shown below.
- JW3313S low-power battery protection IC -2
- FL3095K Mosfets - 2
- 1N4148 - 1
- 0.1uF Capacitors - 5
- 0.15uF Capacitors - 1
- 1K Resistor - 4
- 10K Resistor - 3
- 2M Resistor - 1
- 1uF Capacitor - 1
Circuit Diagram of the 3S 6A BMS Module
The schematic of this BMS is designed using Eagle PCB Design Software. As you can see from the image below, it's not that hard to understand the complete circuit diagram of the 3S 6A BMS circuit.
As you can see, we have the JW3313S chip that controls all the operations of the device. If you carefully observe the module, you will see separate connection terminals for P+ and B+. On the board, P+ stands for positive power input and output and B+ stands for Battery Pack Positive Input. In the PCB, these two terminals are connected to each other so we have named the connection P+B+. Next, we have the CO and the DO pins of the IC, which are pin 8 and 7 of the IC., which controls two MOSFETs. The CO gets high when an overcharger condition occurs. The DO gets high when an over discharge condition occurs. Next is pin 6 of the IC which is marked VM in the schematic and with this pin, the IC sets the over current protection of the device. This IC was designed so that it could use the internal resistance of the MOSFETs to detect the current but in this case, as you can see the manufacturers used a separate current shunt because they are using a Mosfet with high internal resistance. Pin 1 of the device is the power pin that supplies power to the IC and pins 2,3, and 4 are individual sense pins of the BMS module, and pin 5 is the ground pin of the module. Other than that, there are a couple of resistors and capacitors which are used for filtration and current limiting.
BMS Connection with Battery Pack - Fritzing Schematic
The BMS module has 4 terminals that will get connected to the four different points of the battery pack. This way the BMS module can separately monitor three individual cells and protect them from overcharging or over discharging. The schematic diagram of the BMS is shown below.
The BMS acts like three individual protection modules for three individual cells but it's a single IC that integrates all the features together to make the BMS that is able to deliver recurrent up to 6Amps.
Testing the 3S6A BMS Module for Overvoltage, Undervoltage & Short Circuit
Let's test the BMS and see if the BMS module is working as advertised in the datasheet. We are using a 3S 6A BMS module that uses a JW3313S Battery Protection IC and this IC is designed and developed by Joultech which is a Chinese manufacturer. You can check out Joulwatt website for more information on the IC.
Overvoltage Protection Test:
We started our test by arranging the battery packs in 3S configurations and started the charging process with a constant current of 600mA.
According to the datasheet, the charging process should have stopped when the pack voltage reached 13.125V that is 4.375V/Cell but to our surprise the battery got overcharged and started heating up then we stopped the charging. We don't know if this was the problem with our particular BMS board or not. We repeated our test with a new module but the result was exactly the same. You can see the testing process in the gif above.
Undervoltage Protection Test:
when the battery pack was fully charged (In our case it was overcharged), we started our undervoltage protection test.
As you can see in the above image for the under-voltage test we have removed one battery from the battery holder and replaced it with our Regulated Power Supply(RPS). Now we are decreasing the voltage and as you can see from the above gif, the BMS cuts out the load below 2.8V which means there are two protection systems that are working simultaneously. First, the BMS is monitoring the pack voltage and second, the BMS is monitoring individual cell voltage. If any one cell gets damaged the BMS will cut power.
Short Circuit Protection Test:
When the over voltage and under voltage protection test was done we need to check if the BMS was able to protect the battery pack from short circuit and overload conditions.
For that, we have connected a multimeter with the output of the BMS module, and as you can see when we short circuit the output of the module with the multimeter probe, the voltage goes to zero and you cannot see anything that is catching fire. This indicates that the short circuit safety mechanism is functioning properly.
Conclusion
The 3S 6A BMS module is a cost-efficient and highly effective module to protect LI-PO or LI-ION cells from damage. The 6A power capacity makes this device very versatile because not only this device can be used for three series packs, but it can also be used to make three series and two parallel battery packs that can be useful for many projects.