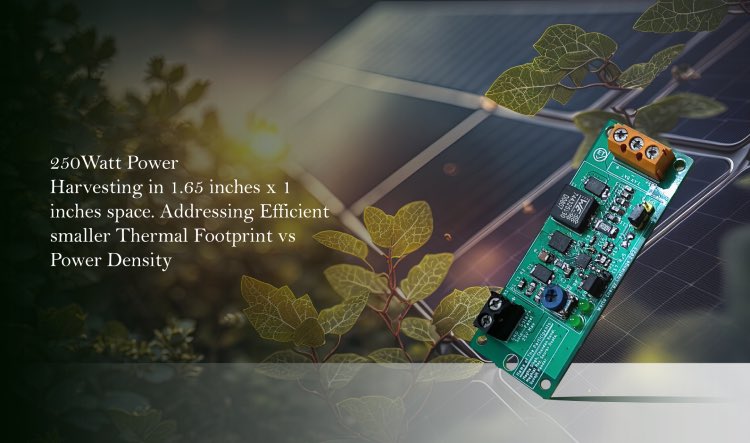
We are heading towards a Greener revolution where each and every one of us is looking for efficient energy harvesting without impacting the environment. Out of different Energy sources, solar energy is the easily available and probably lasts the longest, atleast 5 Billion years before it runs out of fuel and converted to a White Dwarf Planet.
Out of different Solar harvesting topologies, like MPPT, PO, MPP, the major challenge is to harvest energy in small space with high current density. In this World Energy Challenge 2023 we are accepting the challenge to create a circuit that could produce up to 250 Watt Energy from a solar panel grid within a 42mm x 26mm Space Which is 1.65 inches x 1 inches which is pretty small. We will also not limit the circuit for a particular type of battery, instead, this small, miniature circuit could charge Lead Acid battery/ Lithium Phosphate, LiFePO4, Lithium Polymer etc. It is not to mention that the battery voltage can be changed to compensate with the 1S, 2S, 3S Batteries etc.
Overview of the Project
The challenge that we are addressing to overcome is the Size vs Power Density. We are looking for the enormous opportunity in this Smaller rather micro size of electronics product world (Moore's Law). This project is targeted for the Industrial environment rather than the DIY and Hobby World and with a point of view of practical implementations.
To overcome this challenges we need to deal with following things -
- Small size means low copper dissipation area, Thermal Dissipation is the Challenging task
- Tracks thickness for the High current Operations
- GND Bounce issue for Low Copper Pouring Area.
- High stray Inductance on Components Joints
- Choosing the proper components to reduce unnecessary effort.
Specification of the Solution is as follows -
- Input 5-28V Solar Panel
- MPPT Setting Options
- High Efficiency at least 85%+
- Can be configured for Different Battery Type
- Can be used for Different battery combinations
- Options to Enable/Bypass Battery NTC monitoring for Safe Charging
- Options for Charge termination time Enabled or Disabled
- Battery Absent Detection during Charging. Important for Industrial Operations due to the Disconnection and Battery connectivity failure is common.
- Fault and Working LED Indications
- Upto 10A Charge current.
How We Overcome These Challenges
- Done Proper PCB Design and Manufactured using 70 um Copper thickness on external layer and 35um on Internal layer. We Targeted 4 Layer PCB Design
- Used Plane Connection in different layers to compensate with High current Track
- Adequate Vias stitching done along with Thermal Vias on bottom of the Driver.
- Added Thicker Thermal Joints on Power Electronics components to reduce stray Inductances
- Selected Low DCR Inductor and Low RDSon Power TrenchFET to reduce the Thermal dissipation. Used Dual N-Channel Mosfet in Single package (SO-8) To reduce space and increase maximum capabilities and small thermal footprint.
List of Components / Bill Of Materials
Qty |
Value |
Package |
Parts |
2 |
Berg Pin Header |
1X03 |
JP1, JP2 |
1 |
2P Screw Terminal 5.08MM |
W237-132 |
X1 |
1 |
3P Screw Terminal 5.08MM |
W237-133 |
X2 |
1 |
0.004Ohm / 1 Watt |
R2512 |
R12 |
5 |
0.1uF/50V |
C0603 |
C6, C9, C10, C15, C16 |
1 |
0R |
R0603 |
R13 |
1 |
100R |
R0603 |
R7 |
1 |
100k |
CA6V |
R6 |
1 |
10Ohms / 0.25W |
M1206 |
R8 |
1 |
10R |
M1206 |
R3 |
1 |
10uF 35V |
C1210 |
C8 |
1 |
180k |
R0603 |
R14 |
2 |
1k |
R0603 |
R10, R11 |
6 |
1uF/35V |
C0805 |
C1, C3, C4, C5, C7, C14 |
1 |
2.2R |
R0603 |
R9 |
2 |
22pF/50V |
C0603 |
C2, C17 |
3 |
22uF/35V |
C1206 |
C11, C12, C13 |
1 |
3.3uH |
WE-HCI_1050 |
L1 |
2 |
3.9Ohms / 0.25W |
M1206 |
R1, R2 |
1 |
30.1k |
R0603 |
R5 |
1 |
5.23k |
R0603 |
R4 |
1 |
64k |
R0603 |
R15 |
1 |
QFN50P350X350X100-17N |
U1 |
|
2 |
GREEN |
LED3MM |
LED1, LED2 |
2 |
497-10102-2-ND |
D1, D3 |
|
1 |
TRANS_SI7288DP-T1-GE3 |
Q1 |
|
1 |
SOD523 |
D2 |
Important part of the circuit
Schematic Section
Let's go through the important part of the circuit.
The circuit is incorporated with the major driver BQ24650 Which is a MPPT Solar driver / Controller. The circuit has C4 Which is used for internal voltage reference and Regulation filter. The VREF Junction will be 3.3V when the Internal circuit starts working. We can also see that the BQ24650RVA has the STMicroelectronics Diode BAT54KFILM which is a Bootstrap Feeder from the REGN regulation of the IC.
The Input of the IC is protected via a 10 Ohms 0.25Watt resistor for Inrush Current Limiting and the C3, an 1uF capacitor for filtering the VCC input.
Both 10 Ohms and the 1uF Capacitor creates a startup delay due to the RC Time constant which is insignificant here.
We are using SI7288DP-T1-GE3 Power Trenchfet. This Mosfet is actually two mosfets in a single package. Not to mention that this will reduce the space margin. As per the design, the internal mosfet driver circuit inside the BQ24650 has a 6V Gate drive. The RDs ON resistance at 6V Gate drive is close to 0.016 Ohms at 25 Degree Temperature. It is not used in 25 Degree temperatures. Crucial things matter a lot in Industrial design. For example, in the worst case scenario, if the device is placed in a IP65 Rated box without air contact (closed enclosure) outside with full sun, the temperature rise can become 40 Degree at full load. The RDSon will go to 0.02 Ohms. If the current of the battery charge is 5-6A (Adequate for most of the applications)
The Power Dissipation will be = I x I x R = 6 x 6 x 0.02Ohms = 0.72W.
R12 is a very important component in this circuit. Not only setting charge current, this also sets the Precharge, charge termination etc by incorporating the Lead Acid and Lithium charging chemistry in one single solution. Since the full scale differential voltage range is 40 mV, we chose the 0.004 Resistor to compensate with the 10A charge current at full spec. Well, the wattage of the resistor is important for such high current. At 10A the power dissipation will be 10A x 10A x 0.004 = 0.4Watt. We chose 1W of resistor. The battery precharge is determined by the 1/10th of charge current where precharge regulation is 4mV. Here the precharge is 1A.
Next is the Inductor. We selected a 3.3uH 12A Inductor from Wurth Electronic. The Inductor has DCR with only 5.9mR. Continuous current dissipates a very low amount of heat on the Inductor. Similar low cost inductors can also be used but the DCR should be low enough.
The diode STPS15L30CD was originally planned and used for the project, during testing stage the diode was replaced with PDS1040. The schottky diode PDS1040 is used for protecting the mosfet from transient kick back.
Generally, Battery comes with a NTC thermistor. Charging a Lithium battery in too Hot or too Cold condition is not a good thing to do as it destroys the internal cells and Resistance of the battery. An NTC input is available in this board that could be used for the board operations. However, for the batteries not having this feature, a jumper condition is added to use that voltage divider instead of the battery temperature sensing externally.
Input of the circuit is using a Resistor / Capacitor snubber. This is for unintended solar flares and transients. The 100K MPPT setting potentiometer is also connected to create a voltage divider. It is worth mentioning that the MPPT regulation voltage is 1.2V. This potentiometer needs to be set at full sun condition and the device will follow the MPPT tracking from that particular point. It is worth to mention, each solar panel has a unique V-I and V-P curve and experience of this is important to create a perfect MPPT tracker.
This is the charge termination setting that could enable charge termination ON or OFF. By Default we are using Charge Termination to OFF mode. It is important to enable it in actual scenarios as this will ensure to detect the battery fault conditions. The sense resistor determines the termination current with a 4mV regulation. For 0.004 Ohms, it is 1A.
The Battery feedback voltage. This section sets the battery voltage. BQ24650 uses 2.1V voltage regulation across the VFB pin. The resistor divider needs to be done in such a way that it should provide 2.1V after the voltage divider in actual point. In this application we used a 4.2V battery in 2S configurations. Thus, 8.2V (Lower than 8.4V for longer battery life) is done. In the case of Lead Acid battery this needs to be set as 2.3V-2.45V per cell.
PCB Design Section
This is a special type of High Current Design with High energy density. It is worth remembering that adequate PCB design tactics are important to drive this PCB. To start with we selected following layer tactics -
1.6mm PCB with 4 layers and with 70um on external layers, 35um on internal layers.
The major Power Dissipation happens on external layers as the heat is dissipated through the air. Internal layers are not for heat dissipation as those are not connected with air contact. Air is a heat sink. Just a side note, this is a major challenge for the PCBs used in outer space, we live on earth and have this boon.
TOP Layer - PWR-SIGNAL-GND
Layer - 2 - PWR-GND
Layer - 3 - PWR-GND
Bottom Layer - PWR-SIGNAL-GND
Top Layer with all the signal and Thicker GND Plane.
2nd Layer as a Power and GND Layer
The 3rd Layer is PWR and GND Layer. Mostly the GND Layer.
Bottom Layer with PWR, GND and Signal.
We made a star based connection to use the filter capacitor on maximum operation output. The grade of capacitor is important as it will withstand high ripple current as well as the High filtration.
We used Thick connectivity on the copper pouring across the power element reducing the stray inductance as much as possible. The Major driver section uses Thermal vias as well as the proper routing tactics.
The Sense resistor uses Differential coupling. A sense resistor routing is a critical thing to get proper output reducing transient loss as the entire closed loop depends on it. We handle this proper standard such as Kelvin sensing technique with identical length matching. The sensing should be accurate as simple changes on this section make the entire device to operate could turn to unnatural behaviours.
PCB Order, Components and Assembly
We ordered components from Digikey and they provided the components on time. Their support is amazing.
We received the PCBs after the fabrication. We added the proper holes for the fitment.
Since the unavailability of the stencils and assembling a single PCB is very costly, we move forward with the in house hand soldering. It was a difficult task, however, somehow we managed after lots of testing, looking for a short.
The working Video and the demonstration is given on the below video link. The video is first tested with the Solar Panels of 50W x 4 and then the demonstration is done.
Project Team Members
- Megha Singh
- Meghlal Roy
- Subhajit Kandar
- Chandan Kandi
- Sourav Gupta