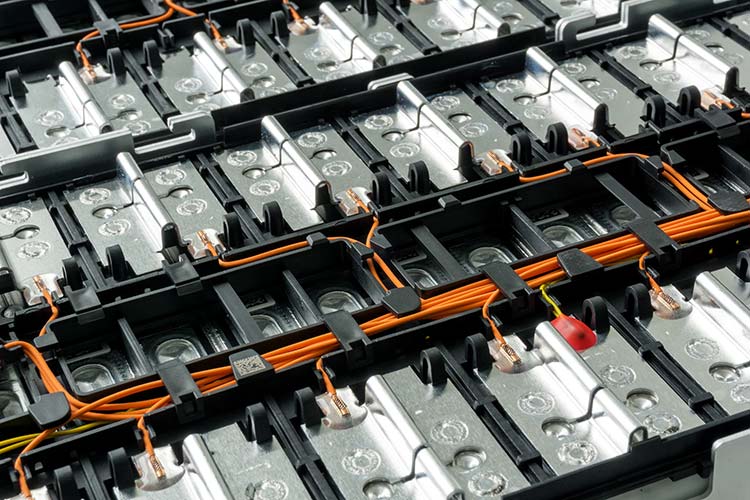
Lithium battery systems are increasingly moving to higher capacity and increased voltage levels as the trend toward electrifying mobility, tools, and industrial equipment continues. Though excellent for enhanced mobility and productivity, these higher battery cell counts and voltage levels mean that battery management system (BMS) technology needs to advance to accommodate this trend. Given the complexity, increased cost, and safety requirements of the latest electrified devices and equipment, BMS must also have greater capability and features for enhanced communication functions, fuel gauging, cell balancing, timing, and accommodating various lithium battery chemistries.
Primer On Lithium Battery Technology
Lithium batteries are energy storage devices stored within chemicals that are trapped in battery cells with a positive electrode (cathode) and a negative electrode (anode). Lithium-ion batteries are based on materials with layered crystalline structures where the lithium ions can migrate between layers, known as intercalation compounds. The discharge cycle of a lithium-ion battery sees the lithium ions migrate from the anode to the cathode, which induces electrons to move in an opposing direction from the cathode to the anode. This allows for energy transfer for the battery's terminals and the electrical load. The voltage level and current output at the lithium battery terminals depend on the number of lithium ions that are migrating. When voltage levels begin to sag, the current is reduced, as the number of lithium ions available to migrate decreases.
The charge cycle of a lithium battery works in the opposite way, where inducing a voltage at the terminals of the lithium battery causes the lithium ions to reverse their migration across the electrolyte and re-embed within the negative electrode. Modern lithium batteries can be made of a variety of different intercalation compounds for the cathode, the most common being lithium-ion (li-ion), lithium-ion polymer (LiPo), and lithium iron phosphate (LiFePO4). The negative electrode of lithium batteries is often graphite. However, ongoing experimentation and efforts exist to develop higher performing batteries using various anode, cathode, and electrolyte materials and technologies.
Given the highly reactive nature of lithium batteries, it is necessary to monitor the batteries' temperature, current, and voltage characteristics during charging and discharging. Without proper battery monitoring and control, a lithium battery cell, even if it is made of "safer" or more stable lithium compounds, may reach a state of thermal runaway. This runaway could cause damage to the cell electrodes or housing, possibly leading to an uncontrolled chemical reaction where the battery cells could catch fire or even explode.
Many lithium battery systems are composed of several lithium battery cells in series to reach higher voltage levels and in parallel to achieve higher current output levels. Given the tolerances in fabrication, inconsistent aging of lithium batteries, and many other factors, the discrepancies between the battery voltage and current characteristics can result in several possible performance degradations or battery damaging conditions. For instance, if a battery cell is in series or parallel to other lithium battery cells and isn’t performing to specification, that cell may act as a load. This results in the degraded battery drawing current, while the voltage of the other cells may be reduced below a safe threshold.
These discrepancies are why cell balancing technology is critical in lithium batteries with more than one cell. Systems that incorporate battery monitoring, control, and cell balancing are commonly known as battery management systems (BMS). As lithium battery technology has advanced and become more widely used, BMS technology has also advanced to ensure greater safety, performance, and longevity for lithium battery systems (Figure 1).
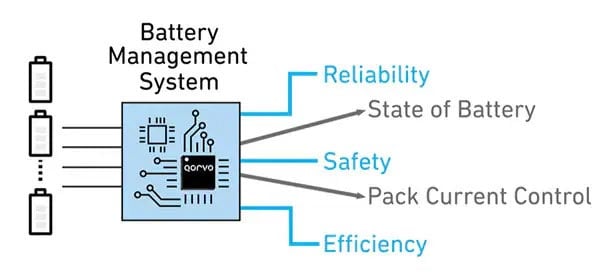
Trends in New Lithium Battery Systems
For many power garden tools, construction tools, mobility, and industrial equipment, gasoline and corded electric systems have dominated the markets for over a century. However, the developments in lithium battery technology have led to the transcendence of electric battery-powered tools for everything from mobility to equipment to everyday necessities. Examples include battery electric string trimmers, blowers, chainsaws, SDS drills, scooters, e-bikes, motorcycles/mopeds, concrete saws, and portable welders. These battery electric systems are commonly made with 20V, 40V, 60V, and 80V, with higher voltage levels likely becoming popular.
The success of battery-operated tools and mobility systems naturally results in even higher performance, which necessitates increasing the voltage levels, capacity, and current capability of the lithium battery systems powering these devices. Due to lithium technology's cell voltage level limits, increasing the number of cells in series is the only way to reach higher voltage levels. Drawing too much current from or dumping too much current into a lithium cell can result in cell damage and catastrophic failure. Increasing the current output/input capability will increase the number of lithium cells in parallel. Therefore, enhancing the overall capacity of a lithium battery system may require even greater numbers of parallel series of cells or much higher capacity lithium battery cells.
Intelligent BMS Step Up to Meet the Challenge of Modern Lithium Battery Systems
Given that lithium battery systems are being developed to push the performance of battery electric systems for various applications—from electric vehicles (EVs) and electric backup generators to autonomous mobile robots—BMS technologies must also advance to accommodate these new higher voltage levels, capacity, and current input/output battery systems.
Qorvo's intelligent BMS (PAC22140/PAC25140), with an integrated microcontroller unit (MCU) and cell balancing technology (Figure 2), is a natural evolution of simple BMS that merely monitored the battery and shut off charging when either temperature or voltage levels reached unacceptable thresholds. These new BMS chips can monitor 10-series (10S) to 20S li-Ion, Li-Polymer, and LiFePO4 battery packs, including the most common lithium battery technologies. Qorvo’s new BMS include a FLASH-programmable MCU (Arm® Cortex®-M0) with power management, current/voltage/temperature sense, drive circuits for charge/discharge FETs, and protection fuses. Moreover, these intelligent BMS also include built-in UART/SPI, I2C/SMBus, and even CAN communication on some units.
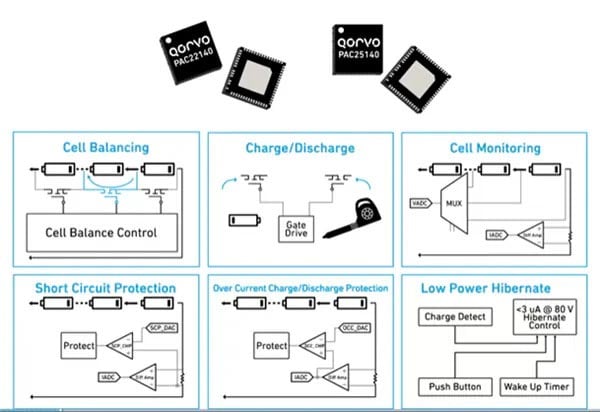
Since it is essential to evaluate new BMS chips and familiarize oneself with their programming and control aspects, Qorvo provides an evaluation kit (PAC22140EVK1 and PAC225140EVK1) for these chips.
These evaluation kits are complete hardware solutions for evaluating the new intelligent BMS devices and also enable solution development with access to all of the device's signals and all the necessary circuitry to energize the MCU and internal peripherals (Figure 3).
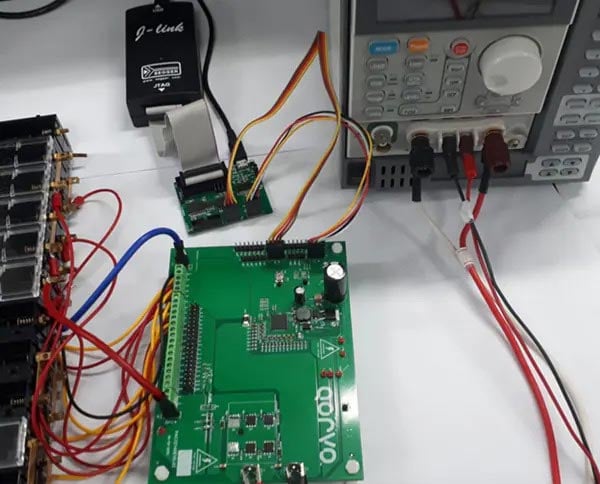
Conclusion
The growth in popularity and utility of lithium battery electric systems has pushed the boundaries on voltage, capacity, and current capability. With greater series cell counts and higher user performance expectations, these new battery electric systems must be appropriately managed and cell-balanced with the latest intelligent BMS technology. Qorvo's new intelligent BMS technologies aid in developing new BMS solutions that augment present lithium battery technology with more efficient cell balancing, monitoring, and protection features.
Original Source: Mouser
About the Author
Principal of Information Exchange Services: Jean-Jacques DeLisle Jean-Jacques (JJ) DeLisle attended the Rochester Institute of Technology, where he graduated with a BS and MS degree in Electrical Engineering. While studying, JJ pursued RF/microwave research, wrote for the university magazine, and was a member of the first improvisational comedy troupe @ RIT. Before completing his degree, JJ contracted as an IC layout and automated test design engineer for Synaptics Inc. After 6 years of original research—developing and characterizing intra-coaxial antennas and wireless sensor technology—JJ left RIT with several submitted technical papers and a US patent.
Further pursuing his career, JJ moved with his wife, Aalyia, to New York City. Here, he took on work as the Technical Engineering Editor for Microwaves & RF magazine. At the magazine, JJ learned how to merge his skills and passion for RF engineering and technical writing.
In the next phase of JJ’s career, he moved on to start his company, RFEMX, seeing a significant need in the industry for technically competent writers and objective industry experts. Progressing with that aim, JJ expanded his companies scope and vision and started Information Exchange Services (IXS).