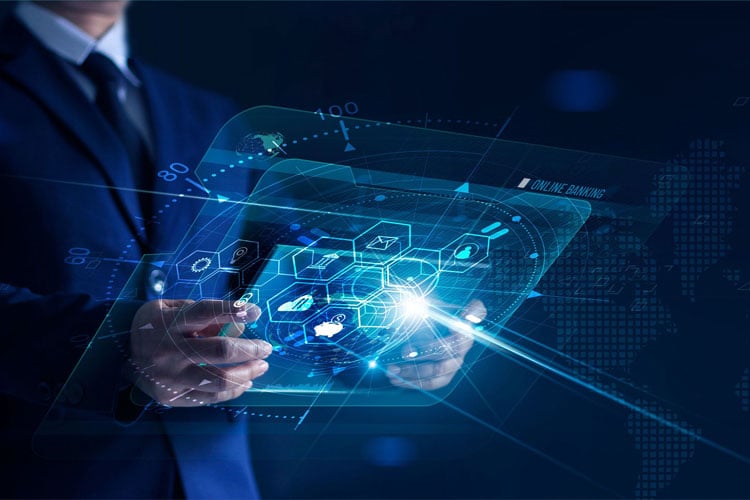
Global spending on the Internet of Things (IoT) should reach $1 trillion in 20221, nearly doubling the 2021 market size. Surprisingly, though, it is not technology or even web-based services leading to the adoption of connected technology. Instead, HFS Research found that industrial manufacturing exhibited the highest adoption rate (85 percent) among surveyed businesses.
There are well-known benefits to industrial manufacturing, adopted over time as standalone functional improvements, such as production rate optimization and increasing the data collected to improve operations insights. But as manufacturing takes a more holistic view to integrating the information technology (IT) infrastructure with operations technology (OT) to create the smart factory, manufacturers can realize the full benefit of this "industrial IoT" (IIoT) propelling their industries forward.
There are several ways the IIoT enables the intelligent factory (with some remaining challenges). However, before exploring those, it is worth reviewing the characteristics that differentiate a smart factory from a traditional one.
Smart Factory Characteristics
The simplest difference in the smart factory is the confluence of digital information and physical assets that extend manufacturing capabilities. These Cyber-Physical Systems (CPS) incorporate additional sensors and automate controls into manufacturing processes, leading to three principal characteristics: asset connectivity, performance/trend visibility, and operator autonomy.
Integrated digital and physical tools connect operators with the equipment. This connection provides them a real-time, virtualized picture of the equipment status in a monitor. By enriching the insights into how the process is running during operation, the operators can monitor the processes closer while spending less active time watching the machines run, increasing autonomy.
Another smart factory characteristic is data collection and requisite analysis that engineers need to decode process operation. In addition, there must be on-site or cloud-based servers to process and house the higher volume of data, a feature legacy infrastructure did not need.
Benefits of the Smart Factory
The IIoT is driving this 85 percent adoption rate in industrial manufacturing due to its many advantages. The first layer is the historical gains manufacturers realize from using AI and machine learning as part of their process:
- Improved inventory control – recording insights into production flow enables the dual benefits of lower inventory—a high-priority key performance indicator (KPI) historically—and higher resilience/component availability (a known drawback of just-in-time (JIT) production). Analytics can optimize the balance while de-risking supply. This improvement reduces order management and material handling costs.
- Lower production cost through higher Overall Equipment Effectiveness (OEE) – using collected data and AI, the smart factory adjusts production flow to maximize uptime, identify patterns, and predict demand variations. This approach also optimizes assets for improved production and energy efficiencies.
- Improved quality and lower scrap – collecting substantial data during production allow operators insight into equipment lifecycles. This view enables them to uncover trends in tool wear and predict the next (likely) point-of-failure. In addition, predictive maintenance reduces both repair cost and downtime to execute it, a significant advantage when considering run rates and targeting process waste reduction through lean initiatives.
With these three apparent improvements, the IIoT further enables the smart factory by promoting decentralization. Through the recent global supply chain disruptions, businesses pivoted to a more vertically integrated model to reduce supplier qualification time and gain control over quality and component delivery. As more companies implement IIoT tools down the supply chain, connecting suppliers' assets to a shared network can benefit an intelligent factory without vertical integration.
Furthermore, adding this capability increases the ability of the supplier to work with other companies by affording new partners insights into process capabilities themselves without time-consuming quality audits or process reviews. Increasing IIoT throughout manufacturing also facilitates creating industry standards to assure companies that a new partner has adopted the new capabilities properly.
IIoT also helps companies create new business streams, such as improved customization offerings and product—or manufacturing-as-a-service. Increased data collection and analytics will deliver quality through continuous improvement across the manufacturing process, no matter the application.
Finally, integrating IT with OT streamlines product development or process improvement/troubleshooting initiatives by leveraging virtual simulations to speed up iterative changes before cutting a physical part.
Smart Factory Challenges
Despite the numerous advantages of the IIoT-enabled smart factory, businesses have some challenges they must overcome.
The first is the initial cost of adding the data collection and digital processing tools. However, as mentioned, these improvements can lead to cost reductions in other aspects of the manufacturing and supply chain, so the business case should consider the total impact of the investment, including modularizing data collection/processing tools and reduced inventory and downtime.
Another challenge is integrating new technology with legacy infrastructure. While building a new integrated architecture is typically a simpler process, it may not be practical. Retrofitting a factory with IIoT tools should consider non-negotiables like connectivity, network resiliency, and cybersecurity, all of which become more critical with higher reliance on a connected factory.
Finally, it is important to add or contract the skill sets to implement the technology appropriately, including projecting network usage increases and data processing capacity.
Conclusion
While businesses must always overcome challenges when implementing a disruptive shift to an industry, industrial manufacturing is sprinting into Industry 4.0 by near-universal adoption of the IIoT. As a result, manufacturers can realize optimized inventory, lower operating costs, and higher quality through improved connectivity, visibility, and autonomy. In addition, the IIoT provides the opportunity to move toward a standardized, decentralized, connected supply chain. Along with faster product and process development improvements, that end state has created an exciting inflection point for industrial manufacturing.
About Author
Adam Kimmel has nearly 20 years as a practicing engineer, R&D manager, and engineering content writer. He creates white papers, website copy, case studies, and blog posts in vertical markets including automotive, industrial/manufacturing, technology, and electronics. Adam has degrees in chemical and mechanical engineering and is the founder and principal at ASK Consulting Solutions, LLC, an engineering and technology content writing firm.
Original Source: Mouser Electronics