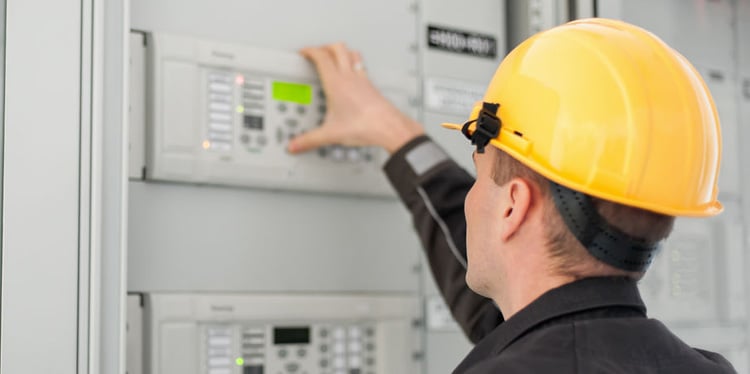
Just like the previous case studies, we bring to you one more actual incident that happened in one of the Chemical / Process Industry. We thought it was important and must be brought to notice to all concerned people working in O&M or Project in chemical industries to take due note of it as it may help other industries who doesn’t know about it.
Repeated Failure of Substation / Load center Relays
In a chemical plant there was around 250+ number of numerical relays used for LT & HT Equipment protection of a good branded MNC OEM. The plant was commissioned in 2013-14 and after 2-3 years of commissioning and full plant run-up, few of the relays in 2 substation / Load center started giving error on display. As the plant had many HT / LT spare and changeover feeder, they replaced the relay (showing error) with spare relays. But after every 2-3 month such kind of error started coming in other relays of same substation. When almost all the spare working relays were replaced, it strikes the Maintenance team, that something is not right.
Normally when such kind of repeated failure happen with Relay, Engineers mostly check the Auxiliary supply (which is normally DC) and Battery bank / Charger to see if there are any fluctuations in DC voltage or not. Because normally heavy fluctuation in Auxiliary voltage causes problem in relay and sometimes even fails the relay. But no problem was found in Auxiliary supply, battery bank / charger or even wiring.
Gas in Chemical Plant causing Relay Failure
After this HOD E&I of the plant brought this notice to OEM and said that almost 30% of relays have started showing problem in 2-3 years of installation, which is unacceptable. Taking due notice of the Maintenance team, OEM acted very promptly (As the Organization was one of their prime customers since decades) and took 3-4 relays for analysis.
After thorough analysis of Relay, which took roughly 2 months, they found the problem, which was some Gas which was there in such kind of chemical industry. And this problem was more in the 2 substation which was nearer to the chemical process area. Far end substation saw very rare such problem in relays.
Conformal Coating mandatory for Relay Protection
Now that the problem is found, what could be the solution? As few people would have guessed the solution is CONFORMAL COATING on the Electronic Circuits (PCBs) of Relays. Some Engineers among you might ask Why Conformal Coating? What does Conformal Coating do here to prevent the problem? The answer is bulleted below.
Importance of Conformal Coating
- This coating provides protection against extreme moisture, corrosive gases and agents (Like H2S, Chlorine, etc) and aggressive dust, or combinations thereof.
- It acts as an Additional layer of protection for the electronic circuits on PWBs
- Furthermore, the coating layer also offers mechanical protection against inappropriate handling and external influences.
- Conformal coating extends the lifetime of your devices in case of harsh environments.
The complete lot of Relay was replaced by OEM (Free of cost) with conformal coated relays. Now things had already settled and both sides have taken responsibility for the losses, but it could have been prevented. People involved in such projects and making such kind of detailed BOQ and Technical scope should have included that “Protective Relay must be Conformal coated” or any other Electronic item used in such kind of plant and area must be conformal coated (Many Relay OEM manual says that, you too can Google it and check) and even if that part was missed by the user, that should have been brought to Notice by OEM. In this and many such cases both User and Vendor miss such minor details. Obviously, there are many other things to work, why to go so in-depth details of equipment whose cost is not even 0.01% of Total project cost.
So, if you’re in a chemical industry and you are going for New Relay purchase, either for Projects or Spares or for Retrofitting, just ask Senior most technical personnel or OEM, whether CONFORMAL COATED RELAYS will be required in your Plant or Not? The same is valid for other Electronic Equipment’s. Remember Conformal Coating will come at some Extra Cost.
Credit of this case study goes to discussion between undersigned and HOD Electrical of a Chemical Plant recently.
About the Author:
Avinash Singh is an Electrical Engineer with over 11 years of rich experience in Electrical Maintenance, Installation, Testing, and Commissioning of all major Electrical equipments. He is specialized in bringing down Energy Cost of a Plant by reducing electricity bills and increasing energy efficiency. He also reduces plant breakdown cost by implementing proper maintenance activities during routine and shutdown. Through these Case Studies he shares his experience and challenges faced in his work routine with the readers of Circuit Digest.