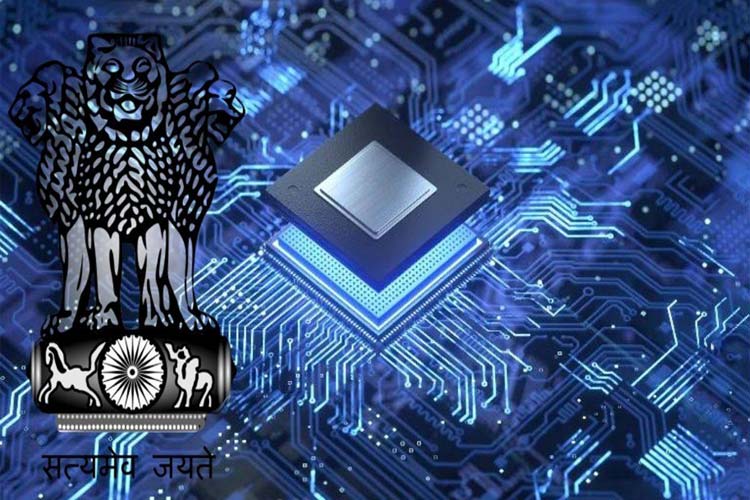
The Indian Electronics System Development and Maintenance (ESDM) cluster was developing rapidly for the past five years, which has also helped the country to export various electronic items, but, somehow the volume is still in the nascent stage and the nation is failing to become globally competitive. Various schemes and initiatives have been unleashed by the government such as PLI on various products, National Policy on Electronics, Scheme for Promotion of Manufacturing of Electronic Components and Semiconductors (SPECS), etc. However, semiconductors, which are the backbone behind every electronic item that also plays an important role in the automobile industry, were not taken into consideration by the government for the unleashing of any schemes. After several rounds of heated discussions and pressure from the industry associations and experts, the Ministry of Electronics and Information Technology (MeitY) has finally unveiled the much-awaited incentive package of Rs 76,000 Crore ($10 billion) under the production-linked incentive (PLI) scheme to perk-up the manufacturing cluster of semiconductors and displays for which the government has already started receiving applications from Jan 1, 2022. The schemes are already notified and uploaded on the government website. In order to make it successful, there is now a specialized India Semiconductor Mission (ISM), which is an independent business platform formed within the Digital India Corporation. It was begun to make India appear as an international hub for electronics design and manufacturing. The applicants beneath the display and semiconductor fab scheme can be negotiated by the ISM and also have the right to select the needed technology mix, applications, node generation, and capacity. In fact, the volume and structure of the financial assistance for the applicants selected will also be spearheaded by the ISM.
According to the government, financial assistance of 50 percent will be provided to set up the industry, which is for certain variants of silicon-based semiconductor fab. The fiscal support will be given for a period of six years from the date of approval. Now, for setting up display fabs, it was granted Rs 12,000 Crore for each FABs that will help magnetizing colossal investments in the making of TFT LCD or AMOLED-based display panels. The PLI scheme will also help in making compound semiconductors, silicon photonics, sensors, FABs, and semiconductor ATMP, OSAT facilities in the nation, while the approved units can grab financial support (capital expenditure) of 30 percent. Experts also highlighted that under this scheme, around fifteen clusters of semiconductor packaging and compound semiconductors will be formed. To make the semiconductor manufacturing dream a reality for the country, MeitY has also unleashed the Design Linked Incentive (DLI) Scheme that offers product deployment linked incentives of 4-6 percent on net sales for five years and an incentive of up to 50 percent of eligible expenditure.
Amid these optimistic scenarios, there is also a grave concern. Faisal Kawoosa - Senior Research Analyst and Founder at techArc told CircuitDigest, "The core issue is that we don’t have an Indian company having manufacturing expertise in the semiconductor industry. So, our success relies much on the interest of global companies in the semiconductor industry and at times, it may not align with their global strategy. We do have other elements, but fab is something where we aren’t present. So that challenge remains the biggest. It's very hard to say when will India be globally competitive and how. We have to first find seriously interested and promising anchors to kick start the journey."
What Lies Behind The Scheme: A Brief Economic Perspective
The subsidies that are offered under the scheme will help the semiconductor and display manufacturing companies to decrease their prices in production and thus ultimately help them in commencing their new factories and other additional facilities. The scheme is likely to terminate India’s dependence on the import of raw materials for manufacturing semiconductors and is also speculated to create new employment opportunities of over 1 lakh directly or indirectly. Experts on the other hand also opine that the government’s investment in these schemes will spike the economy of the nation because the subsidies to the organizations will play an imperative role in developing India as an international den for electronic items.
But, the point to be noted is that the subsidies to any organizations are even questioned by many because a load of subsidies will fall prey to the taxpayers whose incentives on their work would be reduced as taxes will escalate on them and in fact, the resources could be misallocated. Most interestingly, in any market economy, the investment decisions are taken according to the likeness of the consumers or the people because if they do not require certain items then companies will not invest in them to avert losses. Therefore, the success of making India a global hub for semiconductors under this PLI will depend on various other factors other than subsidies. The top-notch setup of institutions plays an important role in a nation because an investor's center of attraction is a trouble-free business operation. A favorable atmosphere has to be offered by the government in order to pull in more investments.
The Current Semiconductor Challenges Worrying the PLI Scheme
In 2020, the semiconductor market size was valued at $427.6 billion and is expected to reach $698.2 billion by 2026 at a CAGR of 5.9 percent during the same period. Along with this, increased investments in memory devices and Integrated circuit components are driving technological improvements in the semiconductor sector. While this is good news, semiconductor and component manufacturers still face challenges related to managing complex networks of multi-tiered original design manufacturers (ODM) relationships, distributors, contract manufacturers, and so on.
Semiconductor manufacturing is dependent primarily on two aspects - Technology and Capital. It is a highly capital intensive activity and also needs constant technology updates and sustained R&D. Apart from this it also needs a good amount of infra support- both hard infrastructures like access to well-developed land with very easy access to Ports and airports as well as soft infrastructures like availability of clean water and totally uninterrupted power. According to India Electronics and Semiconductors Association (IESA), India is getting very competitive in the infra aspects, both hard and soft, over the last 4-5 years of sustained efforts by the central and many state governments. Now, the next challenge is in finding a global technology partner to invest in India and give it a kickstart. This also needs significant capital investment commitment not only for wafer fabs but also for Outsourced Semiconductor Assembly And Test (OSAT) and ATMPs.
Justifying the statement above, Sathish Kumar Ganesan, Vice President & Global Delivery Head – Semiconductor Sector, Cyient told exclusively to CircuitDigest, “On the support systems such as OSAT and infrastructure, we have only one OSAT in India, and there are challenges in infrastructure such as continuous power, water, etc., to maintain such manufacturing units. While we can create such manufacturing units by addressing the above factors, but nurturing the ecosystem is the most critical aspect of sustaining the growth in this industry. The supply and demand in the semiconductor market are always varying though it is mostly on the upside. So, creating an ecosystem that can withstand such market pressure yet continue the operations and keep up with the technology roadmap would be the key.”
Ganesan also added that India should work on short/mid/long term goals to reach the top in this segment. (1) short term goal should be to ramp up the manufacturing services sector (OSAT, test facilities, infrastructure), which will make us enter into the key ecosystem and it will enable us to learn and grow along with the roadmap of this industry; (2) mid-term goal should be to set up the core technology nodes (16nm to 40nm) to cater the majority of the market in terms of industry segment but do it aggressively and quickly to keep along with the roadmap of this industry; (3) long term goal should be set up the complete ecosystem including high-end technology nodes by thereby accumulating all the learnings from short/mid-term goals as it would have created the complete ecosystem for scalability.
Furthermore, many experts also believe that should start looking at alternate technologies such as Silicon Photonics, Gallium Nitride, etc. as these technologies are still evolving and there is good scope to enter at an early stage where the Indian ecosystem of strong industry/academia talent pool can contribute and become a strong player in this industry segment.
The biggest challenges faced by electronics manufacturers in the country have been due to the ITA-1 agreement of WTO which was implemented in April 2005 and it brought all ICT products and their inputs under 217 tariff lines to zero customs duty. This had a huge adverse impact on the electronic components industry, the majority of which were brought to zero duty and thrown open to global competition. According to an exclusive report of the Electronic Industries Association of India (ELCINA) to CircuitDigest, it is widely accepted and validated through industry research and inputs that electronic component manufacturing in India faces a cost disability of 10-12 percent and semiconductors are no exception. In fact, semiconductor manufacturing requires very high value addition and as a consequence, faces the highest level of disability costs.
Post-implementation of ITA-1, investments in electronic components manufacturing including semiconductors dried upbringing the development of this sector in India to a halt. This has pushed us further down reducing our competitiveness with global leaders in this domain and has further widened the technology gap. As semiconductor manufacturing is characterized by high capital output ratio, the entry barrier for new entrants has become higher and our aspirations to grow this critical sector of electronics have remained unfulfilled. Demand for semiconductors is growing as more and more electronic products become “intelligent” and require more processing and logic capability as well as data storage and processing.
Rajoo Goel, Secretary General of ELCINA, said "The government of India realised the criticality of a strong semiconductor eco-system and announced the first Scheme to attract investment in a Fab almost 10 years ago. Unfortunately the same did not succeed as it was for large Fabs which require a strong supply chain and ecosystem which we do not have. More recently more aggressive Schemes have been announced under the National Policy on Electronics in 2012 and 2019 which have been quite successful in establishing equipment manufacturing and infrastructure by way of Clusters.”
“Apart from announcing Production Linked Incentive (PLI) schemes for various electronics sectors, MeitY has recently announced a comprehensive policy program for promoting semiconductor manufacturing in the country. This program, worth over Rs 76,000 Cr, aims to not only provide incentives to semiconductor fabs but also to semiconductor design and OSAT/IC Packaging. The move seems brilliantly timed as the world is currently haunted by the shortage of semiconductors. Moreover, as the semiconductors are the brains behind modern electronics, they are of strategic value to all the countries,” he added.
The Type of Semiconductors India Currently Produces
Now, which are the areas in the semiconductor regime where India needs to strengthen its manufacturing with the assistance of this PLI scheme. The country has already begun producing a lot of electronic items, some of which are also going for export and in fact, some portions of semiconductors are also being produced. Some of the important electronic goods such as mobile phones, engine control units, LED lighting, notebooks, GPON, CCTV, energy/smart meter, and flat panel displays are not made in India as such, which are speculated to capture 68 percent of the Total Addressable/Available Market (TAM) in the electronics market, according to a report of Frost & Sullivan. For instance, while making a mobile phone, all the components and PCBs are imported and because of no/low imported duty, the component ecosystem is not developed. Along with this PLI scheme, support from the government needs to be provided in terms of import duties and sufficient tax benefits to smoothen the home-grown companies.
Currently, India is manufacturing a very small fraction of its demand for semiconductors in the country which is being done by a handful of companies such as CDIL, SPEL Semiconductor, Ruttonshah International, Vishay Semiconductors, Semikron, and a few more, though all of these are small by global standards. Further, they largely manufacture discrete semiconductors, rectifiers, thyristors and provide value-added services. The only Semicon fab in the country is SCL at Mohali which again is a small facility and now largely caters to the space sector. It is often not understood why India has not been able to establish a stronger semiconductor industry in the country, in spite of the strong demand which is driven by the growth of the ESDM market in the country.
Highlighting the statement above, K Krishna Moorthy, President & CEO, IESA, told, "India currently makes some semiconductors for its strategic needs in its fab in SCL Chandigarh. These are parts that are of medium complexity and the technology node which has some limitations for building parts for many of the commercial applications. However, the government of India has announced a major policy initiative on Dec 15th, 2021 to upgrade the SCL Fab with technology collaboration and /or JV route. Apart from that the newly announced policy has also set very realistic targets of getting newer technology node fabs and ATMP's to start green field enterprises in India and we expect the semiconductor manufacturing landscape to change very positively in the country in the next 18 to 36 months. All these will bring in new technology and associated newer equipment to the country, be it in wafer fabrication or in Assembly or Test.”
Why It is a Nightmare to Setup a Semiconductor FAB in India?
With the unleashing of this PLI scheme, this is not the first time that the Indian government tried to craft a semiconductor FAB cluster in the country because fifteen years back, SemIndia, a Bengaluru denned startup associated with the government of Andhra Pradesh to begin a wafer manufacturing special economic zone (SEZ) with an investment of $3 billion, but unfortunately, the government incurred a huge loss and the venture turned a total failure. And during the same time, the government approached Intel to commence a unit, but instead it went to China. Several proposals were given to set up FAB units, but it did not happen due to lack of funding, intelligent technically skilled workforce, and unavailability of natural resources.
The manufacturing of semiconductors requires both back-end assembly and front-end FAB manufacturing. Although there are developments in back end - packaging and testing, there are only a handful of global firms that make chips on a large scale, and most importantly, they are not available in India. According to experts, the market or the value of chips imported in FY 21 is around $12 billion. Experts believe that in South Korea, China, and in Taiwan, the government has offered the initial investment, which India also needs to do, and apart from that, there should be tax reduction rates coupled with lower interests. According to IESA, the government has to offer significant incentives. For instance, if the government offers $40 billion out of the $100 billion to begin a FAB, then still there is a gap of $60 billion. The investors must be boosted with confidence that they would get profits from their business operations in India. This is still a huge gap.
Apart from that gallons of freshwater are required, unbroken and continuous supply of high-speed electricity, expensive operations, and the requirement for periodic replacement of technology. Of late, the US Semiconductor Industry Association stated that since 2020, Taiwan is spearheading the FAB cluster with a share of 22 percent, which is then followed by South Korea 21 percent, Japan 15 percent, China 15 percent, US 12 percent, and Europe 9 percent.
Highlighting the intricacies of setting up a FAB unit in India, Goel further said, “While some of the key reasons have already been explained above, it is widely believed that a semiconductor fab can only to be established if there is a downstream industry in the form of an IC packaging/OSAT sector which can support the Fab by consuming its wafers. There is no doubt that India missed the semiconductor bus many years ago but there is a big opportunity waiting to be grabbed by stakeholders who understand that the changing geo-political conditions have led us towards a new scenario with buyers looking for alternate sources.”
However, it is not an easy task to become globally competitive in the sector because apart from the demand which already exists in India, a strong semiconductor ecosystem requires a strong supply chain, infrastructure, huge investments, and most of all skills and technology to succeed. While we expect to see some green shoots in the next couple of years, it will take anywhere between 5-10 years to achieve global competitiveness in a few sub-segments. If we wish to succeed, we need to pursue and persevere with a consistent supportive policy.