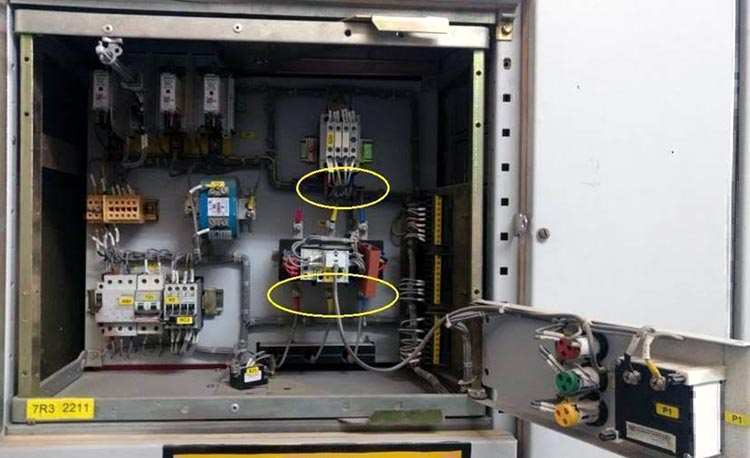
During a common operation & maintenance practice, I have noticed that in various plants for changing the direction of Low Tension motors that are below 15 KWs, the phase sequence inside the panel (the terminals below the power contactor or below thermal overload relay) is normally changed as shown in the picture above.
The main reason for changing power cable from the Relay & Power contactor side is that it will be saving more time (man-hour) than changing the cables directly on the motor terminal side. But, by doing this, we are inviting a “Near Miss” situation, which may not only damage the motor but case a server accident with life-threatening situations. This happens normally in process industries, where there are many identical motors with the same rating. These motors are used for similar applications and there are powered by the same MCC. Also, there can be similar motors for different applications in the same MCC.
Now, for example, consider an MCC where there are 9 Nos 5.5 kW DOL starter feeder, 8 is used (4 for Fan, 2 for screw conveyor and 2 for belt conveyer with gearbox and 1 is spare. Whenever the MCC is manufactured, the power cable wiring in all the feeders will be R, Y & B only (From Left to right). During O&M or plant shutdown, many times it might occur that due to plant requirements or due to some problem in the equipment we must change the direction of motors. In order to do this in an easy way, the engineer or technicians change the direction of the motor by changing the power cable sequence below the relay or power contactor. Also at times, when we are replacing the motor with a new motor and while taking a no-load trial, we found that the direction of the new motor is reversed, so we interchange the R & Y power cable below Relay or Power contactor as it is less hectic and take less time. Now our motor is running in the correct direction but inside the feeder cable is Y, R and B combination.
Now in the future, if there might be some problem in the same feeder and when it gets hard to solve the problem, the maintenance personnel will replace the feeder motor with a spare motor of the same rating to get the plant working ASAP. But, there is very little chance that he notices that in the spare feeder direction of cable is R, Y, and B. If the Maintenance Engg. or Tech. has noticed it, then they will change as per running feeder and then only give start clearance, but you will replace the running feeder with spare feeder only when there is urgency and during those times, we have seen that Engg. Or Tech. misses checking the direction inside the feeder which will result in rotation of the motor in the wrong direction. Now that rotation in the wrong direction can be hazardous or non-hazardous. It may increase the downtime, or it may damage a few components of equipment, or it may cause near-miss to the field personnel or it may cause a serious accident. Ultimately something will be lost.
Hence, we always recommend while changing the direction of Motor (For below 15 kW) from a feeder, we must do it from the panel termination side as marked in Photo. We know it will take more time but not more than 5-6 minutes than changing the direction of the cable below relay or contactor.
I am sharing this case study so that there is no Incident like this happening in any plant. You too share this article so that Technicians and Field engineers can note this point and watch out for it and yes we would like to have your comments and suggestions on such cases.
About the Author
Avinash Singh is an Electrical Engineer with over 11 years of rich experience in Electrical Maintenance, Installation, Testing, and Commissioning of all major Electrical equipments. He is specialized in bringing down Energy Cost of a Plant by reducing electricity bills and increasing energy efficiency. He also reduces plant breakdown cost by implementing proper maintenance activities during routine and shutdown. Through these Case Studies he shares his experience and challenges faced in his work routine with the readers of Circuit Digest.